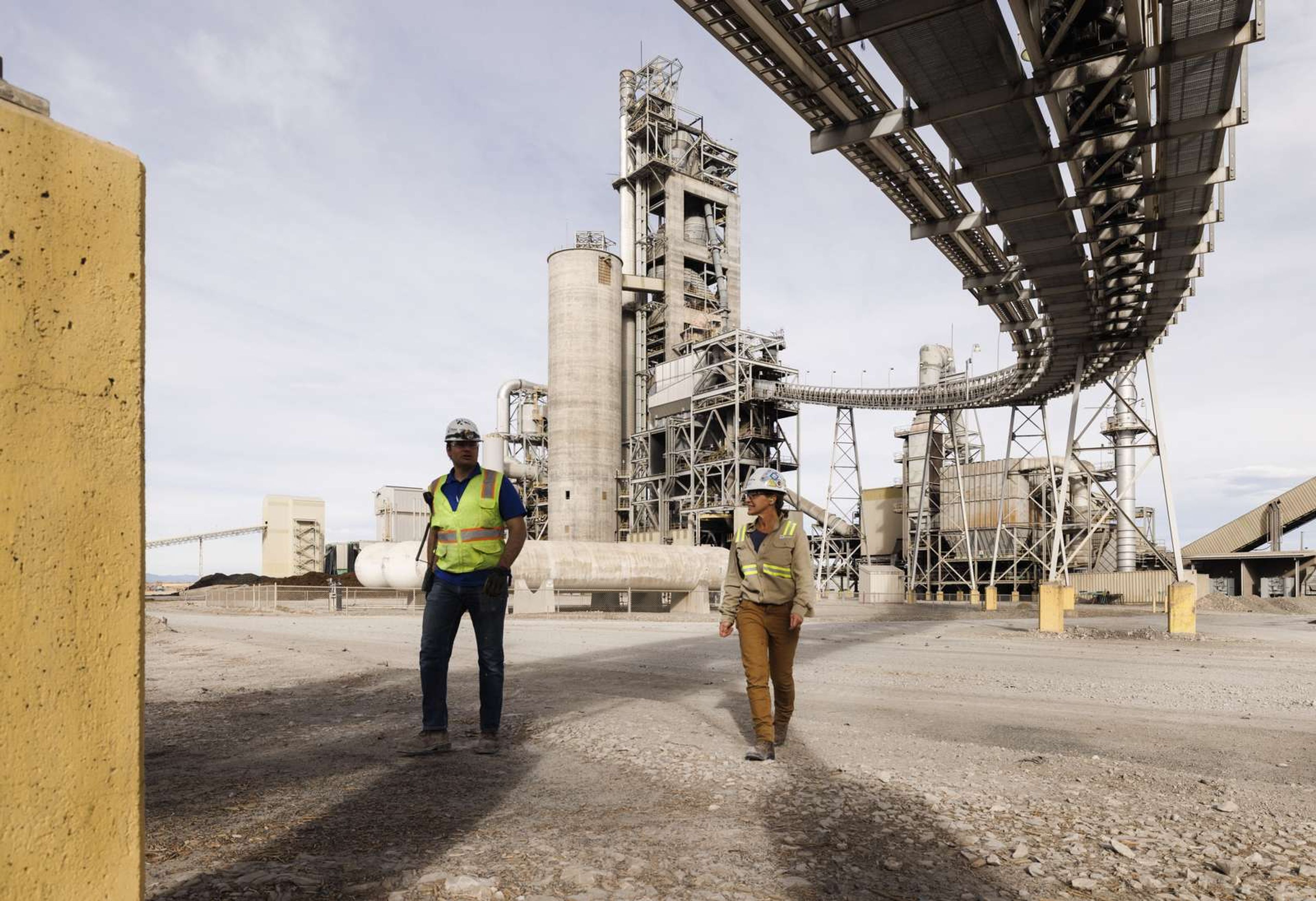
Plant managers rely on FLSmidth Cement’s PlantLine™ Service Agreements to help improve productivity and reliability
What we offer
Complete Life-Cycle Support - 24/7/365
PlantLine Service Agreements provide cement plant managers with comprehensive automation support through our globally-distributed expert network. Available 24/7/365, our specialists deliver high-priority responses to urgent technical issues while also performing preventative maintenance, system optimization, and specialized training. With approximately 4,000 troubleshooting sessions conducted monthly across hundreds of global installations, our team applies unparalleled product knowledge to your automation systems—ensuring maximum operational continuity and performance optimization throughout your equipment lifecycle.
Our Go2 Support site has changed.
For cement-specific service and support, please visit our new site: go2.cement1882.com
Is Your Automation System's Reliability Creating a Hidden Challenge?
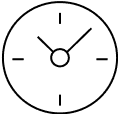
System Downtime - Technical issues create costly production losses
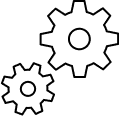
Expertise Gaps - Plant teams lack vital troubleshooting experience
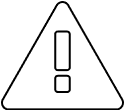
Security Risk - Aging infrastructure enables potential cyber breaches
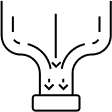
Efficiency Deficit - Outdated systems prevent optimal plant performance
Let's talk about what's in it for you
Let's talk about real benefits that matter to your bottom line when choosing a Plantline Service Agreement. Plantline Service Agreement covers FLSmidth’s automation equipment and software. The name refers to the support line that connects the plant with FLSmidth. Through a range of flexible service offerings, it ensures your automation equipment and software remain protected and performing well. We ensure that your asset delivers today, tomorrow, and throughout its lifetime, giving you the time to focus on other important matters.
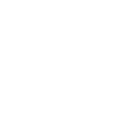
Improves system performance
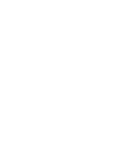
Reduces downtime-related costs
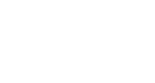
Delivers higher run factor
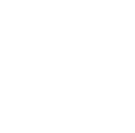
Extends system lifetime
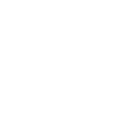
Improves productivity and quality
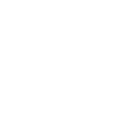
Fixes maintenance costs
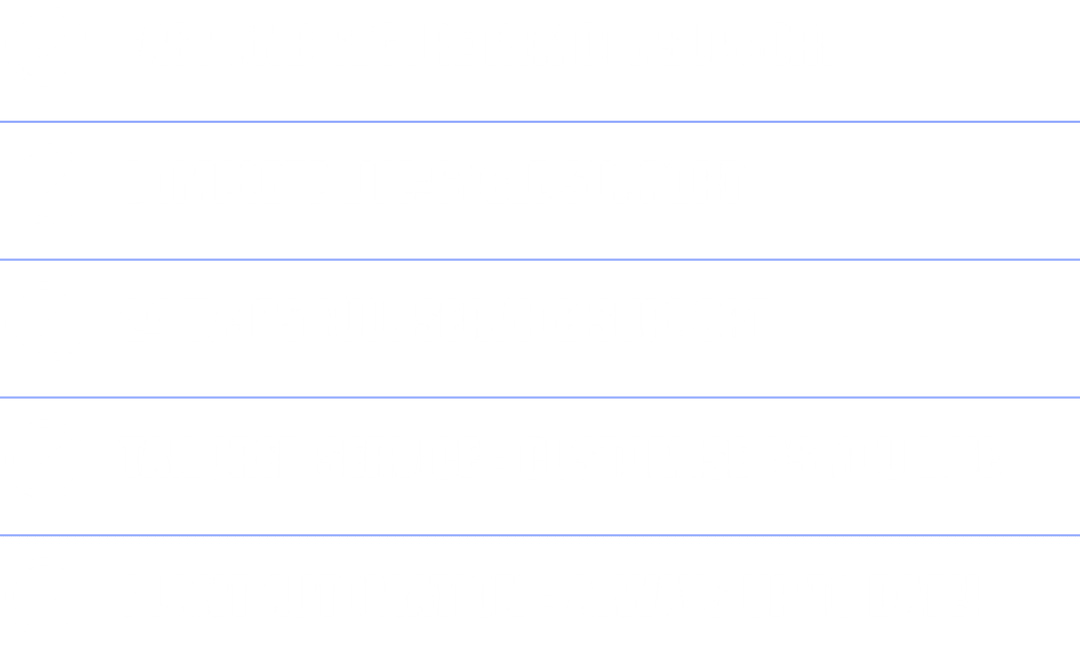
Peace of mind for your plant
With over 300 plant managers worldwide relying on our services, we connect your facility to automation specialists who developed, manufactured, and commissioned your systems—delivering immediate troubleshooting expertise 24/7/365. The result: improved system performance, reduced downtime costs, extended equipment lifespan, and enhanced productivity that directly impacts your bottom line.
KCP Limited
Building a PlantLine Service Agreement - A fast and secure remote support from our team of experts
All PlantLine Service Agreements start with the mandatory Essential package of services. This lays the foundation for more advanced offerings via four optional service packages: Proactive, Lifecycle, Cyber Service, and Remote Technologies. Each of these packages offers multiple pick ‘n’ mix services, so you can decide just how much support you need and choose which combination of services to include. You can also adjust the level of support from year to year as your needs evolve.


Proactive Service Package
The new guillotine shape optimizes the flow’s kinetic energy to: ・Preventative maintenance visits (Onsote / Remote Sessions): Our preventive maintenance visits aim to optimise operation of your FLSmidth automation systems. We can deliver visits onsite or remotely for a faster and more cost-effective response. The exact quantity of visits and other particulars are established with each contract, and administration is simplified through one annual billing. ・Performance monitoring and remote optimisation: Our performance monitoring and remote optimisation service aims to empower your plant personnel to get the most from our ECS/ProcessExpert® (ECS) advanced process control system and /or QCX/BlendExpert™ (QCX) advanced quality control system. Benefits include regular performance monitoring, close cooperation between your plant specialists and our experts, professional tuning of your expert systems, and advice on relevant upgrades and migration.

Lifecycle Services
Access to the latest FLSmidth Cement software products for maximum efficiency, reliability, and security. Software advances at speed. Waiting years to update your software could therefore not only risk your security; it could also mean you’re missing out on opportunities to improve process efficiency that could save you millions of dollars. Our PlantLine Lifecycle services make sure that doesn’t happen with both software and hardware maintenance service options. ・Software maintenance service: Installation of the most recent software release. Every time we release a new version of an ECS or QCX product, we let you know about it and give you access as it’s released, so you can benefit from the latest features for enhanced precision and productivity. ・Hardware maintenance service: Similar to software, your hardware also needs maintenance. By planning timely repairs and having expert assistance on hand, you can increase your equipment’s life expectancy and enjoy predicable maintenance costs. Whether it’s spare parts or wear parts, we can recommend the needed items.

Cybersecurity
Cyberattacks are one of the biggest threats facing manufacturers. With the potential to take you offline for hours or even days, the risk of virus attacks is significant and should not be ignored. The PlantLine Cybersecurity package of services includes our managed whitelisting service and system hardening service. ・Managed whitelisting service ・System hardening

Remote Technologies
The services on offer within a PlantLine Service Agreement open up a world of possibility. Now it’s up to you to discover what you can do with them. From a mobile app to enabling remote access to your control network across your organisation, we can use PlantLine as the foundation for a host of additional solutions, enabling you to increase productivity and gain peace of mind with a flexible approach that’s tailored to your plant. ・ PlantLine mobile app The mobile app keeps you updated on equipment, process, and performance around the clock, even when you’re far away from the plant. ・ Go2FLS The world is changing, and we’re ready for it. Our remote services are well-established, but if you want to empower your team to access control room data remotely, we can help. Our Go2FLS technology enables remote access to the plant’s control network for internal plant support and maintenance. Your team can tap into real-time process mimics, trends, diagnostic faceplates, and all alarms/events on the plant’s control system, enabling them to be part of troubleshooting efforts, engineering, software maintenance and process optimisation wherever they are.

Going beyond Plantline Essential
What comes after PlantLine Essential? Well, that’s up to you. Your PlantLine Service Agreement is designed for you, by you, using our four optional PlantLine service packages: Proactive, Lifecycle, Cyber Service, and Remote Technologies. ・ The choice is yours.
CRH Group
Key benefits
Improves System Performance
Our automation experts / specialists proactively monitor and optimize your systems for peak efficiency through advanced data analytics and preventative maintenance.
Delivers Higher Run Factor
Our PlantLine™ Service Agreements maximize automation system uptime through our 24/7/365 global support network of experts. Enabling a higher run factor for your plant.
Extends System Lifetime
Strategic lifecycle management enhances your automation investment value through comprehensive software and hardware maintenance for your plant.
Improves Productivity and Quality
The integration of advanced process control systems with expert support creates measurable productivity and quality improvements for your plant. Reliable and secure.
Protective coverage wrapped in expertise
A PlantLine™ Service Agreement delivers the personalized support essential for optimizing your cement plant's productivity. Whether you're confronting technical challenges, addressing cybersecurity vulnerabilities, or seeking efficiency improvements through software modernization, our flexible service framework provides comprehensive solutions designed to maximize productivity while ensuring operational peace of mind. What truly differentiates PlantLine™ is the expertise behind our service delivery. Our global team of automation specialists—the same professionals who developed, manufactured, and commissioned your systems—conducts over 4,000 troubleshooting sessions monthly for hundreds of customers worldwide. This unparalleled experience enables us to anticipate potential issues before they impact production, allowing your team to focus on core business priorities while we ensure your automation systems deliver consistent, reliable performance 24/7/365.
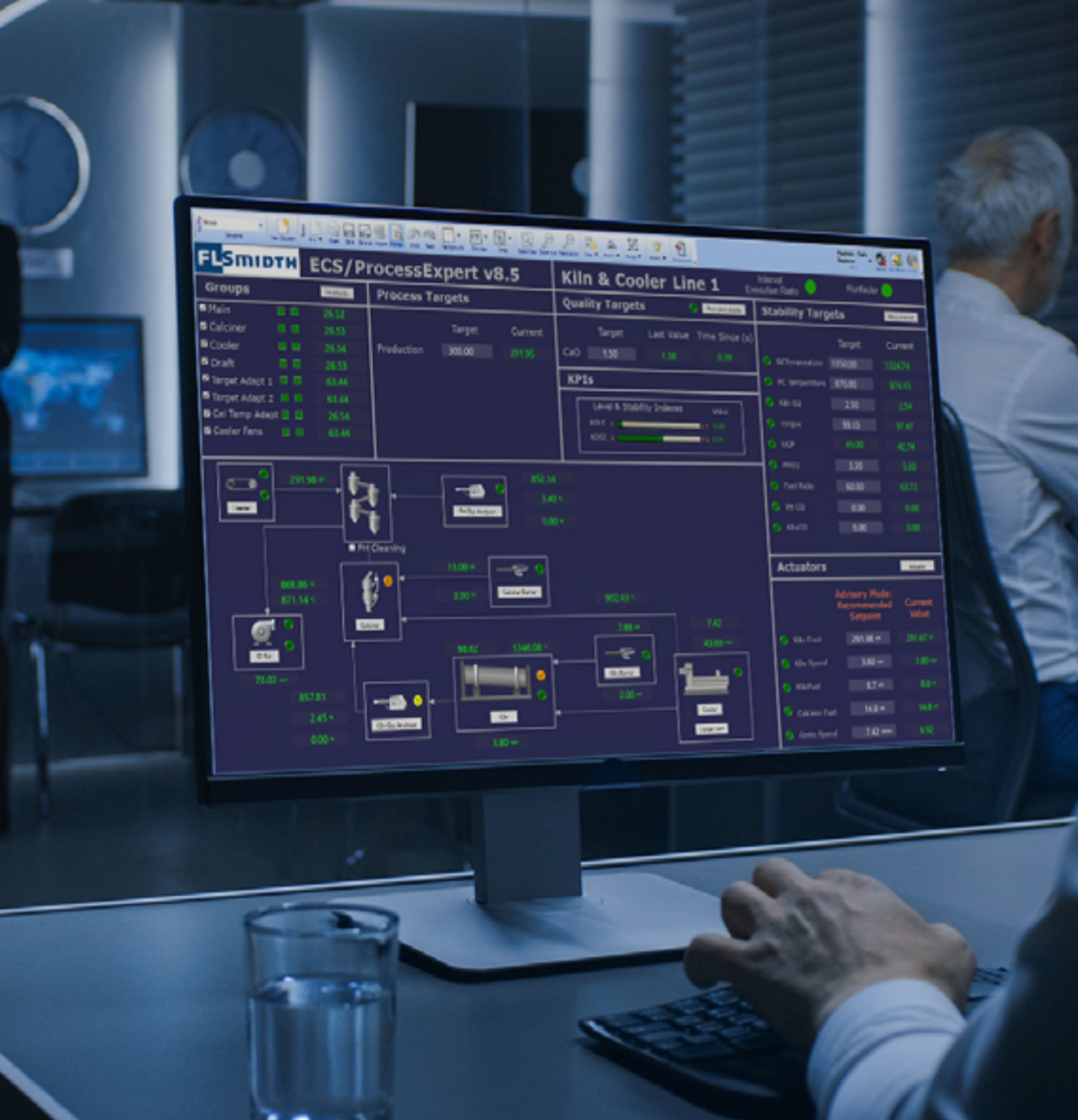
Related Offerings
Services (3)
Plantline Service Agreement - latest news
News and stories about our company, business and offerings related to the Plantline Service Agreement
Recent posts