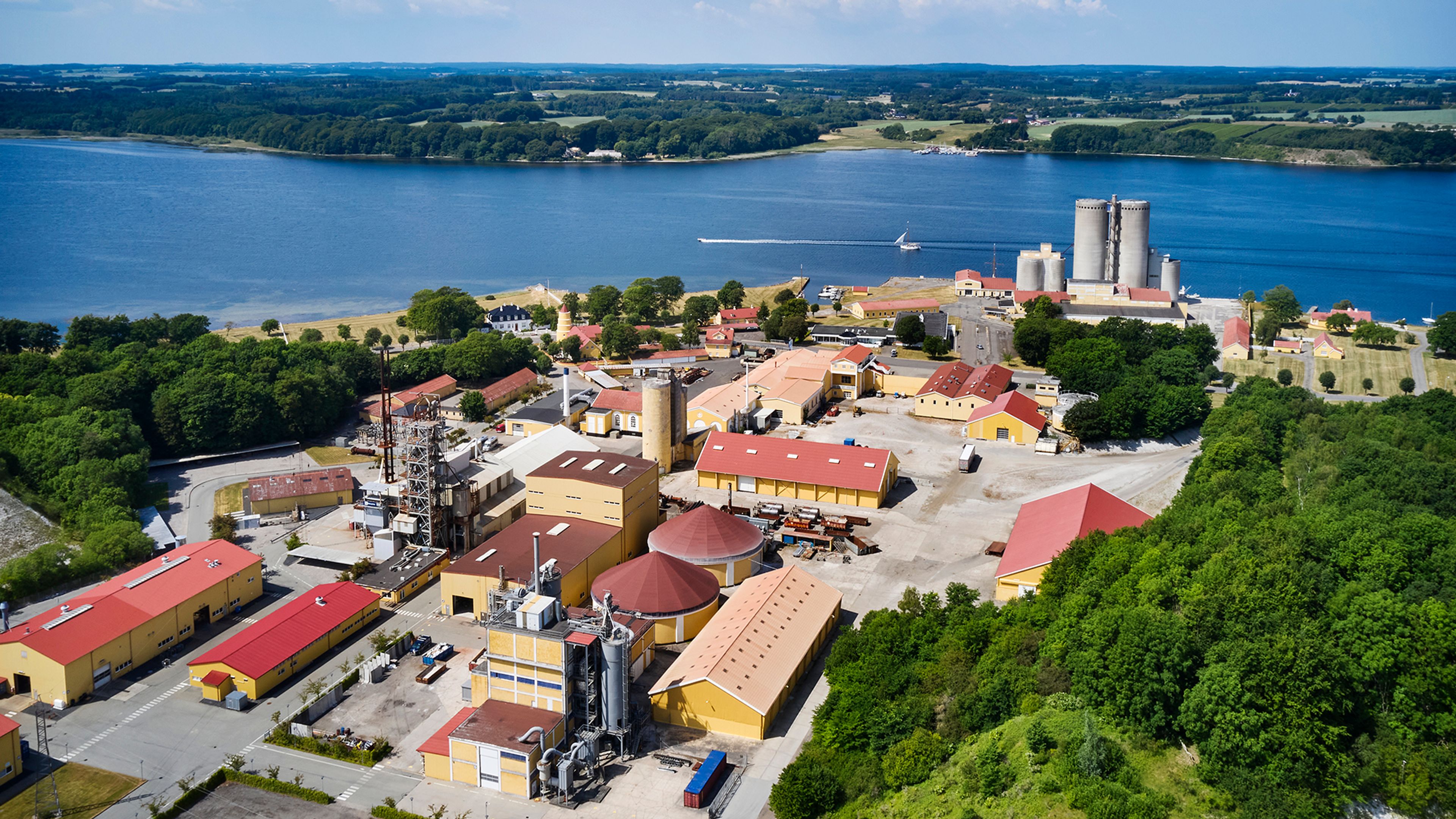
Leverage our expertise and advanced testing facilities
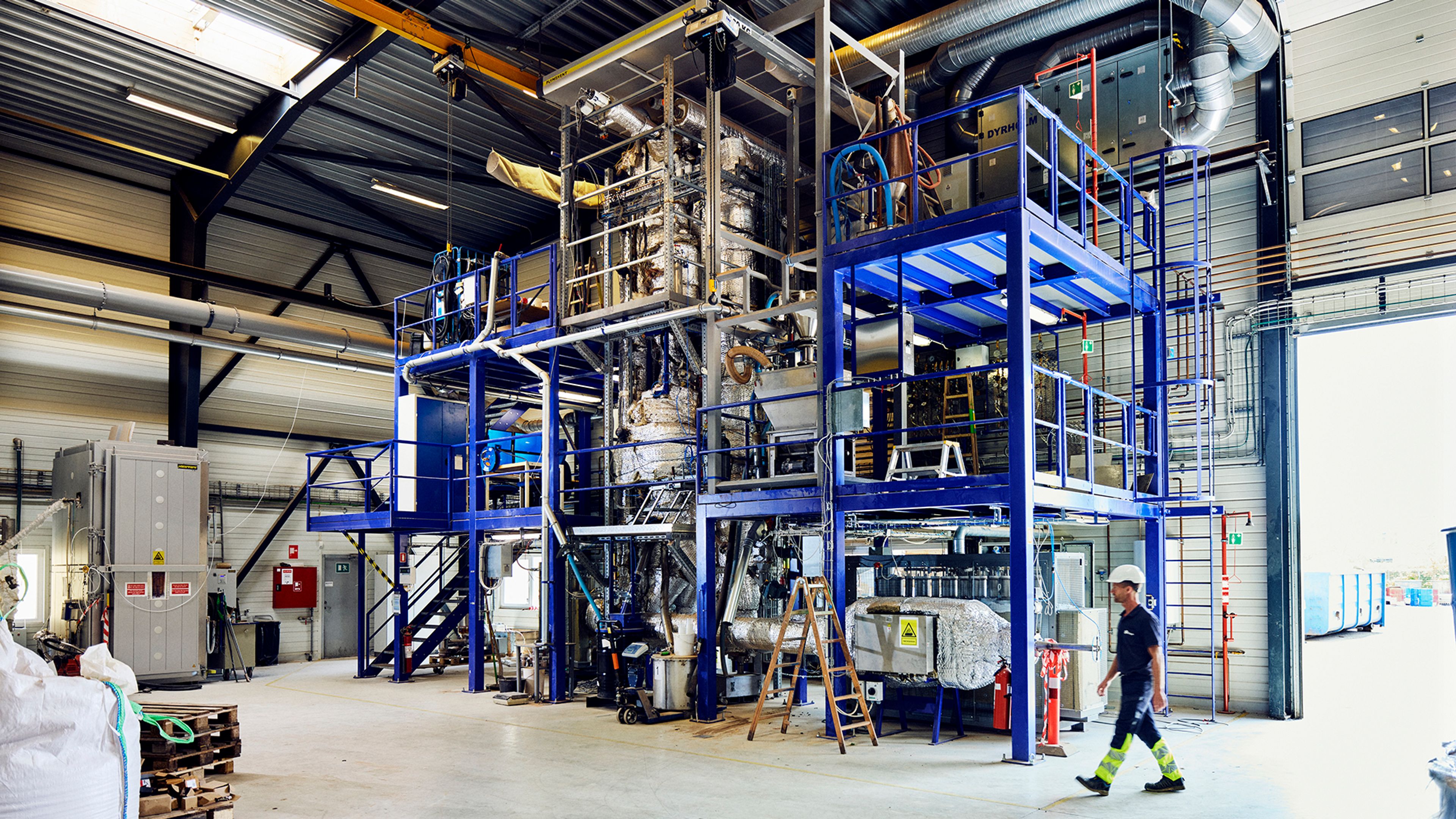
A decade of pilot scale testing, more than 150 years of history
Our facility in Dania, Denmark is one of the world's most advanced laboratories for the analysis of raw materials in cement production, receiving and testing tonnes of raw materials from all over the world. The Dania pilot plant was commissioned in 2010 and reconfigured for SCM activation and colour control in 2020, but the site has been processing materials in one form or another since it was originally built as a cement plant in 1872.
Considering a new investment, or looking for ways to improve your process?
Make the most of our experience, knowledge, and advanced facilities to ensure you’re getting optimal value and the most comprehensive evaluation of possible solutions.
What we offer
Clay testing process
Our materials testing process involves several stages, from the most basic initial analysis to full pilot-scale testing. In this way, we don’t waste your time or money testing materials that haven’t passed the first stages of evaluation.
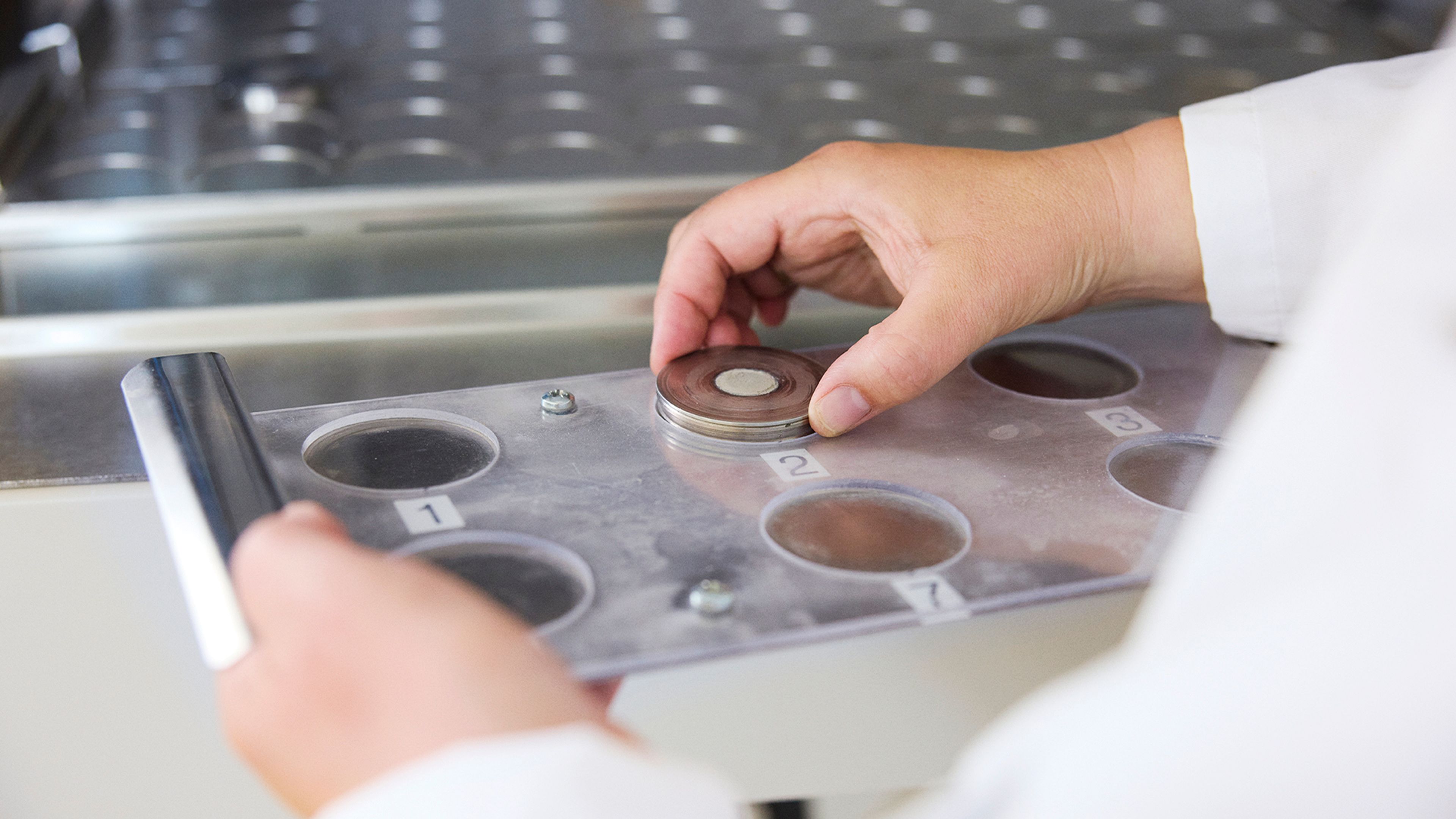
XRF, XRD and thermal analysis
For example, when we test clays for their potential as an SCM, we begin with one or more 15 kg samples, using XRF, XRD and thermal analysis to determine the chemical and mineralogical composition of the materials and ascertain:
- Does it contain the desired minerals and at sufficient quantities?
- Are there any red flags in terms of emissions?
- What about the physical properties of the clay?
The physical properties are important because they will have an influence on wear and handling and contribute to our analysis, where we’re asking, ‘is this feasible?’ as well as ‘is it financially viable?’. If it’s not, we’ll advise you to look for an alternative source for your materials. If it is, we’ll proceed with the next round of testing.
Calcining and emissions analysis
In the second stage of clay testing, we calcine the clay in our laboratory and undertake an emissions analysis, an initial assessment of grinding behaviour, and a characterisation of the calcined material. Again, this is an opportunity to screen those materials that are unsuitable for use in cement production, as well as ascertain what – if any – additional measures will be necessary to ensure the quality of the end product. All calcined clays are assessed for their potential for colour control, as we know end users prefer grey cement – however green it is.
Pilot scale pyroprocessing
In the third stage of testing, we utilise our state-of-the-art pilot scale pyroprocessing facility in Dania, Denmark, to complete final testing and determine the product’s suitability as a clinker substitute. This includes creating a finished cement using the calcined clay, undertaking strength testing, and giving you all the information you need to decide whether or not to proceed with your project. Step 3 is the time to experiment with process design, to define the optimum parameters for calcination, colour control and emissions. We usually invite customers to come to the plant at this stage, so they can see the results for themselves.
Further testing is also available if you’d like to experiment with the results of different cement mixes.
Advanced pilot plant and extensive R&D facilities
Cement plant laboratories are capable of carrying out many of the investigations we conduct at our world-class R&D facility – but not all. And of course cement plant laboratories are occupied with the day-to-day work of cement production and can’t usually spare the time or resources to conduct additional explorations.
The benefit of outsourcing materials testing to FLSmidth Cement is that we have extensive resources, experienced staff, and the time to conduct the thorough analysis required before launching into this kind of project.
What we offer
Lab testing for dry bulk materials
Our Pneumatic Conveying Test Laboratory (PT Test Lab) in Pennsylvania, USA, compliments the capabilities of our text center in Dania by serving the global dry bulk handling market. Its unique facilities and capabilities give you the information you need to be confident in your investments or resolve any pneumatic transport issues you’re experiencing. The Test Lab is designed to help you understand material behaviour during pneumatic transport. We analyse material flowability through a series of tests and provide a full report that will empower your decision-making.
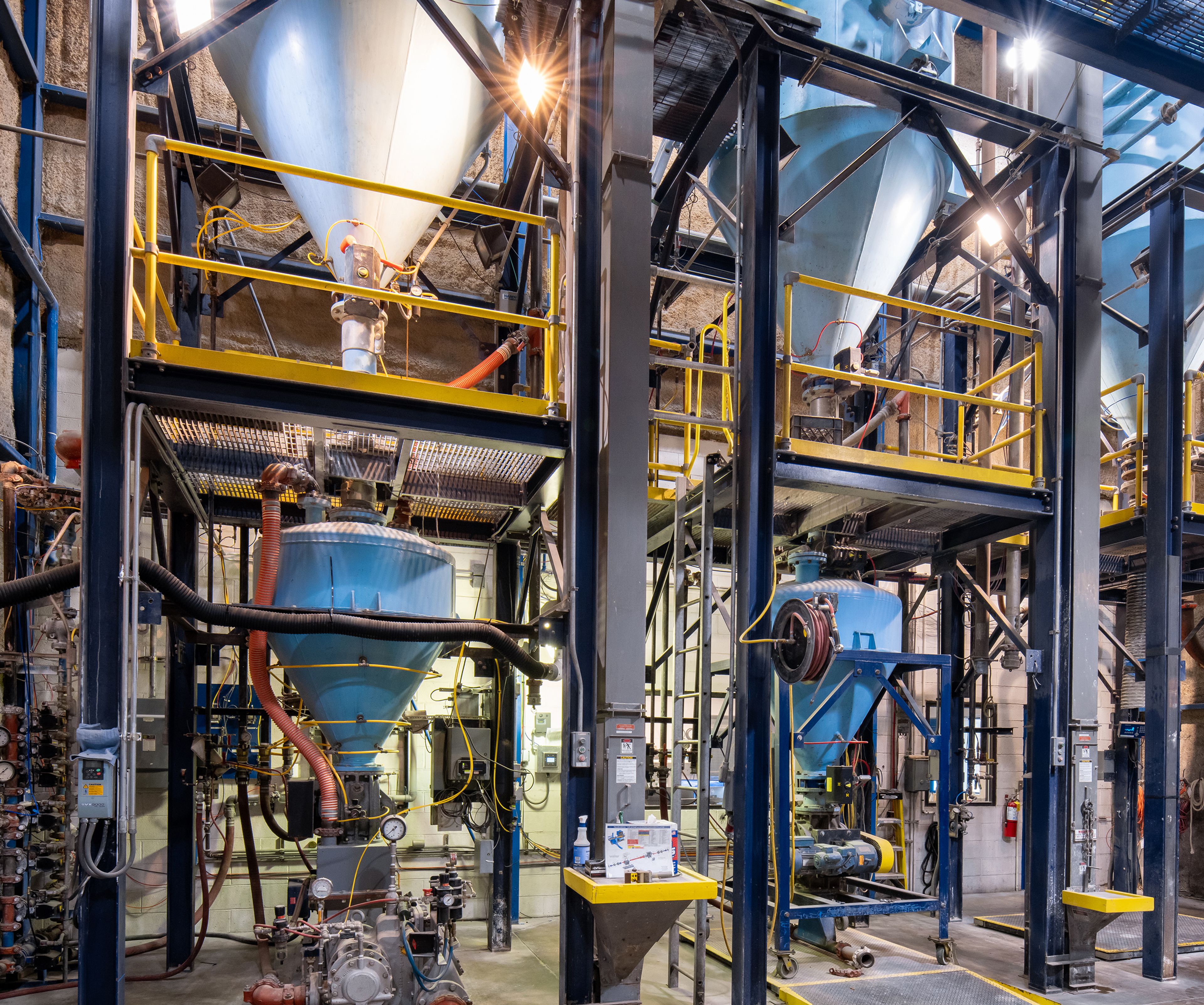