The energy challenge in cement manufacturing
Reducing energy consumption is a core goal for all cement producers, sitting alongside alternative fuels, reduced clinker content and carbon capture as one of the four pillars of decarbonisation. As we look to the future, when new emissions abatement technologies will skyrocket energy use once more, that goal becomes ever more important.
While automation and digitalisation have a critical role to play in optimising energy use, advances in mechanical equipment are often focused on reducing energy consumption – meaning there are many equipment upgrades that could help lower your energy bills, providing a relatively swift ROI in exchange for minimal disruption to your process. By optimising key process areas—grinding, dosing, preheating, and more—plants can reduce energy costs while improving operational performance. But where should they start?
Easy upgrades to optimise the grinding process
“One of the biggest sources of inefficiency in cement grinding is overgrinding,” explains Nick Litzenberger, Design Engineer. “Every extra pass through the mill consumes energy but does not necessarily improve product quality. This is especially critical in Type 1L cement, where fine limestone particles can lead to excessive power consumption and reduced throughput. Many cement plants still operate second-generation separators, which lack the precision of modern designs. Upgrading to a third-generation separator can optimise particle size distribution, lower energy use, and boost mill output.”
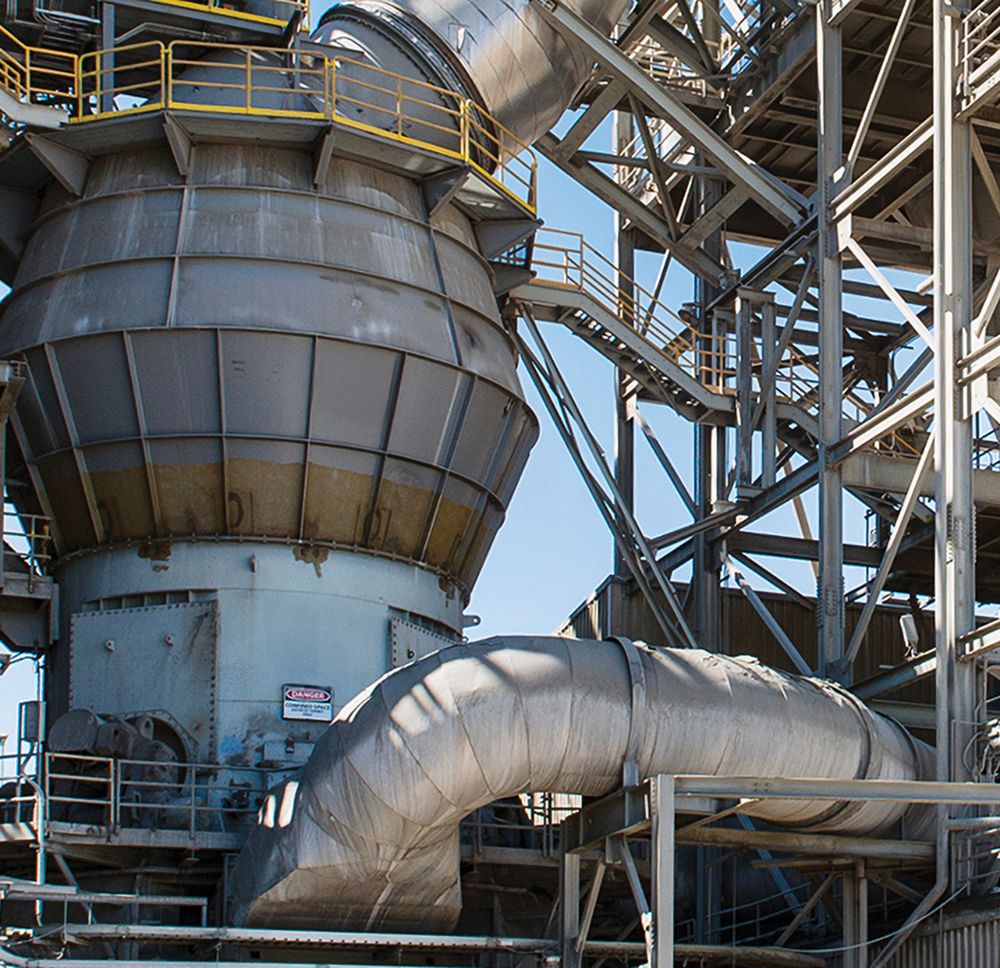
Third-generation separators for ball mills like the O-SEPA® or SEPAX™ utilise more hard-wearing materials, improving seal performance and separating more efficiently. These types of upgrades require just a 2 – 3-week shutdown, as much of the work can be done while the mill remains operational and deliver a 5 – 10% reduction in power consumption.
Among third-generation separators for VRMs, options like the ROKS-H separator specifically address overgrinding in Type 1L cement, delivering energy savings of about 2 – 3% while improving product quality. Even an upgrade from an early 3rd generation separator, like a ROKS, to one of the latest separator designs, like a ROKS-H, can reduce power consumption and improve cement quality in a grinding circuit.
Reducing energy use in feeding and dosing
Even small inefficiencies in feeding and dosing can result in wasted energy and increased operational costs. If your dosing system struggles to maintain consistent feed rates, the inevitable result is instability in pyroprocessing and impacting power consumption.
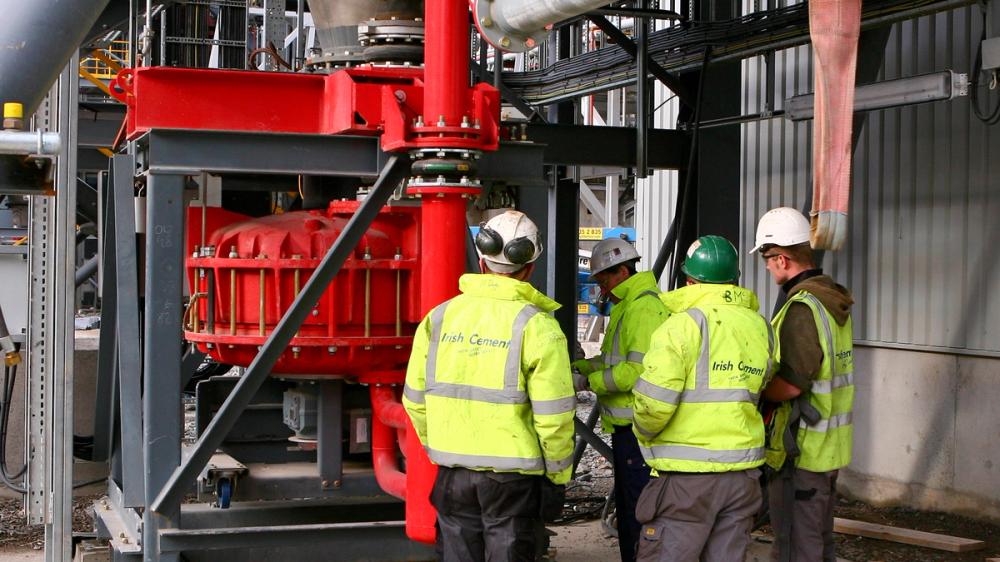
“We’re continually exploring ways to reduce energy consumption in feeding and dosing applications,” says Peter Norek, Global Product Manager-Feeding and Dosing Technologies. “We’ve introduced digital features like Pfister® Smart Aeration, which reduces compressed air usage by up to 90%, patented FEEDFlex™ technology, which enables much lower fossil fuel dosing, and the FDC controller upgrade, which includes a new motor, enhancing efficiency and reducing electricity consumption. These are all simple upgrades with a positive environmental impact.”
Improving preheater efficiency and heat retention
Preheaters play a critical role in cement plant energy efficiency, but outdated cyclone designs and corroded components can lead to excessive heat loss and higher fuel consumption. Plants that optimise preheater separation efficiency can reduce fuel use by up to 5 – 10 kcal/kg clinker while improving downstream performance.
One area where upgrades can make a difference is in the central pipe elements. By switching to an advanced suspension design, plants can improve separation efficiency and extend wear life — offering both energy savings and operational benefits.
“The cast central pipe is installed in the preheater cyclones to improve separation and thermal efficiency,” explains Muthukumar Muthu, Senior Product Specialist, “Our patented design for the suspension of the cast pipe reduces corrosion (extending pipe life), while also making it easier to carry out maintenance work. Installation of one cast pipe in the lower cyclone stages can save customers 5 – 10 kcal/kg clinker, reducing power consumption in the ID fan drive by 4 – 8% - a significant energy saving. Customers can choose whether to claim these benefits in cost savings or convert them to a 1 – 2% increase in production. Either way, the cast pipe provides a quick ROI.”
The improvements to the cast central pipe elements reduce the stress across the element, and make it simpler to manufacture, which results in a more consistent quality, more durable product. This upgrade can be implemented during the annual maintenance shutdown with no disruption to operations.
Maximising efficiency in combustion
False air leaks and inefficient fuel combustion are two of the biggest sources of energy waste in cement kilns. Uncontrolled air ingress forces plants to burn more fuel to maintain operating temperatures, while the inefficient combustion of alternative fuels can create a volatile environment that reduces both efficiency and clinker quality. To address these issues, plants can implement sealing upgrades that prevent air leaks and burner modifications that optimise fuel-air mixing, ensuring more complete combustion and greater flexibility in alternative fuel use.
“We’ve introduced the new Spring Tensioned Graphite Seals to reduce false air entry and increase thermal efficiency – effectively lowering fuel consumption without affecting clinker quality,” says Karthikeyan Arumugam, Senior Product Specialist.
In addition, advanced burner designs such as a JETFLEX® partial upgrade allow plants to retain the existing kiln burner pipe while improving fuel-air mixing, increasing alternative fuel utilisation and efficiency. This burner enables cement producers to use pulverised coal or petcoke, anthracite, oil, natural gas – or any mixture of these – as well as alternative fuels (such as plastic and wood chips, sewage sludge) with no difference in performance and minimal volatility in the kiln to support reliable and consistent production of high-quality clinker with low NOx emissions.
Cooling efficiency as easy as ABC inlet
An inefficient or older generation cooler inlet leads to higher fuel consumption. Alternative fuels and petcoke produce dusty, sticky clinker that builds up easily, creating ‘snowmen’ in the cooler that disrupt the system, leading to inefficiencies and even unplanned shutdowns.
“The ABC Inlet upgrade continues to be one of our most successful cooler inlet upgrades because it resolves issues as a result alternative fuels usage and enables better heat recovery back to system,” explains Rene Hede, Cooler Product Specialist. “The ABC Inlet prevents snowmen formation with a patented in-grate design that pushes compressed air up through the grates, blasting agglomerations.”
In addition, the ABC Inlet’s rapid quenching process enables faster clinker cooling while maximising heat recovery to the pyro line, resulting in heat consumption savings of 10–30 kcal/kg of clinker. This also enhances clinker quality, providing greater flexibility in cement product formulation and allowing for clinker factor reductions that further improve grinding energy efficiency.
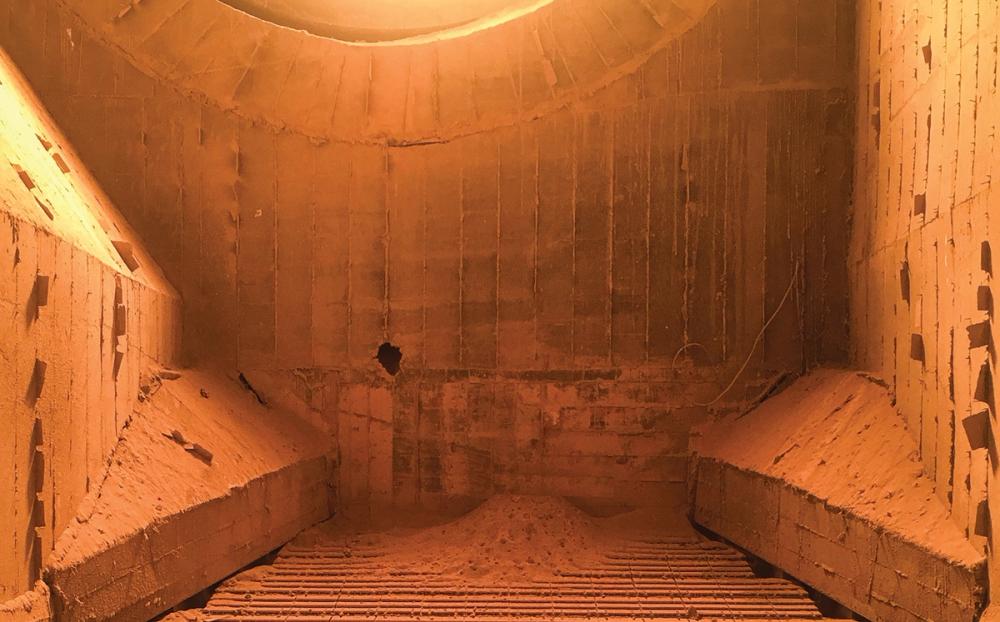
Improving energy efficiency in material transport
Pneumatic conveying offers a cleaner and more contained alternative to mechanical conveying. However, pneumatic systems can also be energy-intensive, with inefficiencies arising from air leakage, pressure losses, and outdated equipment designs. Optimising these systems can significantly reduce energy consumption and operating costs.
“One major challenge is maintaining efficient air-to-material ratios, as excessive air use leads to unnecessary power consumption,” explains Emilio Vreca, Manager of PT Product Engineering“Leaks in piping and inefficient compressors further compound energy losses. To address these issues, upgrading to the latest pneumatic conveying solutions can yield substantial improvements.”
The latest pump design—the Fuller-Kinyon® (FK) ‘N’ Pump—provides power savings of up to 15% thanks to an improved seal, while an extended barrel and screw design have improved volumetric efficiency by more than 15%. Similarly, the latest generation Ful-Vane™ Air Compressor has been engineered for increased energy efficiency, with an improved inlet area for capturing larger air flows and compatibility with variable frequency drives.
Optimising energy efficiency in packing and dispatch
Even minor inefficiencies in bagging and palletising can lead to higher maintenance demands, increased material waste, and unnecessary energy use. Reducing these inefficiencies is yet another lever to improve overall plant performance and sustainability.
Upgrading rotary packers enhances weighing accuracy, reduces spout-to-spout variations, and lowers reject rates, improving both product consistency and energy efficiency. Similarly, replacing pneumatic drive systems in palletisers with electric alternatives eliminates compressed air dependency, leading to more precise bag handling and reduced energy demand. These targeted upgrades help streamline operations while minimising environmental impact.
A key development in dust control is the FILLPro™ Dust Reduction Kit for GIROMAT® EVO. “By refining material flow and fluidisation, FILLPro reduces dust emissions at the
source, improving bagging efficiency and plant cleanliness,” explains Gabriele Rapizza, Proposal Engineer. “This reduces material loss, prevents blockages, and cuts down on maintenance, helping plants achieve a more stable and energy-efficient packing operation.”
How services contribute to increased energy efficiency
In the past, many viewed the role of the supplier as a “sell-and-move-on” model. Things have certainly changed. As cement producers face challenging markets, heightened competition, and increasingly ambitious decarbonization targets there is little room to tolerate inefficiencies within the plant.The paradigm has shifted such that the value of expert services is as essential as the initial equipment supplied. Furthermore, as digital solutions progress at speed, a fluid, long-term partnership gives cement plants the best platform to take advantage of the latest tools.
Whether it’s an audit to identify why energy efficiency has decreased from one year to the next, or even an optimisation package preparing your plant for carbon capture solutions – we are believers in the principle that there is always more we can do to improve efficiency. For example, our Online Condition Monitoring Services (OCMS) provide continuous monitoring of critical equipment such as the kiln, mills, cooler and fans, aggregating data and utilising advanced algorithms to identify potential trouble spots. As the OEM and an experienced full solutions provider, we can support these services with expert advice, not only alerting you to a problem but also providing recommendations as to how to remedy it or attending site to support you in person.
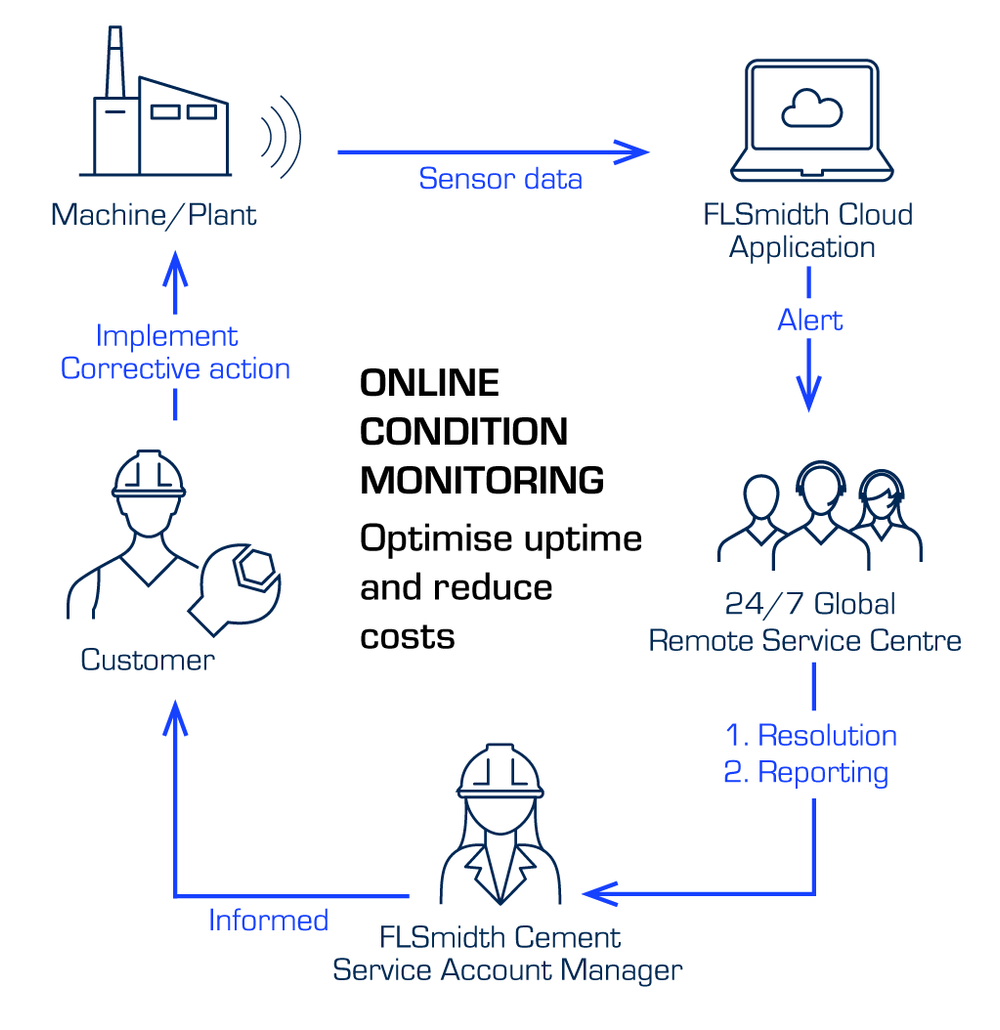
Small upgrades, big impact
Energy efficiency is a critical factor, influencing both operational costs and sustainability goals. While large-scale innovations such as carbon capture will play an essential role in long-term decarbonisation (and steal the headlines), incremental mechanical upgrades offer an immediate pathway to lower energy consumption with minimal disruption.
By optimising key process areas — grinding, dosing, combustion, cooling, and material transport — you can achieve measurable energy savings while improving performance and flexibility. These solutions provide a strong return on investment and pave the way for a more sustainable cement industry.
This article was originally published in International Cement Review's May 2025 issue.