Save energy or increase production
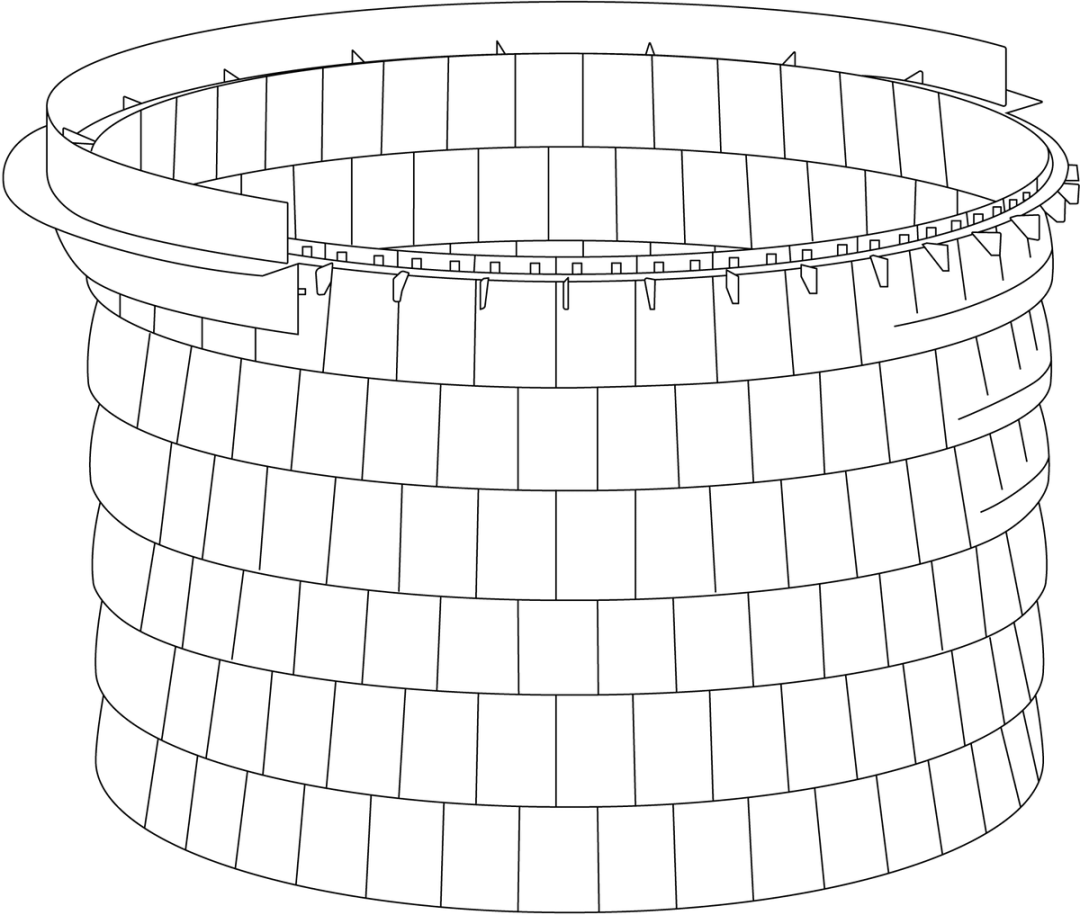
What we offer
Improved separation and thermal efficiency
Installation of a central pipe in the preheater cyclones is essential for the overall performance of the preheater. Delivering both improved separation and thermal efficiency, the FLSmidth central pipe saves fuel and decreases power consumed on the ID fan drive, as the preheater gas temperature is reduced.
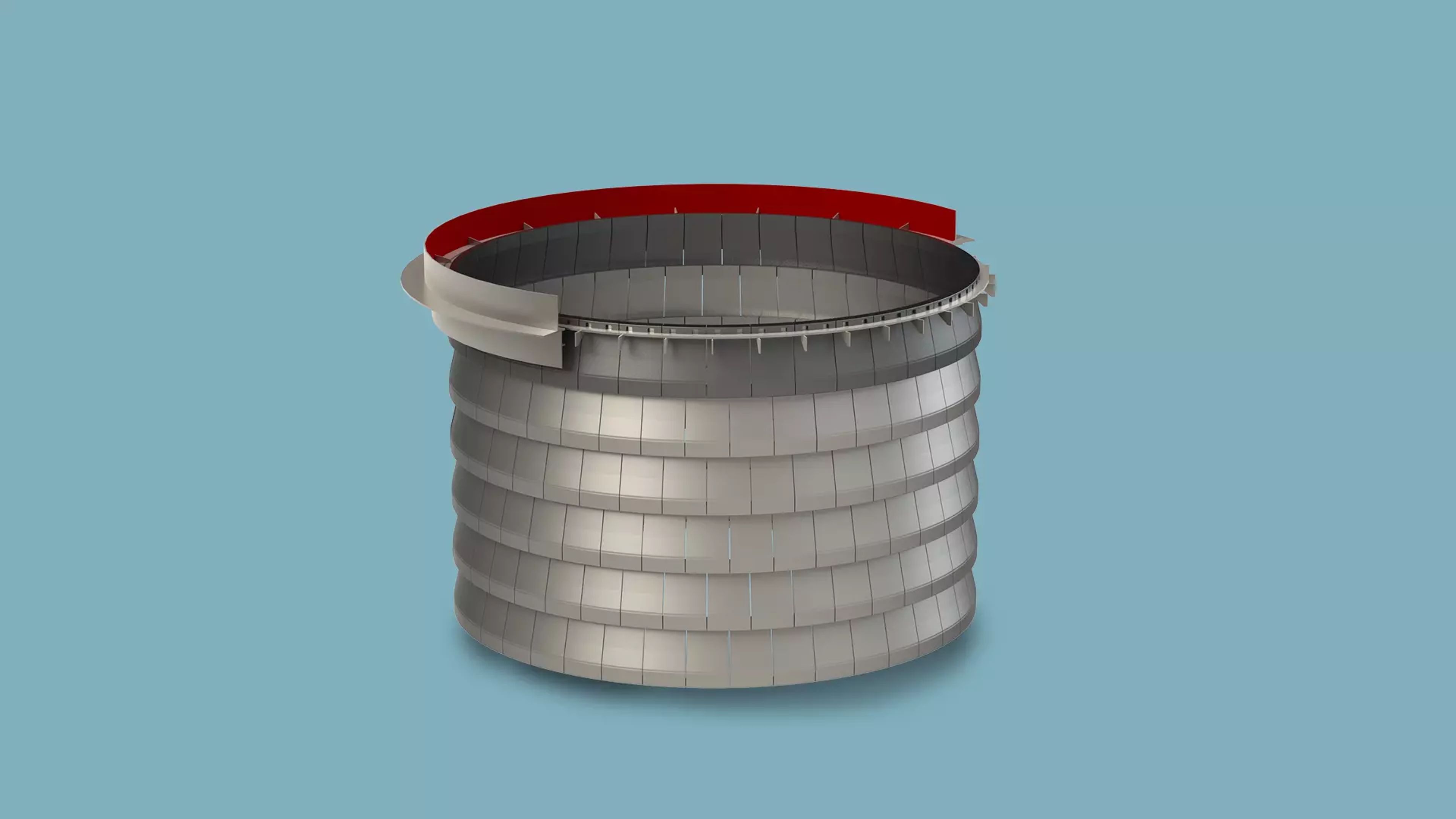
Fast, easy installation
The cast central pipe’s modular design fits into any size of cyclone design – both new and existing cyclones, regardless of manufacture.
The cast central pipe is very easy to install with only a short downtime required. The simple design and limited number of different replacement parts makes it possible for FLSmidth to maintain adequate stock to ensure fast delivery worldwide.
By installing one cast central pipe in the lower cyclone stages, the typical fuel savings are between 5-10 kcal/kg clinker and the power consumption savings on the ID fan drive are between 4-8%. Whether reductions in fuel and power consumption are converted into savings or increased production of typically 1-2%, the central pipe provides a fast return on investment.
Cast central pipe design update
As part of our drive to continually reduce the total cost of ownership of all our equipment and components, we have made a change to our cast central pipe segments. The new design gives you improved performance and longer life.
The hook length has been reduced by 5 mm, which better distributes the stress across the segment and prevents the premature bending of the hook, thus reducing the risk of failure.
The thickness of the segment has been standardized to simplify casting. This reduces the potential for quality issues during manufacture, ensuring you get a sound product you can depend on.
These changes will extend the life of the segment - a better product that won’t cost you more, but could save you money on repairs. In fact, we are able to offer competitive wear guarantees for both retrofits and new projects.
Segment range extended
In addition to the performance improvements, we have also added a new segment length to the range. The standard segment length is still 500 mm, but we now also offer an alternate length of 770mm. For many customers, this will reduce the overall number of rows of segment and weight needed to achieve the same target pipe length, offering better value for money. This also provides more flexibility for retrofits with matching up the length of the new segment to the length of the existing segment being replaced.
Segment range extended
In addition to the performance improvements, we have also added a new segment length to the range. The standard segment length is still 500 mm, but we now also offer an alternate length of 770mm. For many customers, this will reduce the overall number of rows of segment and weight needed to achieve the same target pipe length, offering better value for money. This also provides more flexibility for retrofits with matching up the length of the new segment to the length of the existing segment being replaced.
The redesign does not affect the suspension ring system, which is unchanged and works the same with the new segments.
Segments will be manufactured of 5840 material as standard, though our 5850 and new 5860 materials are available for high corrosion cases if needed.
15 mm thickness is standard; 20 – 25 mm thickness will be used for the very largest cyclones or for high corrosion cases.