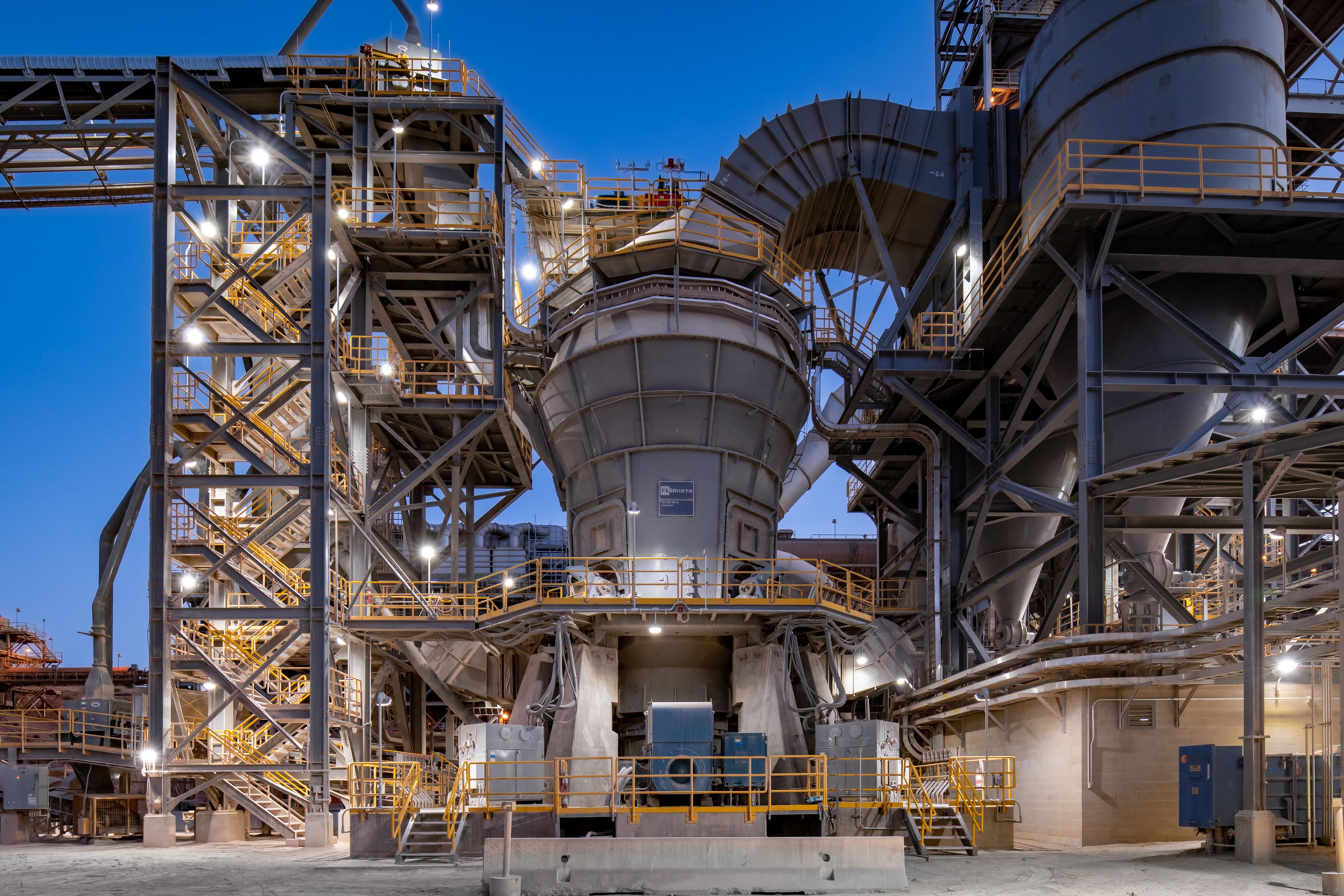
With years of experience in the cement and over 3000 mills sold worldwide, FLSmidth Cement continues to develop its range of efficient milling and grinding solutions. This experience and know-how, as well as close collaboration with our customers, means we can deliver best-in-class technology.
We know that you strive to increase production while saving on CAPEX, operation and maintenance costs. Further, consideration for the environment is a priority for production industries, making energy-efficient designs highly sought after. So, these are our priorities when designing milling and grinding equipment to meet your needs.
With the knowledge and experience gained throughout the years, we ensure that you have the best milling or grinding solution possible.
Our Hydraulic Roller Press is suitable for water-scarce locations as it does not require water for deagglomeration of feed material in the roller press. It is also adaptable to three different types of grinding setups: pre-grinding, semi-finish grinding and finish grinding. The OK mill can skilfully grind raw or cement feed material and offers parts commonality, simplifying spare parts inventory and facilitating easy switching of parts between vertical roller mills. Our ATOX® coal mill has large rollers with great grinding capability of all types of coal, tolerating moisture levels up to 20 percent.