At last: a hot/wet gas analysis system that excels in high sulphur conditions
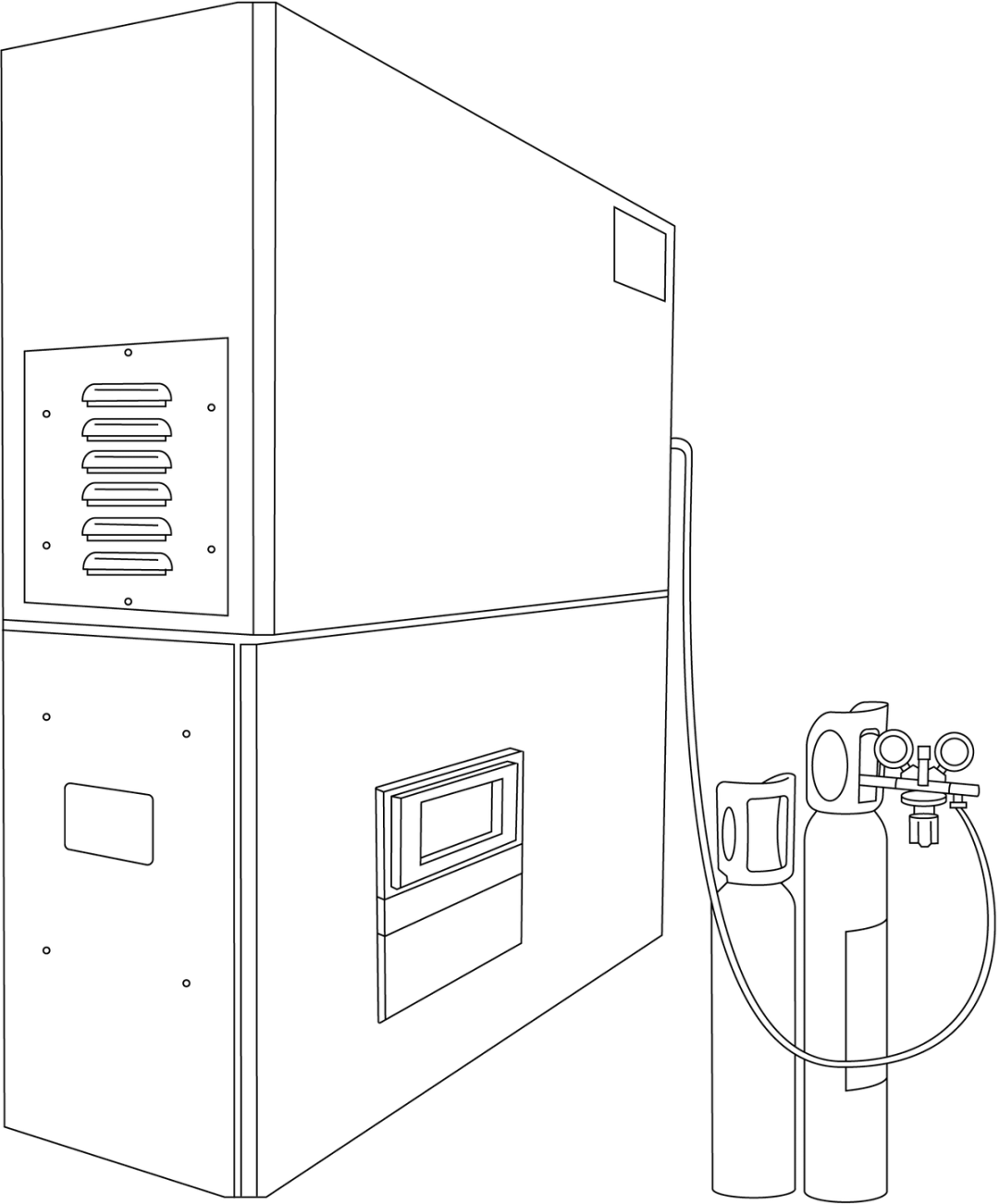
What we offer
Eliminating acid damage with the KilnLoq® HW Laser Gas Analysis System
Alternative fuels and raw materials with high sulphur content can damage your gas analysis system. Acid formation and corrosion can take your kiln inlet analyser out of operation altogether, leaving the kiln operator blind. Repairs are expensive and time consuming. And while you wait for your gas analysis system to be fixed, you can’t take the crucial measurements that can help you optimise the process and keep emissions in check.
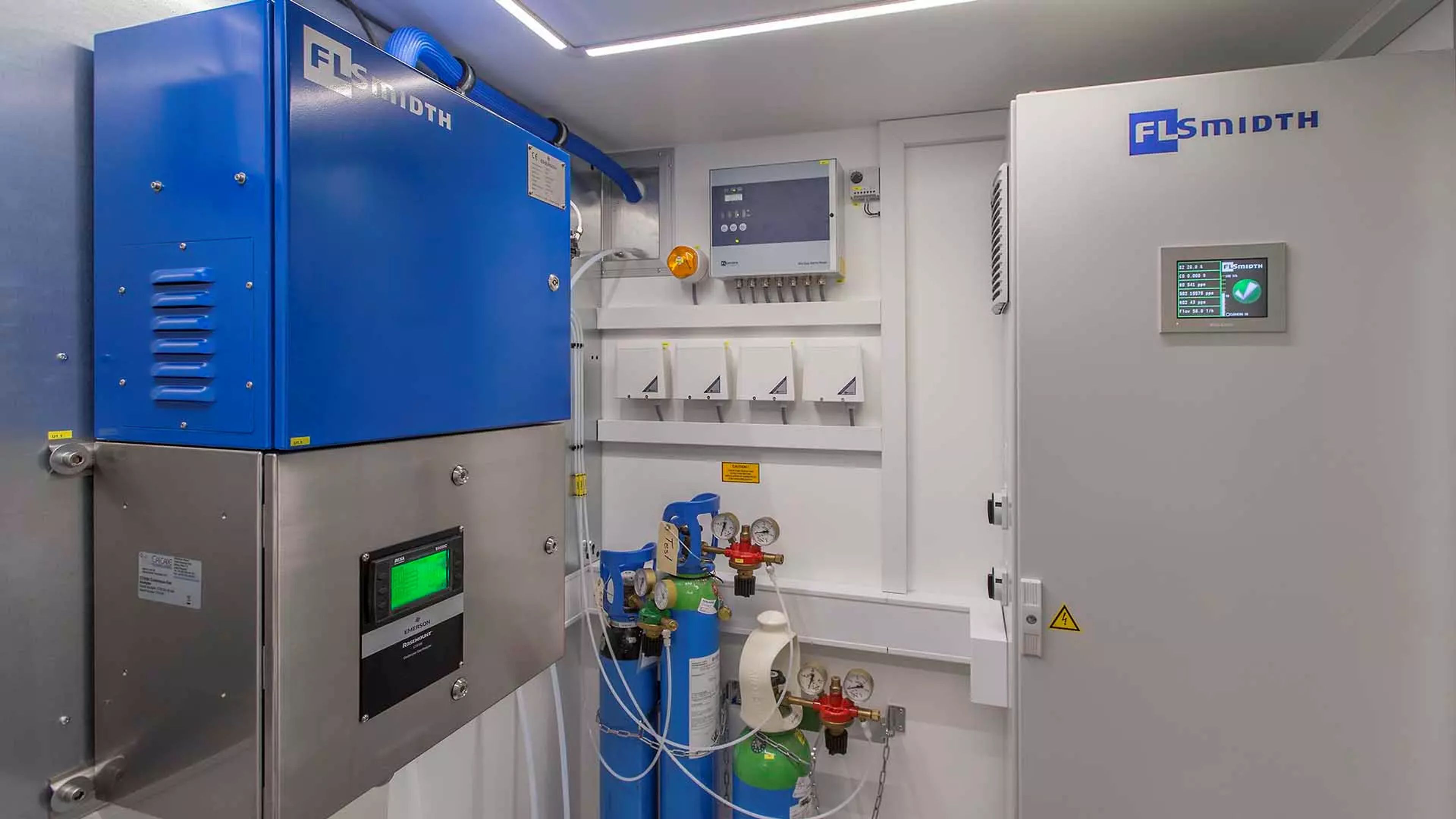
If your gas analysis solution can’t cope with your process, it’s not a solution. It’s a problem.
The KilnLoq® HW Laser Gas Analysis System is designed for these high sulphur conditions. It’s a state-of-the-art hot/wet gas analysis system based on laser technology that works in combination with our KilnLoq kiln inlet probe system. The temperature of all parts is kept at 180˚C – above the acid dew point – so that acid damage is entirely avoided. No expensive maintenance. No equipment downtime. No more prolonged data blackouts. Just fast, precise measurements. The KilnLoq® HW Laser System measures gases such as CO, NO, SO2, CO2, HCl and O2 at the kiln inlet. This insight enables kiln operators to optimise the air to fuel ratio for the best possible fuel consumption and clinker quality. This one-of-a-kind solution is designed for plants with high sulphur processes, whether because they are burning alternative fuels such as tyres and plastics, or because there is simply a high sulphur content in their raw materials. It’s also an ideal option for: Plants wishing to measure water-soluble components such as HCl and H2O; Plants experiencing high SO3 values that wish to measure SO2; and Plants that do not want to use H2O2 dosing due to safety and maintenance issues
The hot/wet solution
A hot/wet analysis system maintains a temperature above the sulfuric acid dewpoint so that the gas being measured is both hot and wet. Conventional gas analysis methods use a cold/dry system in which the gas being sampled is passed through a cooler and analysed in dry conditions at temperatures around 5˚C – a danger zone for acid formation. Hot/wet analysis is already widely used today, especially for CEMS (Continuous Emission Monitoring System) applications, mainly in the form of multicomponent FTIR analysers. However, these systems are commonly limited to lower measuring ranges than those required in process measurement, they’re typically complicated, and they’re high maintenance.
Proven laser technology
FLSmidth’s KilnLoq® HW Laser System is the only system of its kind. It utilises robust, low-maintenance Rosemount CT5100 laser technology, which has been around for over 20 years. During that time, this technology has successfully proven to offer reliability, a long lifetime and instant response time.
Hot/wet laser technology: A unique combination
The KilnLoq® HW Laser System is the only laser-based hot/wet analyser solution on the market;
The simplest hot/wet analyser solution with the least maintenance requirements and the most accurate hot/wet gas analysis solution available.
Hot/wet laser technology: A unique combination
The KilnLoq® HW Laser System is:
- The only laser-based hot/wet analyser solution on the market;
- The simplest hot/wet analyser solution with the least maintenance requirements and the most accurate hot/wet gas analysis solution available.
Fast, precise hot/wet gas analysis without the downtime
High sulphur levels cause big problems
Hot/wet analysis eliminates acid damage
Hot/wet technology compared to cold/dry
- Less consumption of wear/spare parts – expected saving over 5 years: EUR 8000.
- Savings on maintenance hours – reduced from 2 hours/week to 2 hours/month; expected saving over 5 years: 400 hours.
- Savings on man-hours for calibration due to less drift on analyser – reduced from once per week to once per year; expected saving over 5 years: 250 man-hours.
- Savings on repairs due to acid problems – expected savings over 5 years: EUR 35.000
Introduced in 2003, the KilnLoq® probe has proven to be the optimum solution for kiln inlet gas analysis with more than 300 references worldwide. While other products may have bends, obstacles or deposits that can get in the way of samples, the KilnLoq® probe uses the One Pipe system, which samples gas in a straight pipe. The process gas enters the filter housing through the centre of the pipe, where it passes through a coaxial filter for collection and analysis. The filter itself is built into a section of the One Pipe sample probe and the entire probe system is heated to 180°C, preventing the condensation of sulphuric acid.