Automated samplers delivering premium quality control to your cement plant
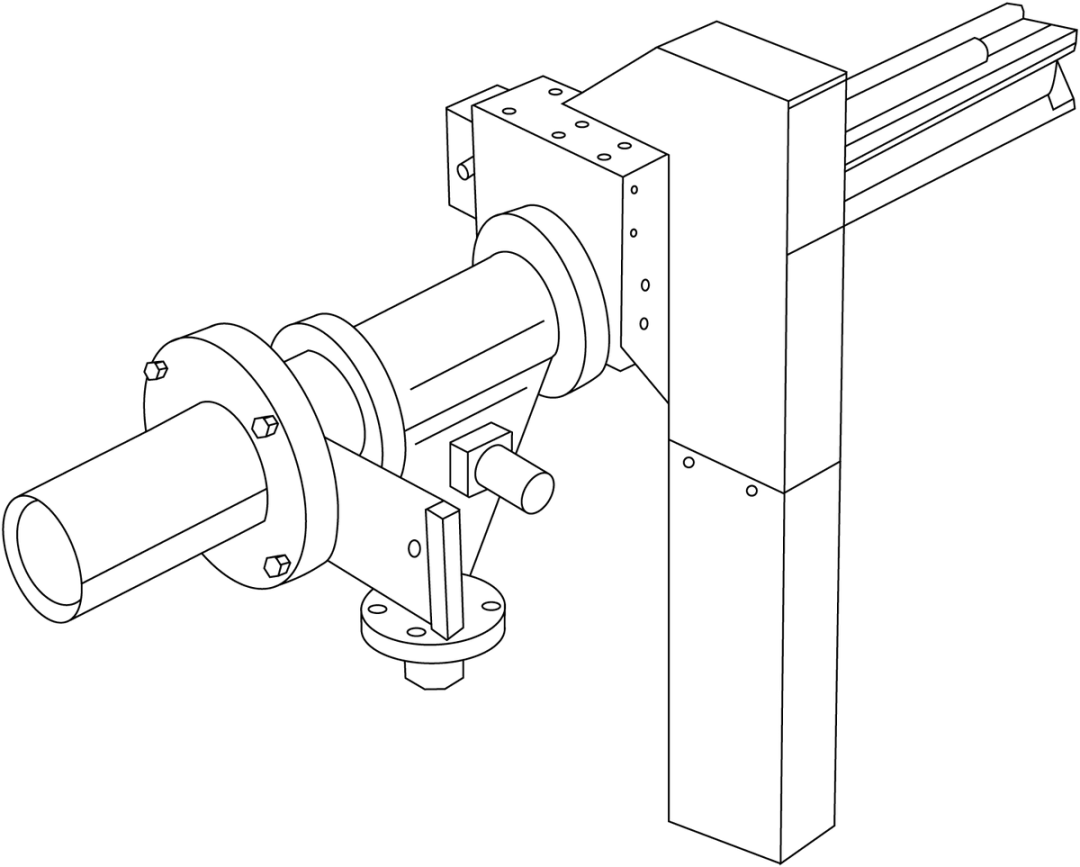
What we offer
Take control of your plant quality – all day, every day
You can trust our pragmatic approach to sampler design. We deliver well-performing and proven sampling solutions that support the production process throughout the cement plant – this includes monitoring chemical processes and product quality, process optimisation, and checking your finished cement ready for despatch.
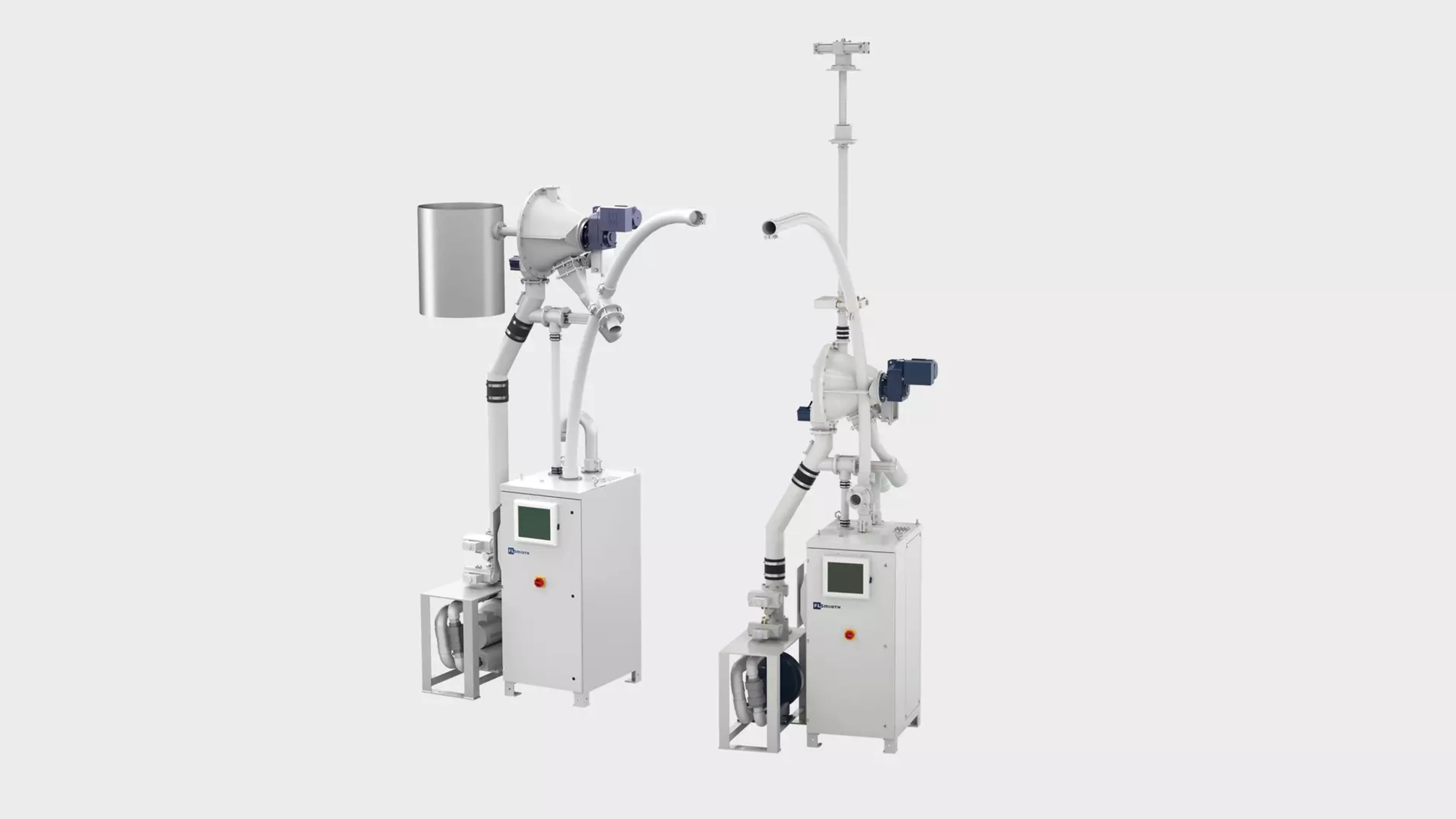
Efficiency
We understand the rules of correct sampling practices, as well as applicable industry standards. We combine smart sampler design with deep knowledge of relevant processes and industry-specific experience. What does this mean for you? Practical, efficient and cost-effective sampling solutions.
Fit-for-purpose samplers
We also understand the challenges you face, with sampling being the critical first step in the quality control chain. Without correct sampling, then preparation and analysis are compromised. It has been calculated that 80% of quality errors can be sourced to poor sampling, making the need for fit-for-purpose samplers paramount.
Our range of specialised sampling devices service all the routine sampling programs across the cement plant. They are designed to operate at frequent intervals (every ½, 1, 2, 4, 8 hours or longer) during normal operation. These samplers are permanently installed at designated locations and usually operate fully or semi-automatically.
Manual and automated collection samplers
We distinguish between:
Manual collection samplers – permanently installed, which are automatically operating samplers for routing sampling with manual sample collection.
Automated collection samplers – permanently installed, which are automatically operating samplers for routing sampling with automatic sample collection via our QCX® AutoSampling tube transport system.
In our experience, well over 90% of all sampling requirements can be solved by selecting one of our pre-engineered standard solutions. In the remaining few cases, a customised project solution may be built from a wide range of standard components available.
Don’t disrupt productivity and jeopardise product quality by poor sampling
Cement plants are under pressure to maintain high standards while also minimising costs.
With our samplers, you can achieve high quality cement and optimal performance thanks to the right combination of high standard core equipment technology, process knowledge, and repeatable operating excellence that preserves your plant asset value. Samples are taken consistently, at the right time and at the right place: this results in more frequent samples, sample composites, more representative sampling and faster results.
Minimum sample-to-sample cross-contamination: our fully integrated system with associated QCX®/AutoSampling™ software means high quality dependable results from sampling to transport to laboratory.
Fail-safe sample identification and traceability: with the QCX® system, samples are sent from the process stations to receive/send stations in the laboratory in accordance with individual sample priorities and waitlist status. Sample entities such as sampling location, product type, sampling time etc. are automatically passed on to the next handling stage, whether manual or automatic.
Safety in mind: you can eliminate the slow and hazardous process of manual sampling where operators must access process points around the plant to take grab samples, exposing themselves to heat and moving machinery, often at heights.
Cost-effective: better quality control saves energy and fuel, and leads to better quality product – higher quality equates to higher margins and increased market share for you.
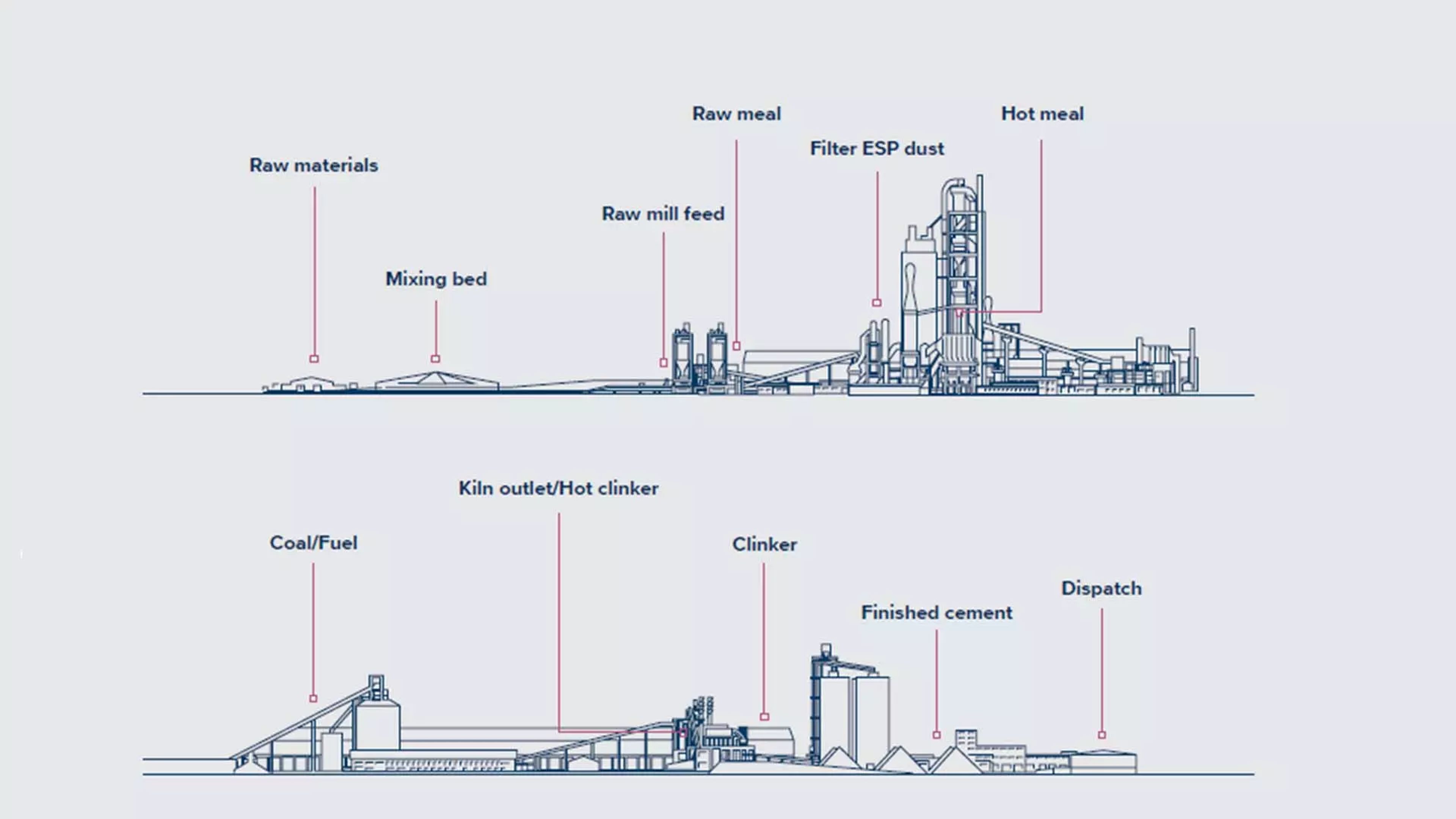
Ensure that your entire cement plant has the best sampling solutions
Many of our sampling solutions are built around two key sampling mechanisms: the PSM chute sampler and the PSA air slide sampler.
Chute samplers
A sampling screw (auger) rotates slowly and continuously extracts powder material from the sample process stream in a vertical or close-to-vertical chute section. A mixing tank – on the same axis as the screw – collects the material for a composite sample. The mixing tank has internal lifters rotating with the auger, which means that the sample material in the tank is constantly well blended. The variable frequency motor can be adjusted, so that the time it takes to fill the mixing tank is within ½ to 2 hours (with ½, 1 or 2 hours as the typical sampling intervals).
Air slide sampler
A sampling tube, with a thin slot, is placed with the slot located opposite the direction of the material flow. With intervals of a few minutes, the tube is rotated 180 degrees, so that the slot is focused on the material flow and a small sample increment is collected and routed to the mixing tank. The tank has rotating internal lifters that ensure the collected samples remain thoroughly mixed. The amount of filling required to equal a ½, 1 or 2 hour sampling frequency is controlled by the time interval of rotating the sampling tube.
Sampling points in the cement plant
The extent of sampling and testing considered necessary at a cement plant varies considerably from one plant to another, depending on the raw materials at hand, production machinery and the quality assurance and control (QA/QC) requirements as defined by plant management. Sampling and/or analysis points are located along the complete cement production process. They include: Raw materials Mixing bed Raw mill feed Raw meal Electrostatic precipitator or filter dust Kiln feed Hot meal Coal meal Kiln outlet Clinker Cement mill Cement silos and cement dispatch. We provide you with reliable solutions to ensure that correct sampling occurs at each and every critical point along the process – reliably, accurately and safely.