Safe, efficient and economical pressure tank systems
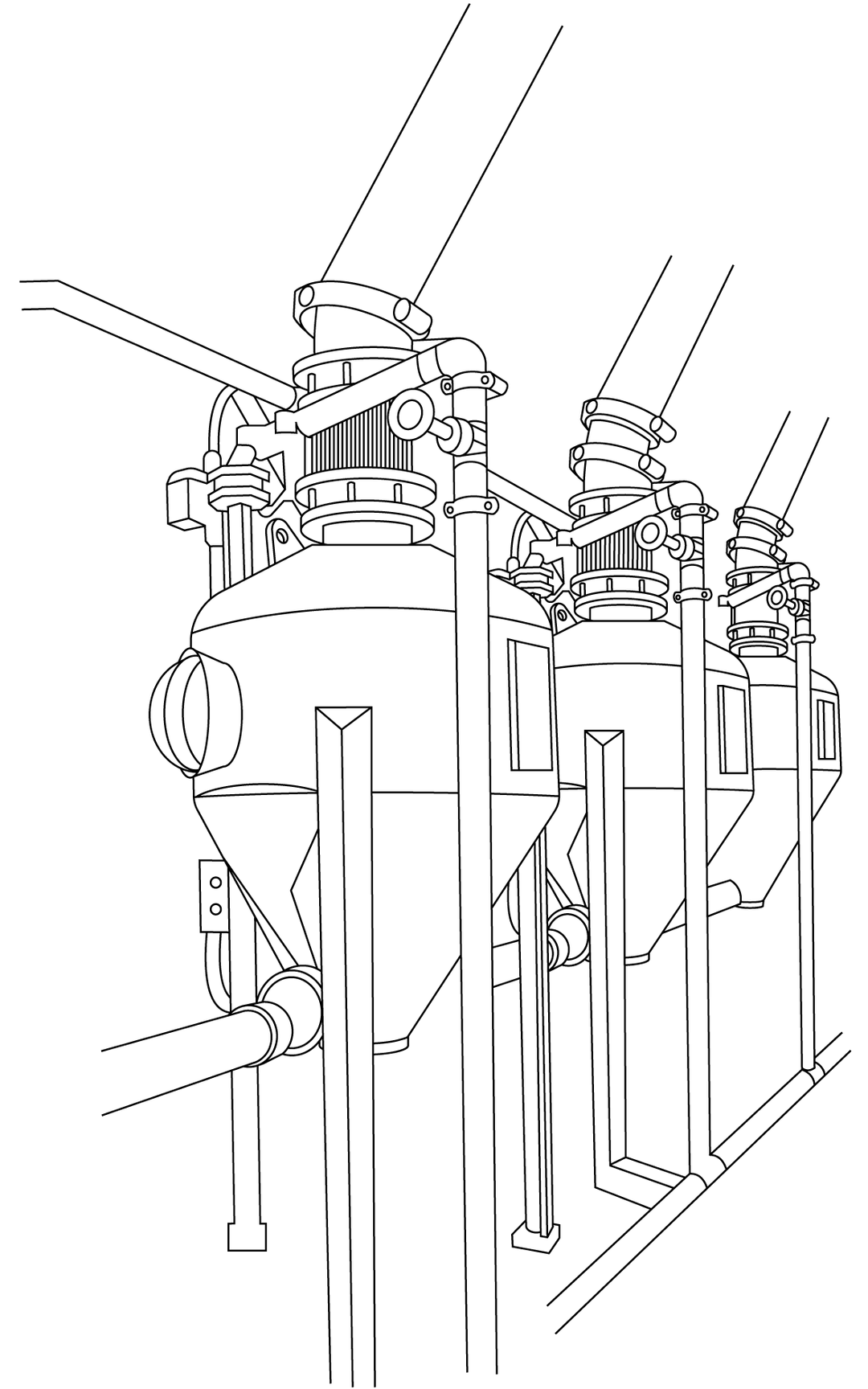
What we offer
Dense-phase conveying: the low-maintenance, energy-saving solution
Conveying solutions should always be tailored to the materials you are moving. If you get the wrong system, you will end up paying more on operations, more on maintenance, and more on your product, since material segregation and attrition can reduce the quality of your bulk materials. Our pressure vessel systems are designed to transport powdery and granular materials by dense phase conveying. Depending on the bulk characteristics, this can be a low velocity transport system that minimises wear and tear, while still permitting high conveying capacities. The comparable lower compressed air consumption of those conveying systems means lower operating costs. It’s also suitable for long distance conveying systems, if high pressure conveying air is available. 3.5 barg, 7.5 barg or 10 barg compressors are used for pressure vessel dense phase conveying systems. Put this together with the system’s long service life and low maintenance requirements and you have a low cost transport solution that ensures you deliver the quality your customers expect, with no delays. What materials are you moving? We offer the optimal pressure tank system to ensure lowest velocity, lowest wear, lowest energy consumption and highest availability
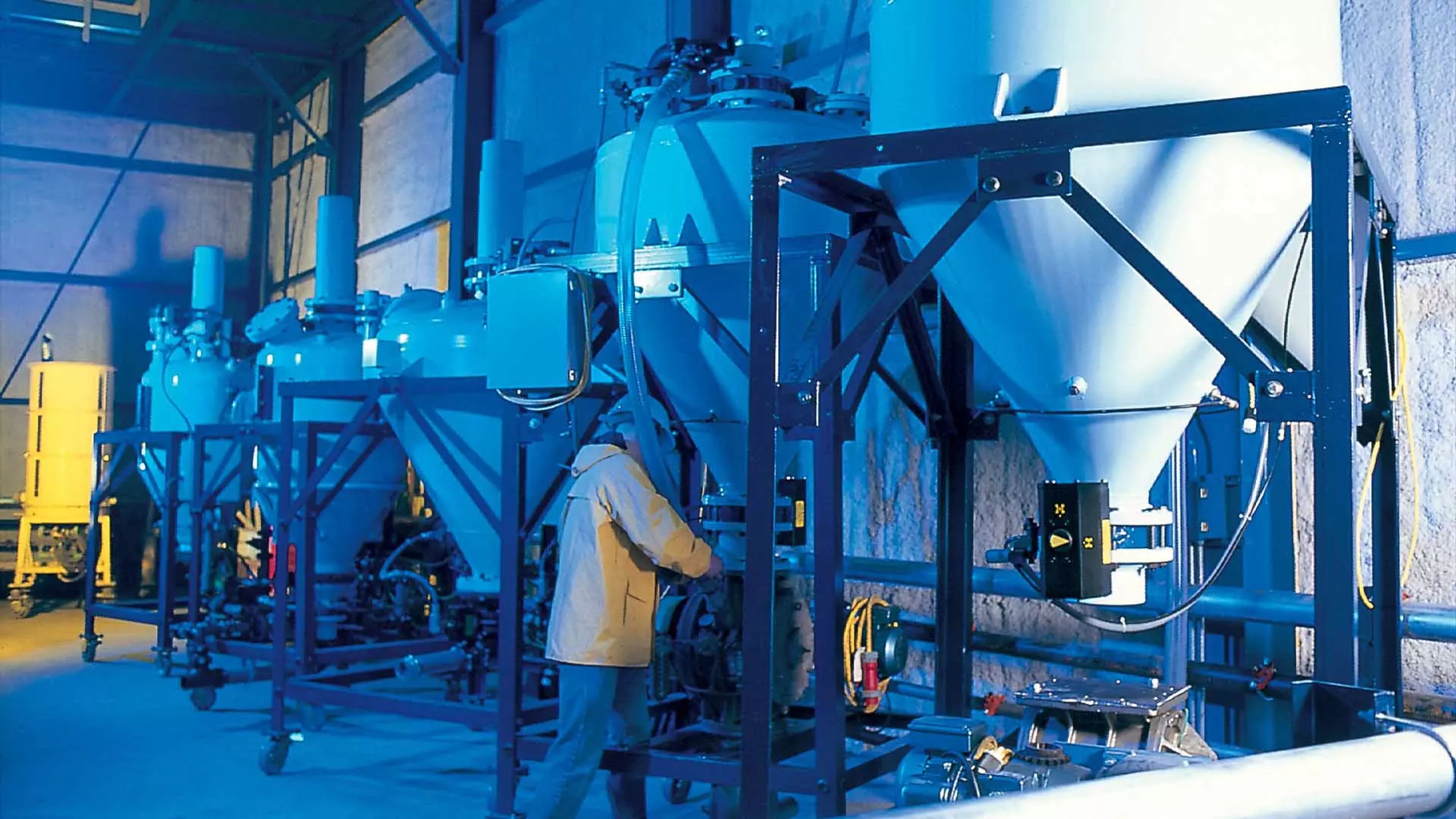
What’s the benefit of high pressure dense phase conveying?
Pressure tank dense phase conveying
Pressure vessel dense phase conveying is ideal for moving granular and powdery materials such as fly ash, alumina, cement and gypsum. These materials benefit from a smooth moving material stream. Abrasive bulk materials can damage your equipment if moved at higher velocities where they rub against the interior of the pipe, especially at the bends. At lower conveying velocities, as well as reduced wear, you also see much reduced grain attrition and segregation, so you maintain product quality. All these advantages also equate to a much reduced maintenance requirement. You get more life out of your equipment – and less stress in your life.
Efficient means of transport
As well as the reduced maintenance costs, pressure tank dense phase conveying is also a more efficient means of transport, since you can shift larger quantities of product with a lower amount of conveying air. That reduces the system’s energy consumption, which tends to be the biggest cost with systems like this.
Cost-efficient pressure vessel systems, built to last
For bulk material transport that is safe, low maintenance and economical, and which works for high capacities, long distances and abrasive bulk materials, FLSmidth Pressure Tank Systems are a solid choice.
Application range
Our range of pressure tanks can be used in any industry where dusty material needs to be transported. Each installation is tailored to the demands of the application and the material. Depending on your budget, materials and application, you have the choice of either single pressure vessels, or twin or triple systems. Single pressure vessels are used for batch-wise pneumatic transport; twin or triple pressure vessels also allow quasi-continuous operation. The pressure tank system is designed for capacities from 1 t/h up to 300 t/h and non-stop conveying distances up to 4000 m. Bulk material temperatures up to 250 – 300˚C can be handled with no problems. All the fittings and control valves are high quality, giving you the performance you’d expect from FLSmidth. It’s a fully automated operation with electronic controls that can be easily connected to your plant control system.
How does a pressure vessel work?
Normally, a pressure vessel will be filled from a buffer silo or a pre-hopper. The operation cycle of a pressure tank system is divided into the filling phase and the conveying phase. During the filling phase, the filling valve as well as the main vent valve on top of the pressure vessel are open. All other valves, such as the pressure tank outlet valve, which is directly connected between the pressure vessel outlet and the conveying pipe, are closed. The filling phase ends with the maximum level indication of the pressure tank or a well defined maximum filling time. The filling phase shall be minimised in order to maximise the resulting conveying phase and the equivalent conveying capacity. Once the pressure vessel is filled, both the filling valve and the main vent valve will be closed. The conveying phase starts by opening different valves for the distribution of the conveying air to different connections at the pressure tank, the conveying air booster chamber and the pressure vessel outlet valve. The conveying cycle of a pressure tank is always pressure-controlled. Therefore, pressure transmitters are installed at the conveying air supply upstream of the pressure vessel and at the beginning of the conveying pipe, downstream from the pressure tank. If the actual line pressure (back pressure from the conveying pipe) reaches the maximum value, the conveying air distribution will be changed in terms of opening/closing the different air valves. The conveying cycle automatically stops when the minimum line pressure is reached and the pressure vessel is empty. If necessary, the conveying pipe will be cleaned by the conveying air for a certain time. Afterwards, the pressure vessel can be filled again.
MaxiDense dense phase conveying system
Another option for your pressure tank system is MaxiDense dense phase vessel conveying technology. This system is suited to virtually all dry bulk powders. It’s best for long-distance, high-capacity applications. Why is it called MaxiDense? Because it maximises the time spent at the design pressure of the convey system, producing the most efficient conveying possible. First, the unique tank design has a fully fluidised bottom using Fullerator™ aeration elements that promote smooth flow of material from the vessel. Further, the upward flow, side discharge design assists in controlling material flow into the convey pipeline, working in conjunction with the other process controls of the system. The staged approach is far more efficient in charging the convey line with the proper amount of material than a single valve bypass. This means that the optimum material to air mixture enters the convey line to maintain design pressure throughout the convey cycle. In other words, it’s the most efficient means of tank conveying possible. The MaxiDense technology utilises a staged bypass to allow small increments of air to enter the convey line downstream of the tanks. Using several valves, a larger portion of convey air is bypassed at the beginning of the convey cycle when material more readily exits the tank. As the tank empties, more air is routed to the tanks to aid in tank cleanout.