Increase production, cut costs, and reduce energy consumption and carbon footprint
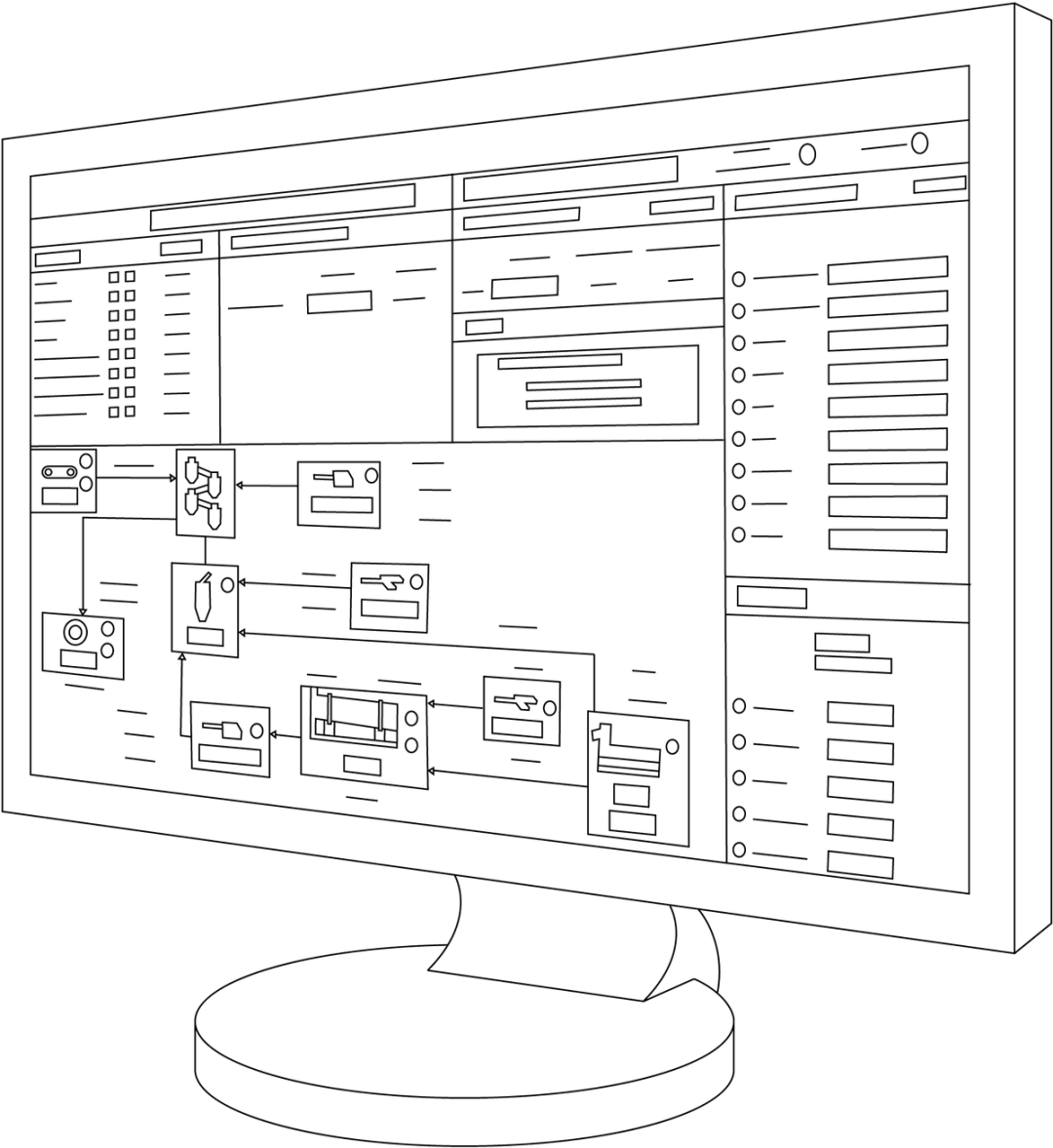
What we offer
An intelligent next-gen process control solution for the cement industry
Our ECS/ProcessExpert software provides advanced process control and optimization for the cement industry. Bringing together our experience and knowledge of the cement making process with the most advanced control technologies, it delivers maximum efficiency and higher profitability, while also supports your sustainability ambitions, including reduced carbon emissions and higher alternative fuel substitution rates.
Let's talk about what's in it for you
Built by cement experts with over 50 years of automation expertise, ECS/ProcessExpert v9.1 delivers measurable results that directly impact plant performance and profitability. Our proven solution consistently demonstrates significant improvements in production efficiency, energy consumption, and emissions reduction across global implementations. The system enables higher alternative fuel usage while substantially reducing process variability for more stable, predictable operations. Advanced process optimization also reduces equipment wear and minimizes downtime, protecting your critical investments while delivering compelling returns.
Increase production by up to 4-7%
Cut power consumption by up to 4-7%
Lower CO2 emissions by up to 2% and cut NOX emissions.
Reduce equipment wear and minimize downtime
Deliver ROI within a year (depending on application)
Reduce process and quality variability by up to 40%
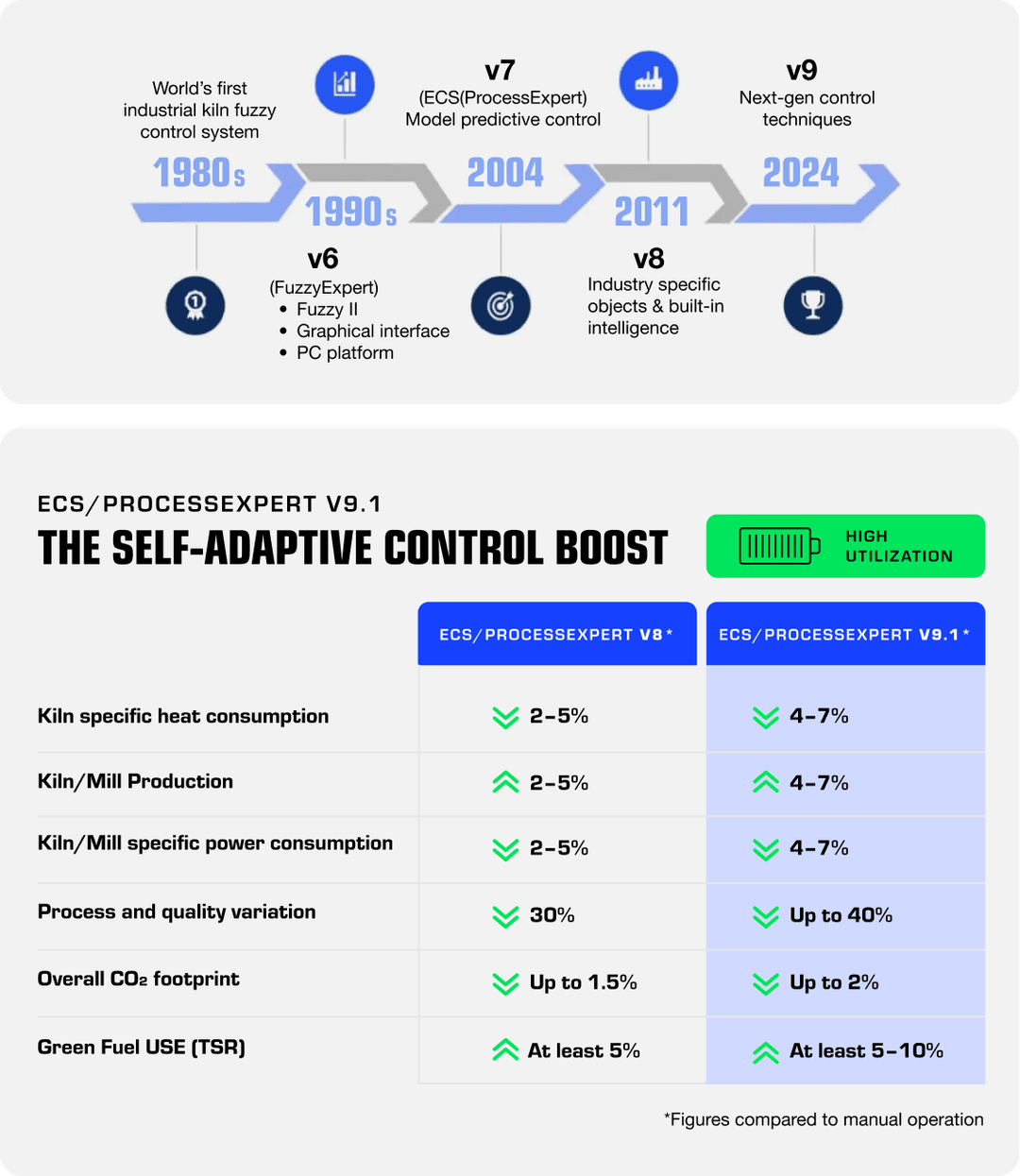
Revolutionary self-adaptive process control technology for higher utilization
The self-adaptive controller at the heart of v9.1 sets new standards for intelligent process control. This self-learning system continuously adapts to changing process conditions in real-time. Unlike traditional systems requiring multiple controllers, our adaptive technology handles all process scenarios in one controller - maintaining optimal performance during process disturbances, varying raw material conditions, and alternative fuel operations far more reliably than conventional approaches.
Dinesh Sampath, Global Product Manager Process Optimization
The Future of Process Control
A Vision of Intelligent, Connected Operations
Traditional process control systems struggle with cement's complex nature, creating competitive disadvantages and missed targets. FLSmidth Cement is pioneering the automation transformation with advanced process control software that delivers unprecedented operational visibility and real-time AI solutions for prediction, anomaly detection, condition monitoring, and optimisation. Our new service-based approach adds to that and transforms how plants can access these cutting-edge technologies. Rather than large capital investments in software that becomes outdated, our subscription model converts expenditure into predictable operational costs while ensuring continuous access to the latest innovations. This includes upcoming emission control applications, enterprise-level analytics, and more AI-driven optimisation capabilities-delivered regularly - constantly positioning your plant ahead of the competition.
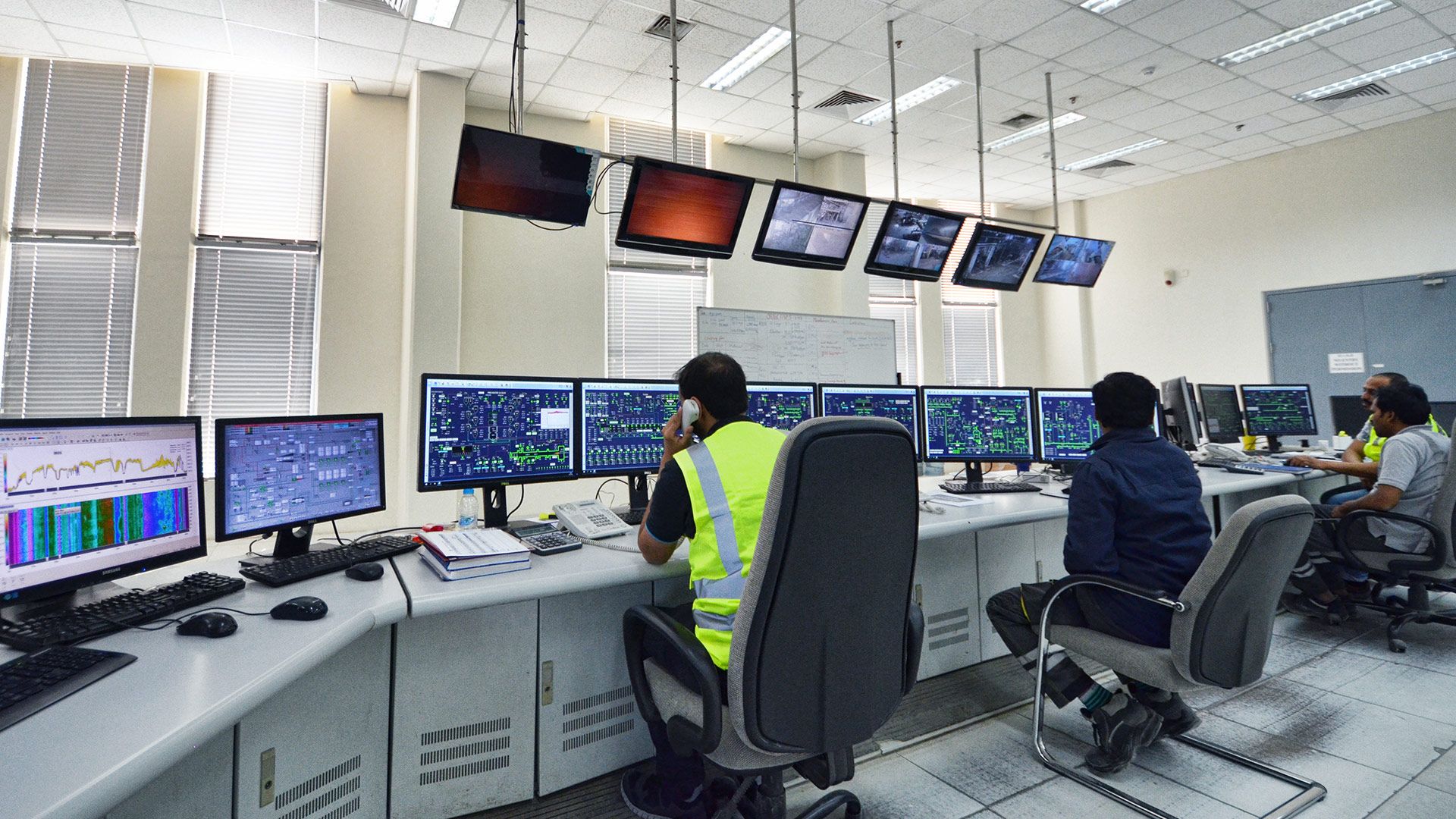.jpg?w=3840&q=80&auto=format)
ECS/ProcessExpert® Applications
Comprehensive process control across your entire cement production flowsheet, with advanced applications for every critical operation and continuous expansion of our solution portfolio.
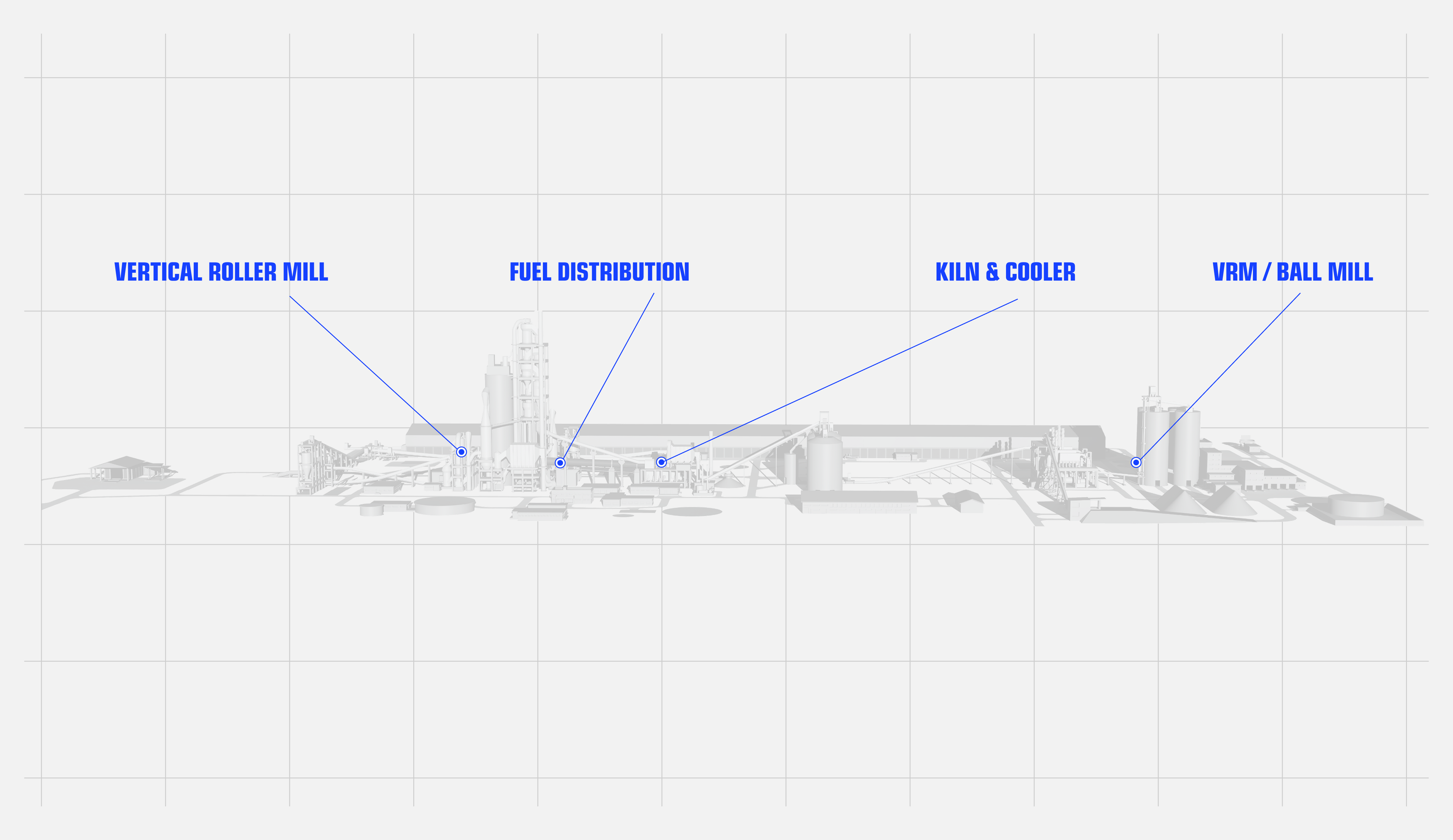
Vertical roller mills
Vertical roller mills are recognised for their higher efficiency compared to ball mills; however, they operate in a fast-changing, dynamic environment where conditions can shift within minutes, requiring close attention to process conditions. Our advanced multi-input multi-output control strategy improves operating capabilities and efficiency, delivering significant reductions in specific power consumption and tighter mill control.
The solution includes predictive models that enable smooth, controlled start-up to rapidly achieve process stability and minimise machine wear.
Fuel Distribution
Our customisable fuel distribution module enables plants to substantially increase alternative fuel thermal substitution rates (TSR)-supporting the transition to greener plant operations and lower fuel costs. The application ensures the best possible fuel mix based on cost and heat value, delivering a reliably stable process regardless of input material variability.
This intelligent optimization enables meaningful increases in green fuel use while maintaining process stability and supporting significant CO2 emissions reductions.
Kiln & Cooler
An unstable pyroprocess is a headache, leading to inefficient production and variable clinker quality. Expert process control via ECS/ProcessExpert® software avoids these negative outcomes by stabilising kiln and cooler operations, resulting in increased production, fewer cyclone blockages, reduced kiln ring formation, and more consistent clinker quality.
The system also delivers substantial reductions in CO2 and NOX emissions while enabling higher alternative fuel utilization rates.
Ball mills
Ball mills are energy intensive machines where conventional control loops prove insufficient, particularly in handling process delays and internal couplings that can cause operational conflicts. The ECS/ProcessExpert software employs advanced control strategies to deliver lower specific power consumption while ensuring correct product fineness is achieved. It automatically adjusts fresh feed to ensure best-possible throughput and quality for any given cement recipe. For grinding circuits producing different cements, it automates the switch between product types via predefined recipes, enabling quicker, more efficient changeover.
v9 Features for unparalleled process control
Meticulously engineered features combining cutting-edge AI and cloud technologies with comprehensive out-of-the-box functionality, all designed for seamless customization to your unique operational requirements.
Performance Enhancement That Adapts and Endures
ECS/ProcessExpert v9 transforms process control through model-less multivariable technology that intelligently adapts to time-variable process dynamics with inherently adaptive and predictive capabilities. The self-adaptive controller doesn't just respond - it evaluates process information in real time, delivering long-term process stability that traditional static systems simply cannot achieve. Built-in intelligence ensures exceptional consistency across implementations while dramatically reducing time spent during commissioning, enabling every installation to reach optimal performance faster than ever before. Whether facing varying raw material properties, alternative fuel fluctuations, or seasonal operational changes, the system maintains peak efficiency through continuous intelligent adjustment that is more resilient to process changes and capable of superior dynamic predictions than conventional approaches.
Advanced Analytics for Enterprise-Wide Optimization
Unlock unprecedented operational intelligence as ECS/ProcessExpert v9's enterprise-level PXP Insights seamlessly integrate with plant-level deployments to report and analyze performance across multiple cement plants in real time. This powerful system provides comprehensive visibility that empowers you to identify controller performance and stability degradation before it impacts operations, while measuring performance improvement through detailed KPI analysis that quantifies every operational gain. This advanced approach to data analysis in real time ensures you're not just controlling processes - you're continuously optimizing them based on actionable insights that drive measurable business value across your entire operation portfolio.

Model-less multivariable process control that adapts intelligently in real time
Cement plants face constant variability in raw materials, alternative fuels, and operating conditions that challenge traditional control systems. FLSmidth Cement's self-adaptive controller represents a breakthrough in process control - eliminating the need for complex mathematical models while delivering superior performance. This innovative technology evaluates real-time process information to make intelligent adjustments automatically, adapting to changing conditions without requiring operator intervention or system retraining. The controller's rate-predictive approach handles both linear and non-linear processes with equal effectiveness. Unlike conventional Model Predictive Control (MPC) systems that rely on static parameters and historical models, our self-adaptive technology is more resilient to process changes and generates superior dynamic predictions compared to traditional approaches. This translates to fewer process upsets, higher utilization rates, and consistent performance even when fuel quality varies or equipment characteristics change over time.

Enterprise-level integration for groupwide performance optimisation and sustainability tracking
Multi-plant cement producers need clear visibility into which facilities are performing well and which require attention. FLSmidth Cement's cloud-based PXP Insights 2.0 module seamlessly integrates with plant-level ProcessExpert deployments to provide enterprise-level benchmarking across your entire operation. The platform enables benchmarking of individual equipment performance against the group average, comparing critical metrics like heat consumption and production efficiency to identify top performers and improvement opportunities with just a few clicks. Dedicated sustainability dashboards provide global visibility of operational CO₂ savings achieved by ProcessExpert software, making environmental reporting effortless. Real-time KPI monitoring spans multiple sites, delivering the insights needed for focused resource allocation. This enterprise-level analytics platform transforms complex multi-plant data into clear, actionable intelligence that drives both operational excellence and sustainability performance across your cement operations.

Essential visibility for optimising controller performance and detecting degradation
Maintaining optimal control performance requires continuous monitoring to detect degradation before it impacts plant efficiency. FLSmidth Cement's Control Loop Performance Monitoring (CLPM) identifies underperforming control loops and diagnoses problems for corrective action with just a few clicks. The system uses key statistical metrics - standard deviation for process stability and mean absolute error for target achievement - to ensure parameters remain stable precisely at target rather than merely stable. Visual time series and column charts provide immediate insights across flexible timeframes from hours to months. CLPM proactively detects when processes become unstable and performance drops, enabling corrective action before efficiency losses occur. This comprehensive monitoring ensures precise and efficient control of main process parameters, guaranteeing that the greatest levels of optimisation are consistently identified and delivered across your cement operations.

Collaborative framework for collective AI development and seamless real-time deployment
Modern cement operations require advanced analytics that bridge data science innovation with real-time process control. FLSmidth Cement's PXP DataBooks provides a collaborative framework designed specifically for skilled process specialists and data scientists to collectively develop new AI solutions. These solutions deploy seamlessly into any control strategy in real time, enabling immediate operational benefits without process interruption or complex integration challenges. The platform facilitates inference of machine learning and deep learning models trained offline in preferred environments, bringing advanced AI capabilities directly to your plant floor. Applications include prediction, anomaly detection, and condition monitoring that enhance operational intelligence across your organization. This shared development approach accelerates AI adoption while ensuring advanced analytics integrate naturally with existing ProcessExpert control strategies for maximum operational impact.

Comprehensive performance optimisation through expert partnership, continuous monitoring, and strategic investment protection
Every ECS/ProcessExpert installation includes a comprehensive one-year proactive service agreement featuring bi-monthly remote service visits and annual onsite support. Our experts continuously monitor KPI parameters and analyze system utilization data transmitted to FLSmidth Cement's processing center, delivering advanced performance reports that identify both realized benefits and untapped optimization opportunities. This proactive approach ensures your investment delivers maximum value while maintaining peak operational performance. The PlantLine Essential service framework provides the foundation for expanded support through optional modules including lifecycle management, cybersecurity, and remote technologies. This flexible approach converts traditional capital expenditures into predictable operational expenses while ensuring access to latest software innovations. Expert guidance extends your operational capabilities and helps achieve sustained competitive advantage through continuous process optimization and technology currency.
Combining process control and AI technologies
Carefully crafted modules and technologies that work with existing controllers and control systems
FLSmidth Cement's ECS/ProcessExpert software represents the evolution of five decades of advanced control expertise, now enhanced with breakthrough innovations in adaptive intelligence and artificial intelligence integration. These latest developments eliminate traditional dependencies on complex mathematical models while introducing real-time learning capabilities that respond dynamically to changing process conditions. The result is a comprehensive suite of customizable technologies that allow plant personnel to tailor functions to their unique needs while working seamlessly with existing infrastructure. Each process control application combines proven techniques such as model predictive control and fuzzy logic rules with modern machine learning integration. The model-less approach requires no dependency on detailed process models, making it well-suited for diverse control environments. This advanced system excels at handling a wide range of challenges, including adaptation to plant upgrades and testing of new solution prototypes across global operations.
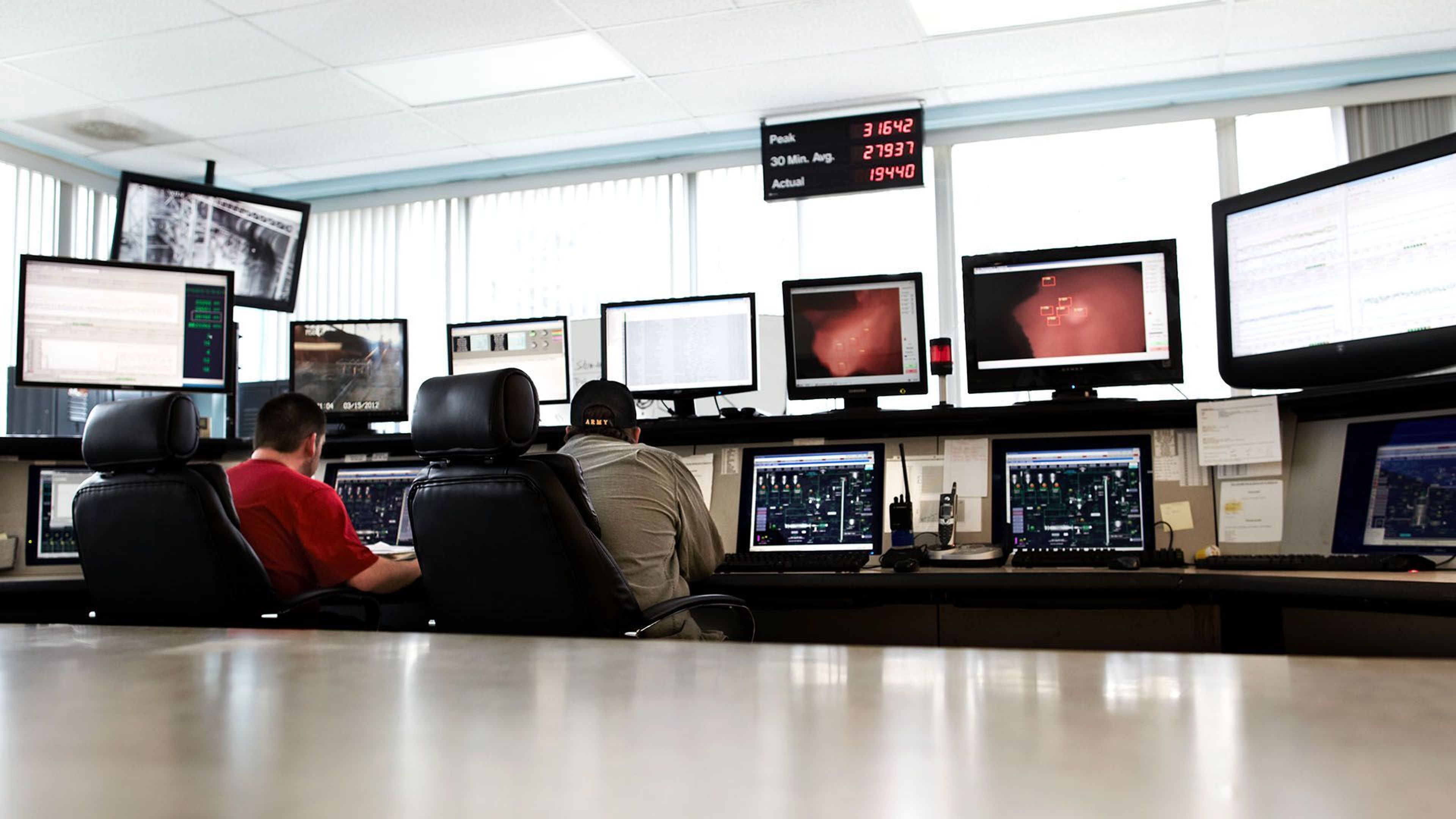
With out-of-the-box features and
functionality that you can rely on
- Smart objects: intelligent process objects that integrate process and control engineering knowledge.
- Modelling tool that helps find the process variables and actuators correlating to the model.
- Fuel distribution (pyroprocess) module for controlling the use of alternative fuels in the kiln.
- Module for controlling recipe changes in the raw and finish mills.
- Mill ramp-up facilitates ramp-up of grinding circuits, ensuring nominal production is achieved faster and with less process variability.
- Target adaptation continuously adapts the operational targets to ensure maximum production and minimum fuel/energy consumption are achieved.
- Advisory mode recommends actions to the operators when the system is not in operation.
- Holistic solutions that optimize mill and kiln operation, customized to each plant.
- Decision tree component illustrates the process status and reveals the underlying reasons to the operator.
.... and many more features.
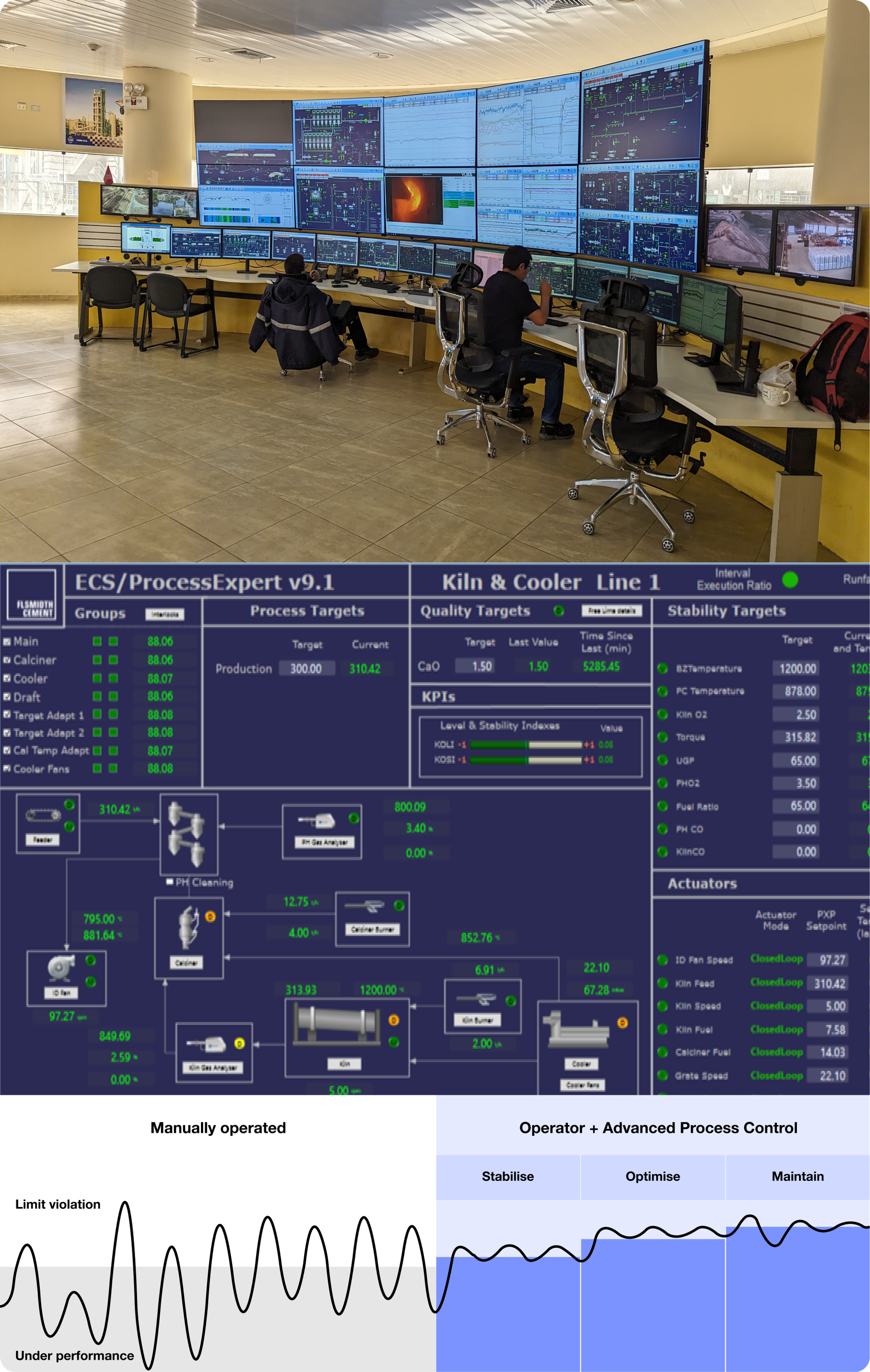
CEMEX Cement Plant, Croatia
The process control solution to Improve your bottom line
We’ve built the ECS/ProcessExpert solution (PXP) to help increase your productivity by reducing costs and lifting output. Our software will quickly have you producing more with less.
Increase production and cut energy consumption by up to 7%
Our advanced process control software delivers unparalleled process stability for optimal productivity and efficiency. A typical production increase of up to 7% is the result, alongside a similar reduction in energy consumption – with significantly higher values in the double digits reported at some plants.
Lower CO2 emissions by up 2% and cut NOX emissions
An unstable pyroprocess is a headache. Our advanced process control software offers the cure. By stabilising kiln and cooler operations, it not only improves process efficiency, productivity, and product quality; it also reduces CO2 and NOX emissions.
Reduce equipment wear and minimise downtime
Running your plant under less-than-optimum conditions takes a toll on your equipment, reducing the life of assets and potentially resulting in costly downtime. Our advanced process control software reduces wear on your assets by ensuring optimum and stable operating conditions throughout the process.
Deliver ROI with a year
We’ve built the ECS/ProcessExpert solution to increase productivity by reducing costs and lifting output. The result? It quickly has you producing more with less for rapid return on investment.
Reduce process and quality variability by up to 40%
Using the latest process control techniques to continuously analyse and precisely adjust process conditions, even correcting for process disruptions, our advanced process control software delivers a significant reduction in process variability, which is reflected improved consistency in product quality.
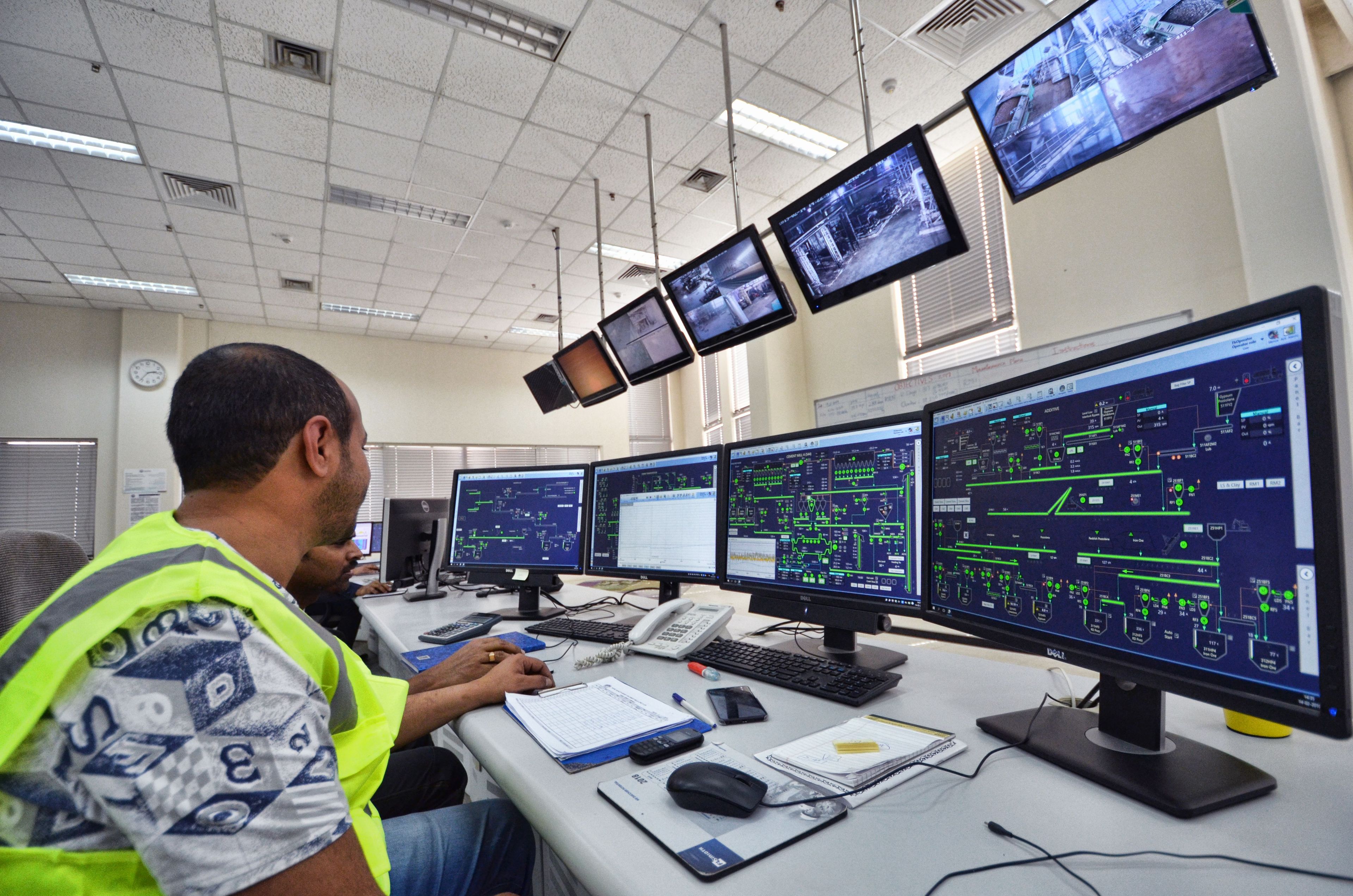
The process knowledge experts
Developed by cement experts for the cement industry
Two factors set our ECS/ProcessExpert software apart: domain expertise and proven implementation success. We're the only advanced process control software solution built exclusively for cement by cement process experts. This means software that understands your unique challenges from day one. You'll have confidence in our ability to deliver real impact at your plant while our remote team of experts ensures the system performs exactly as you need it to. ECS/ProcessExpert solutions are available for all critical cement processes, backed by an implementation methodology built for success, that reflects decades of cement industry experience. This proven approach delivers rapid deployment with minimal operational disruption. Ready to see the real-world results?
Creating Results in Cement Process Control for Five Decades
Five decades of proven expertise, thousands of successful installations, and measurable performance improvements - proven results you can measure, relationships you can trust. That's why leading cement producers worldwide choose ECS/ProcessExpert to deliver exceptional operational results.
0+Installations
Proven global performance with thousands of advanced process control systems successfully deployed across cement plants worldwide, delivering consistent results and operational excellence in diverse industrial environments.
0+Years
Unmatched automation expertise built over five decades of cement industry leadership, combining deep process knowledge with cutting-edge control technologies to deliver solutions that reliably enhance plant capabilities.
0YEAR TO ROI
Rapid return on investment typically achieved within twelve months through measurable improvements in production efficiency, energy reduction, and process optimization—making PXP a compelling business case for immediate and long-term value.
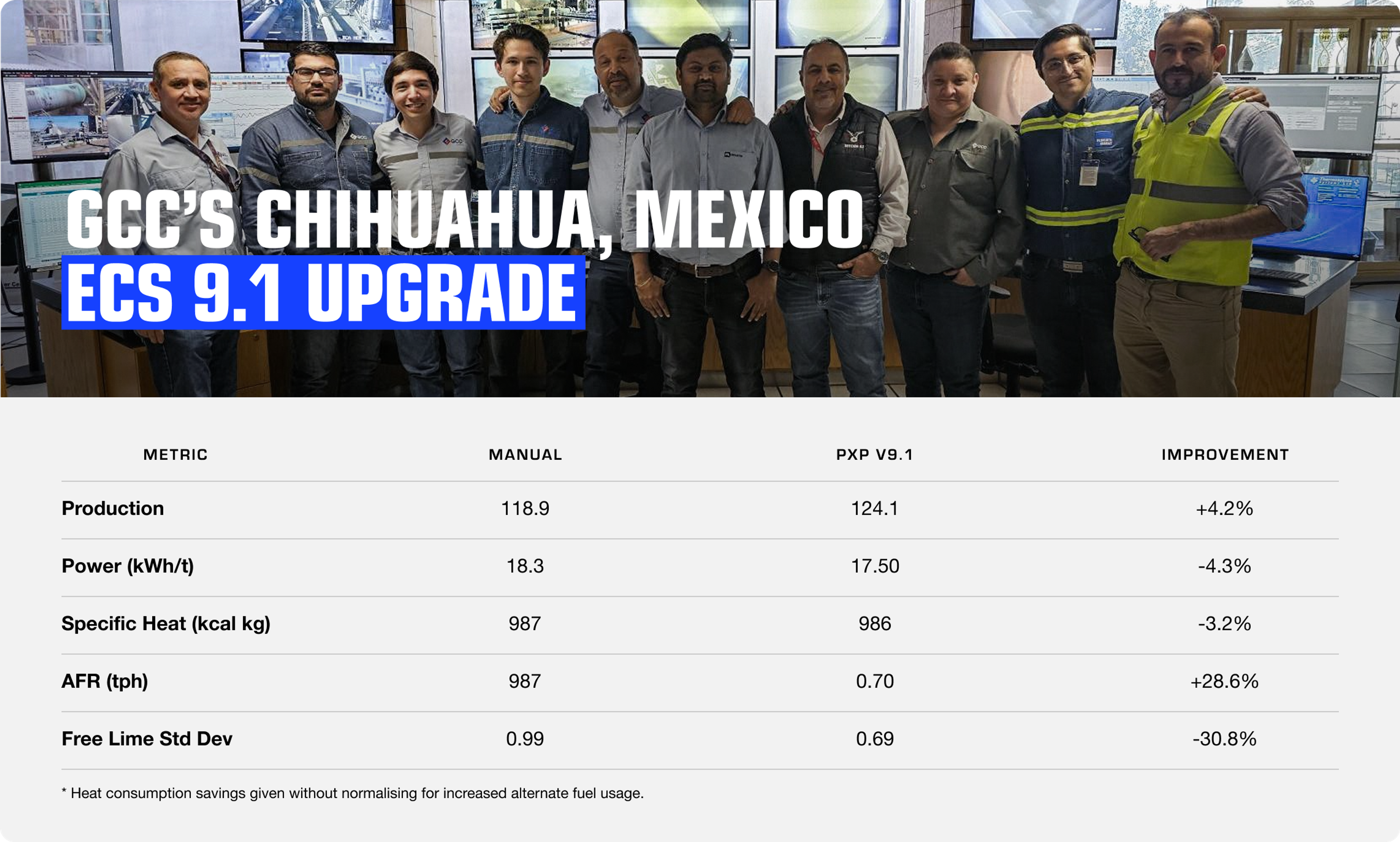
Ing. Carlos Guerrero Anaya Regalado, production manager, GCC Chihuahua plant
Transform Your Plant's Performance Today
Ready to boost production, profitability and utilization while cutting energy costs, lowering emissions and reducing equipment wear and downtime? Our ECS/ProcessExpert® software delivers proven results across installations worldwide with process control technology that cement industry leaders trust.
downloads
Brochures
ECS/ProcessExpert Advanced process control for ball mill circuits
26.06.2024 |
777.98 KB |
English
ECS/ProcessExpert Advanced process control for kilns and coolers
26.06.2024 |
3.56 MB |
English
ECS/ProcessExpert Advanced process control for vertical roller mills
26.06.2024 |
1.54 MB |
English
ECS/ProcessExpert Solution - Advanced process control
14.11.2024 |
600.77 KB |
English
Success with ECS/ProcessExpert
News and stories about ECS/ProcessExpert® advanced process control software
Recent posts