One-step processing of wet, sticky raw materials with our dryer crusher
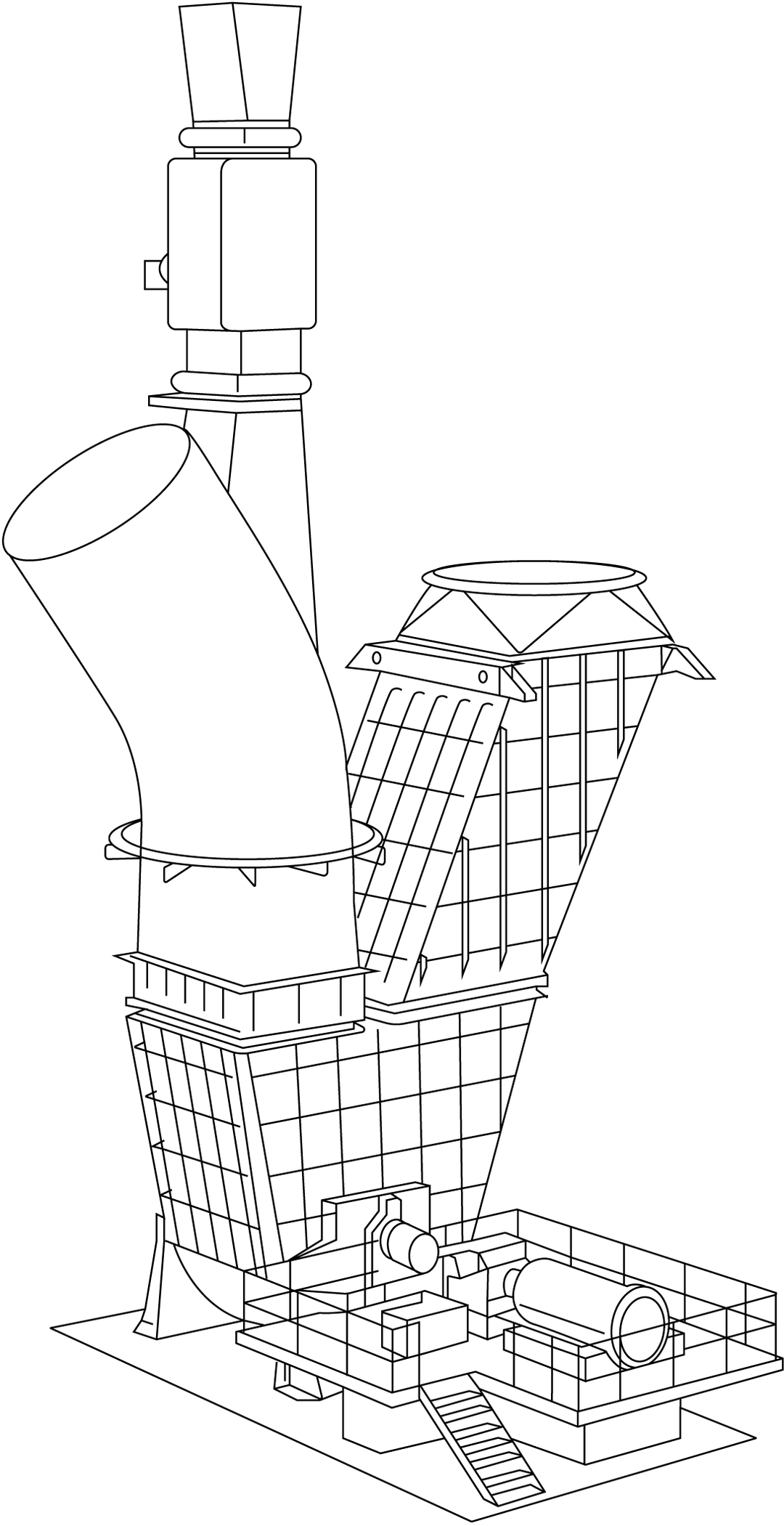
What we offer
One machine, two jobs: the FLSmidth dryer crusher
Ideal for sticky, low-abrasive materials with high moisture contents, such as chalk, clay, marl, and slurry filter cake, our dryer crushers deliver consistent raw material preparation at the very start of your production process. They can also be used to dry slurry. Dependable raw material preparation The drying process re-uses hot gases from available pyroprocess equipment in an energy efficient process that delivers final product moisture content of about 1%. This drying process is combined with our proven impact hammer crusher that efficiently crushes feed of up to 100-150mm. The result is a machine that you can depend on, day in, day out, for your raw material preparation needs. Crushing that meets your individual needs Our state-of-the-art raw materials testing centre at FLSmidth Dania, Denmark, and our laboratory in Chennai, India, support you in making the most appropriate crushing solution for your application. These facilities are some of the world’s most advanced for raw material analysis and allow us to measure various parameters, such as hardness, abrasiveness, and stickiness. Understanding these factors allows us to optimise the process to your specific application requirements..
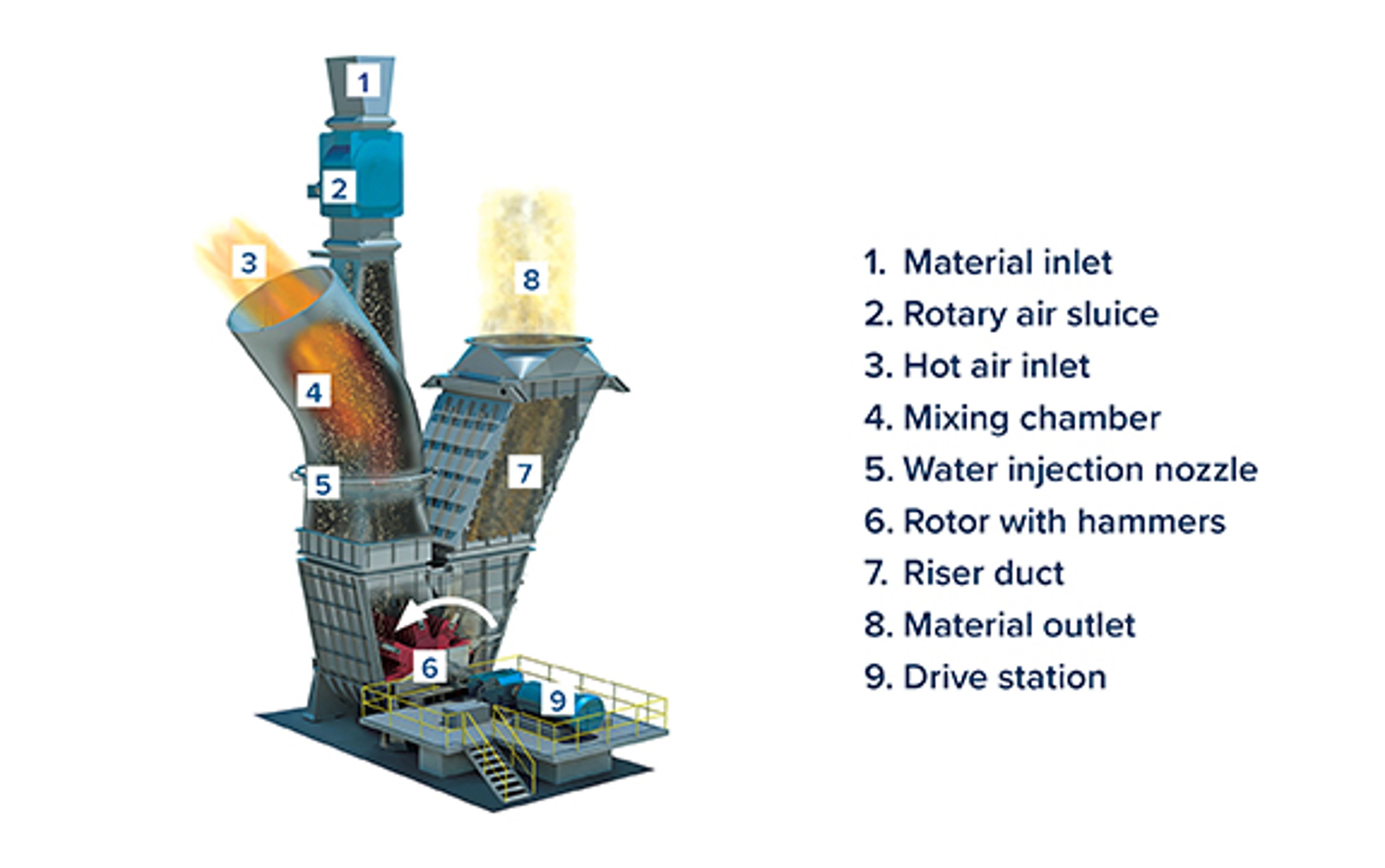
Energy efficient. Low maintenance. A crusher you can depend on.
Two jobs, one machine
Doing more with less – without sacrificing quality, reliability, or efficiency – is a central tenet of sustainability. It’s one we place particular emphasis on here at FLSmidth. Our dryer crusher is a case in point. Designed for soft and sticky raw materials with moisture contents up to 40%, these versatile machines combine drying and crushing processes into one efficient operation.
A highly energy-efficient process
Our dryer crushers are designed to utilize hot gases from your pyroprocess equipment, such as cement preheaters or clay calciners, for maximum energy efficiency.
Reliable with low maintenance
Your dryer crusher will often be the first step in the production process. You depend on it to deliver a consistent and high-quality feed to your downstream process, day in, day out. Any unnecessary or extended shutdowns will therefore dent productivity and hit the bottom line. It’s why we’ve designed our dryer crusher to keep running reliably, with few maintenance interventions required. So, while you may have headaches in your process, our dryer crusher won’t be one of them.
What we offer
Have we mentioned it both crushes and dries?
Hot gases are supplied from your pyroprocess equipment, such as cement preheaters or clay calciners, to provide a continuous flow of hot air with an inlet temperature of 400°C to 800°C. This air sweeps through the dryer crusher, pre-drying the feed material as it enters the mixing chamber. Drying continues as feed material passes through the impact crusher chamber to deliver a product moisture content of about 1%. In the crushing chamber, impact hammers efficiently reduce feed materials through impact with the hammers, collision between feed particles, and impact with the lined housing.

Minimising unnecessary recirculation of material
Past the crushing chamber, the system is designed to reduce unnecessary recirculation of material for optimum efficiency and productivity. Coarser material first drops out of the air stream in the riser duct and returns straight to the crushing zone. A high-efficiency dynamic separator then accurately removes any remaining oversized material, which is returned to the dryer crusher inlet. Finished product proceeds to the cyclones and filter.
Designed for minimal maintenance
Maintenance is reduced to a minimum thanks to a number of key design features. Raw materials are fed into the dryer crusher through a self-cleaning rotary air sluice. Slurry is injected through nozzles just above the rotor; a water injection nozzles is also provided in case there is a disturbance in the raw material flow.