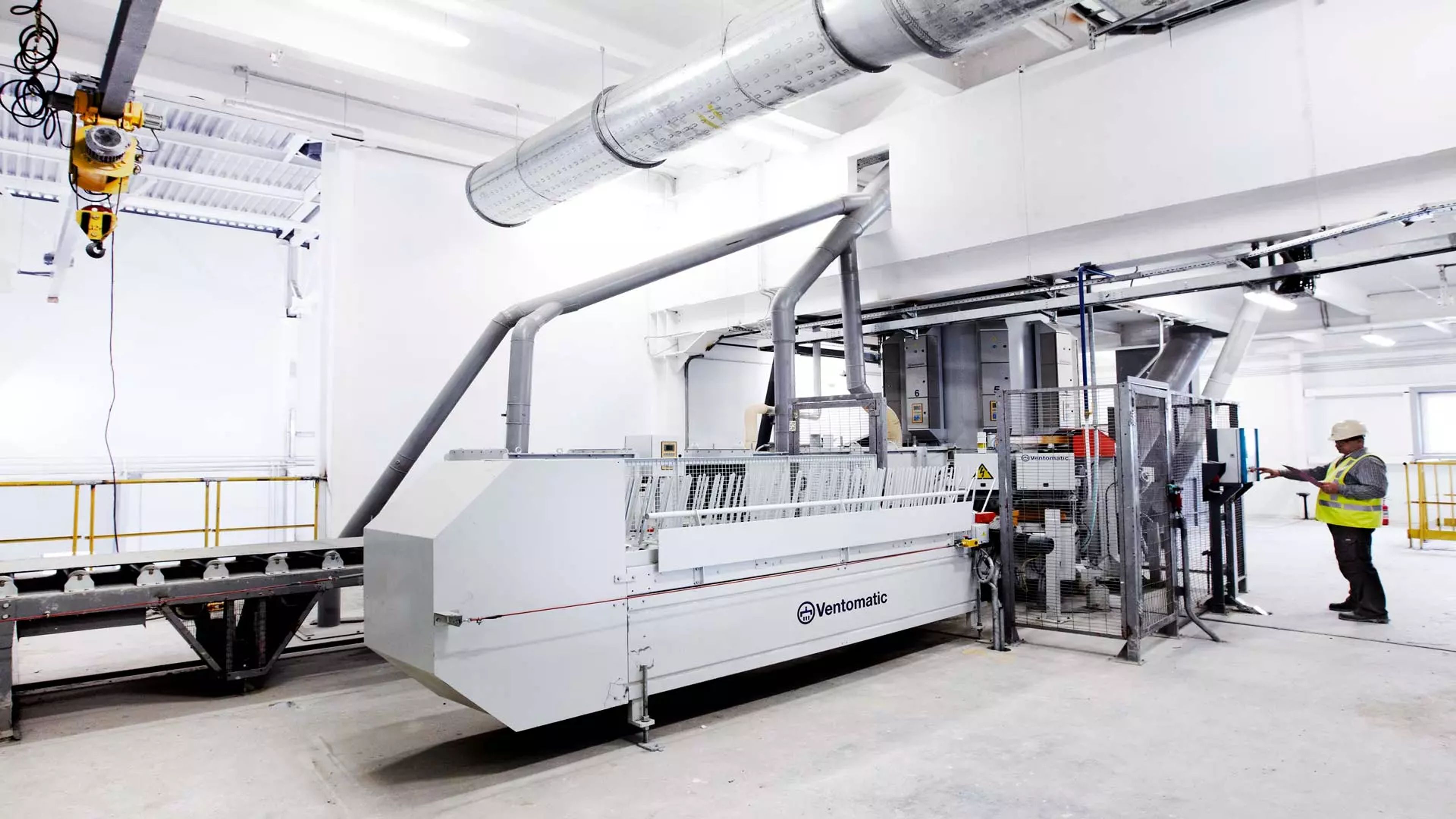
Maintain high efficiency of packing and dispatch lines
What we offer
Reliable VENTOMATIC® services for maintenance, spare parts, and support
Successfully getting your product ready for delivery is essential to a well-functioning production cycle. We will make sure your equipment is efficiently installed and commissioned, and then we’ll take care of maintenance, on-the-job training, and help you troubleshoot any issues. Keeping your packing and dispatch equipment in excellent condition for productivity, we offer: Expert field-service visits Programmed maintenance services and audits Online technical support Fast spare-parts supply for programmed maintenance and for emergencies Equipment modernising and enhancement
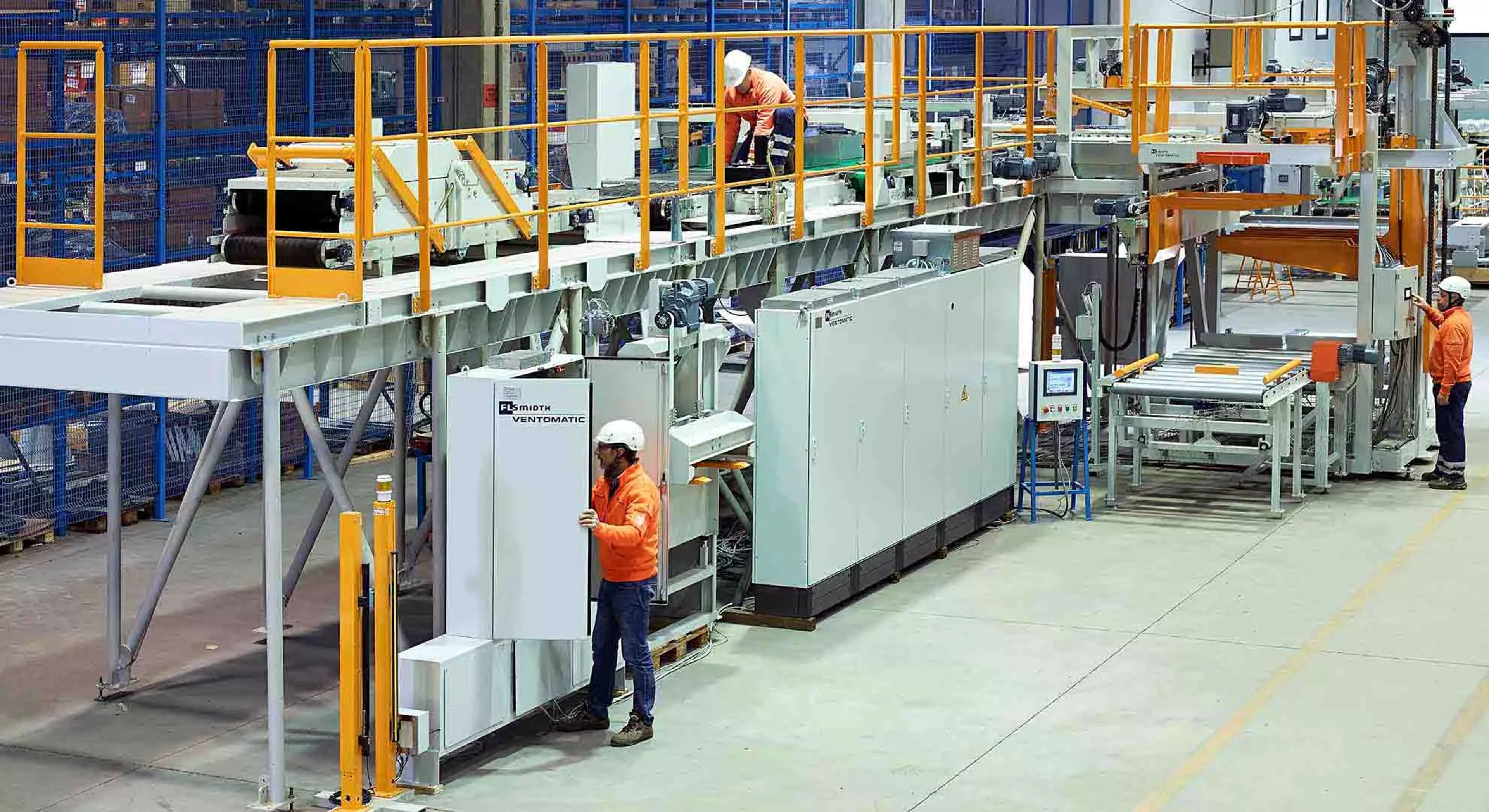
Maintenance site visit
A maintenance site visit is the ideal way to help you solve emergencies, tackle repairs and to do troubleshooting. This visit includes preventative maintenance, calibrations, mechanical fine-tuning, and an optimisation of process parameters. Usually, a mechanical site visit is a single intervention, open-book agreement (payment according to fees for supervisory personnel).
Service agreement
A service agreement helps you achieve maximum plant uptime and provides valuable preventative maintenance support to avoid unplanned shutdowns. The result is a stable production yield at the optimal level. Each service agreement contract is individually customised to meet your needs in terms of inspection, maintenance, and training. Usually, a service agreement contract includes a minimum of two visits per year (payment is via a Lump Sum).
Training
FLSmidth VENTOMATIC offers you dedicated, tailor-made training to improve the skills of your staff and the performance and reliability of your installed equipment. The training can be held either onsite at your plant or at our VENTOMATIC facility in Italy.
Secure parts you can trust
Get assistance with both existing and new equipment. We’ll visit you to audit your equipment, to ensure you have the correct spare-part stock and programmed maintenance. We can consult with you and offer relevant potential upgrades of your machinery in order to optimise the efficiency and productivity of your complete installation.
Get in touch with our specialists
Online technical support
Please send an email to service@flsmidthventomatic.com with the following required information: Your contact details (name, surname, company name, phone or mobile numbers). Your VENTOMATIC® Project job number (K number). Description of the issue description.
OEE service proposal
Please send an email to oee-italy@flsmidthventomatic.com with the following required information: Your contact details (name, surname, company name, phone or mobile numbers). Your VENTOMATIC Project job number (K number). The service required (see the following list): Audit Site Visit Maintenance Site Visit Service Agreement Recommended Spare-Parts List Upgrade Service Consulting Training Technical Seminar
Spare-parts quotation
Please send an email to spareparts@flsmidthventomatic.com with the following required information: Your contact details (name, surname, company name, phone or mobile numbers). Your VENTOMATIC Project job number (K number).