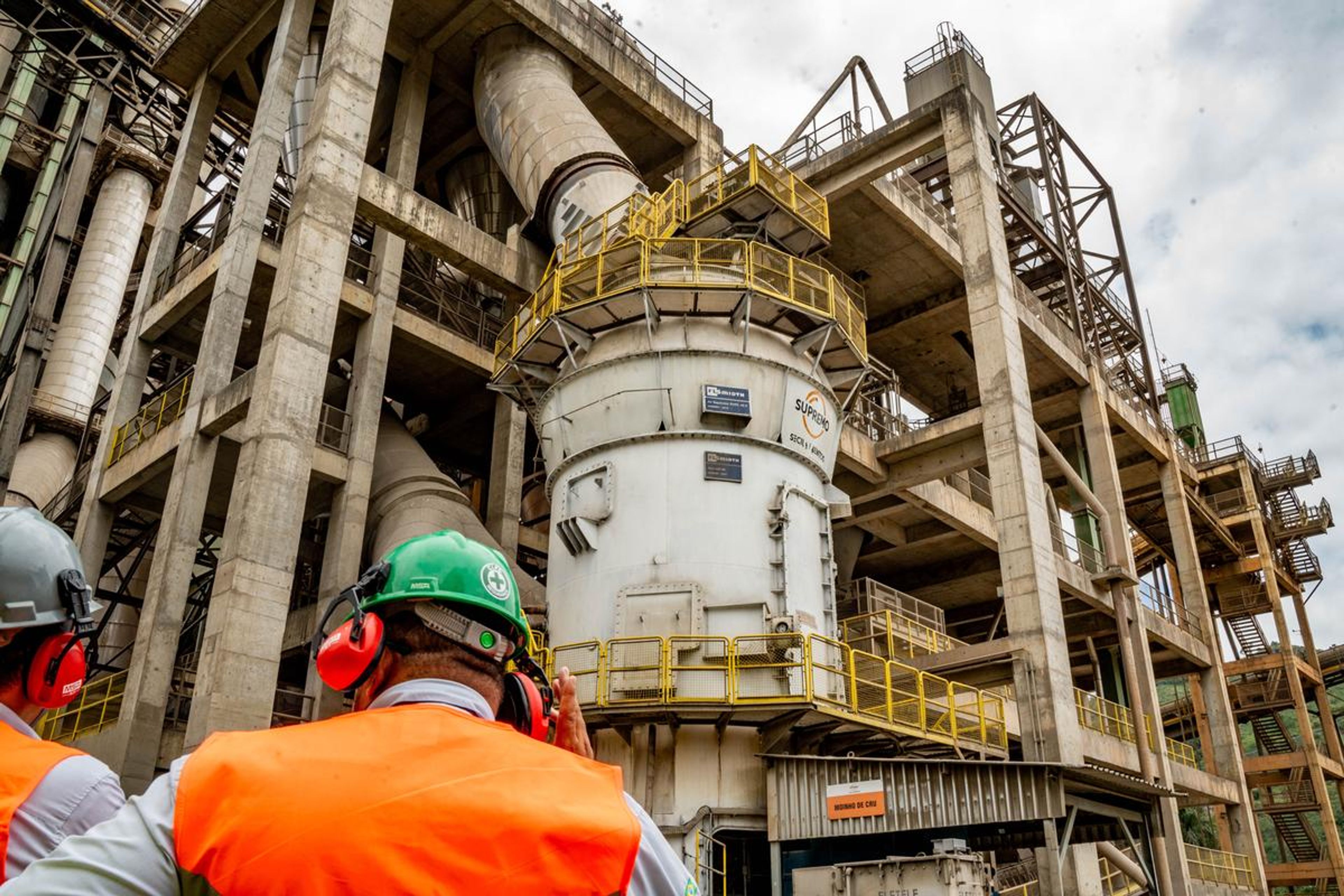
Long-lasting, flexible and sustainable wear solution for VRMs.
What we offer
Optimal wear protection for highly abrasive grinding conditions
VRM components are subject to severe wear. This is particularly true when grinding materials with high silica content and slags, such as are found in cement mills. This wear has a direct impact on a plant’s bottom line: a worn VRM roller reduces grinding efficiency, increasing the energy demand and costs of milling. Excessive wear of the mill lining may also result in increased vibration, exacerbating the problem and risking damage to the equipment. With our deep knowledge and experience of mill operations, we understand the causes of wear, how it impacts operations – and how to better protect against it. Not just on our own mills, but on any VRM in your production line. And we put that knowledge and experience to good use, alongside our partners at Castolin Eutectic, the best in hard facing services, to offer a long-lasting and flexible solution to your wear protection needs. Castolin Eutectic's leading knowhow and experience, combined with our knowledge of the material composition of our wear parts, enables us to give you the best recommendation of welding deposit materials, as well as the highest quality onsite service by a professional team of expert fitters. In addition, our wear segments (including the welded overlay) are recyclable at end of life, making them a more sustainable wear protection solution than non-recyclable ceramic-based solutions. Our hard facing services can also be packaged with other VRM maintenance services. These include our re-start service, which ensures optimal mill set-up after refurbishment, and our grinding circuit walkthrough, which provides a general evaluation of the grinding circuit, as well as in-depth inspection and analysis of critical elements.
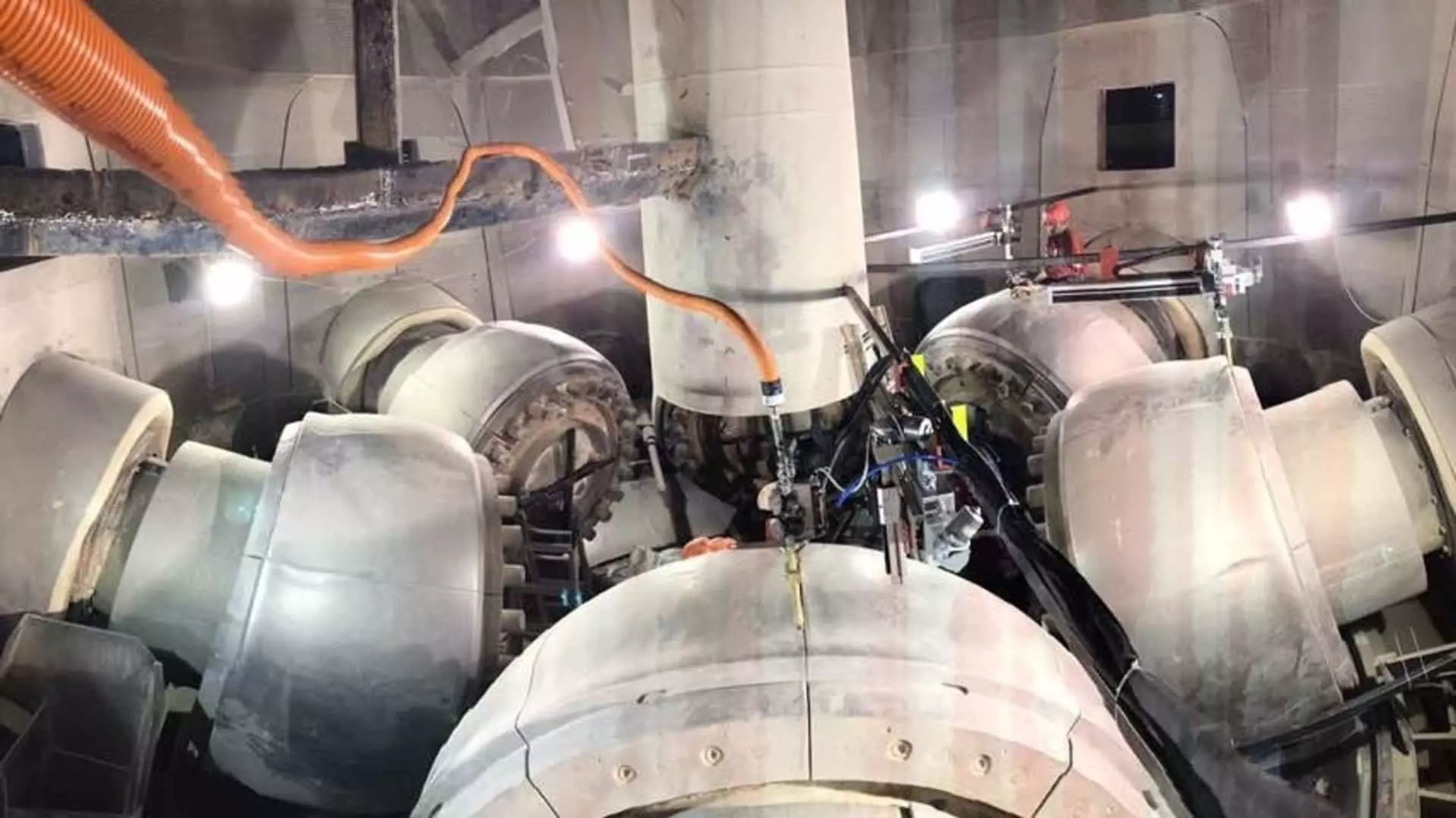
Is your wear solution optimised for your mill?
Our hard facing solution ensures the right approach for your mill is taken. We evaluate the wear and tailor our offering to best meet the unique requirements, guaranteeing the correct welding for the various mill types on the market.
Longer wear life
With our highly-controlled welding process, we achieve optimal bonding to the base materials, ensuring a longer-lasting wear solution and increased up time. Each segment is also individually checked against FLSmidth standards before the hard facing occurs to guarantee the best results. Hard facing offers a re-usable wear solution. Hi Chrome segments are suitable for repeated hard facing and can be refurbished in-situ to bring them back to the correct surface profile. This keeps downtime to a minimum and ensures the continued high performance of your VRM. Hard facing can also be re-welded on most applications (rollers and table), essentially reducing the wear rate of the equipment.
In situ application for minimum downtime
Hard facing offers a re-usable wear solution. Hi Chrome segments are suitable for repeated hard facing and can be refurbished in-situ to bring them back to the correct surface profile. This keeps downtime to a minimum and ensures the continued high performance of your VRM. Hard facing can also be re-welded on most applications (rollers and table), essentially reducing the wear rate of the equipment.
Recyclable at end of life
Hard facing of cast iron wear parts offer longer-lasting wear surfaces – even in high abrasive conditions – while in situ refurbishment can be done multiple times. This reduces the amount a part must be replaced, reducing material consumption over the lifetime of the VRM. And when the wear pieces do finally reach the end of their usability, they can be recycled at a standard foundry. This makes them a more sustainable option than segments made from ceramic composite materials, which require an special process to remove the ceramic components before re-smelting. As a result, the majority of foundries will not accept ceramic composite parts for re-use and they are often sent to landfill when they reach the end of their life.