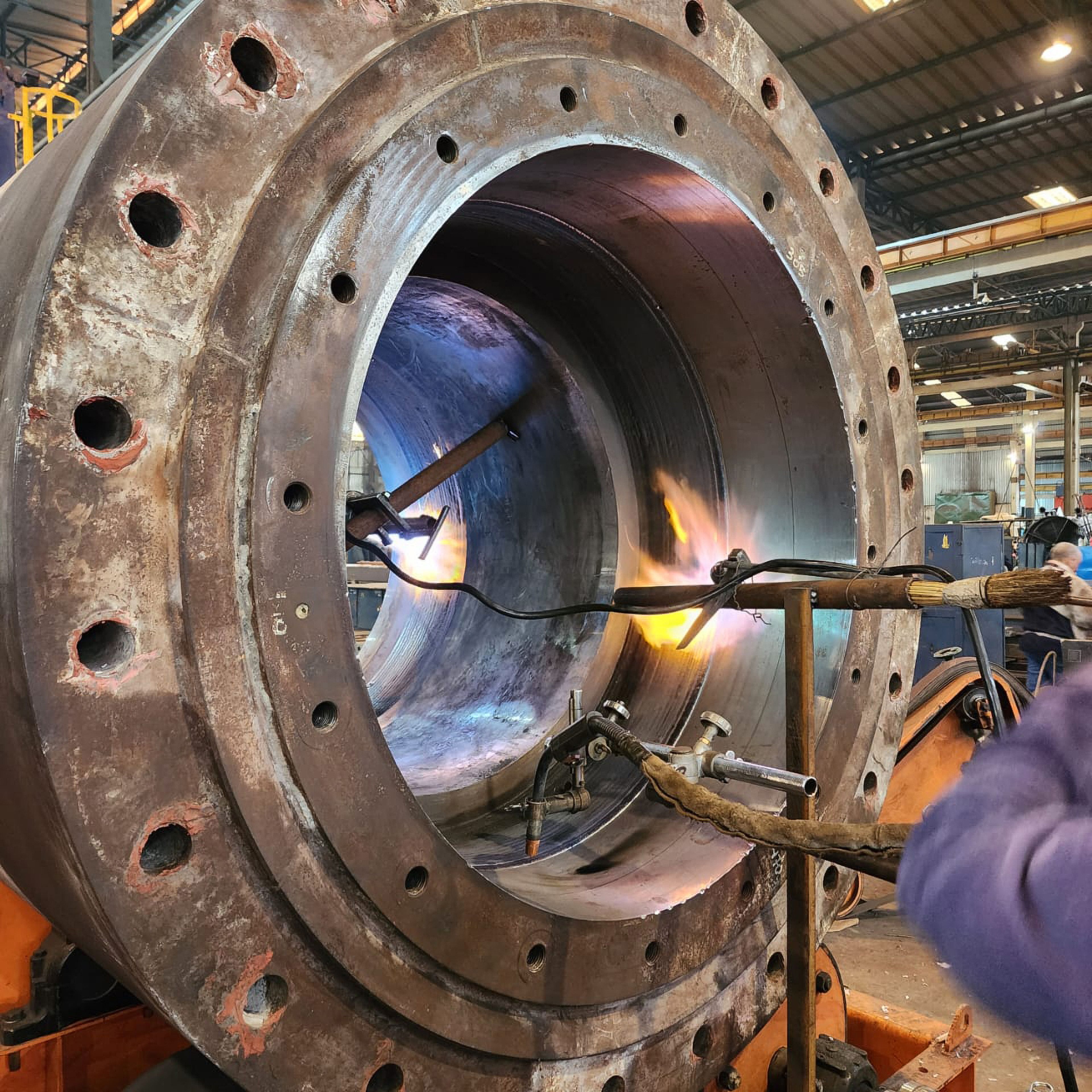
Restore your rollers to the original design condition with an OEM-approved rebuild service
Key benefits
Reduce operational costs
Rebuilding with an OEM-approved workshop enables you to maintain a consistently high-performance level in your OK™ Mill and ATOX® Mill. Plus, with a longer service life, the cost of maintenance is reduced.
Extend equipment life
By only using workshops that have access to our engineering support and technical drawings/procedures, you ensure your roller will be returned to you in as-new condition, with machining completed to the original parameters. With optimal operating conditions, this should give you a service life of 24 – 36 months with each rebuild.
Minimise downtime
A roller refurbished to OEM standards will deliver higher availability and reduced downtime. A proactive maintenance approach ensures fewer stoppages for repairs, and a rebuild plan that works with your schedule.
OEM-approved providers
All our providers have been vetted to ensure the rebuilds are of the highest quality. Nothing passes the gates that we wouldn’t be happy to send out ourselves.
What we offer
How it works
To ensure maximum rebuild quality, we’ve implemented a two-stage process for all roller rebuilds. 1. We take receipt of your worn roller and our engineers conduct a comprehensive inspection to discover exactly what’s required to bring it back to as-new condition. We’ll report back to you and let you know if new parts are required and what the total cost of the service will be. 2. Our workshops carry out the necessary work to rebuild the roller. All our providers are OEM-approved. They are equipped with our engineering support and the technical drawings/procedures to ensure the roller is rebuilt to the precise tolerances of the original component.

The OEM difference
Many workshops provide a rebuild service, but very few have the capability to carry out the work to our exacting OEM standards. By personally approving each supplier and equipping them with our engineering support and the technical drawings/procedures, we ensure your roller can be restored to its original design specifications, ready to return to service.
A proactive maintenance approach
Proactive roller rebuilds ensure you’re never at the mercy of a roller breakdown again. If you keep spare rollers on site, you can schedule roller rebuilds to coincide with existing shutdowns and continue operation with the spare roller while the worn one is rebuilt.
Long-term agreements and exchanges available
If you’re looking for long-term improvements in availability and machine life, talk to us about a long-term service agreement for roller rebuilds, or an exchange agreement whereby we buy back your worn roller for credit against a refurbished and ready-to-use roller.
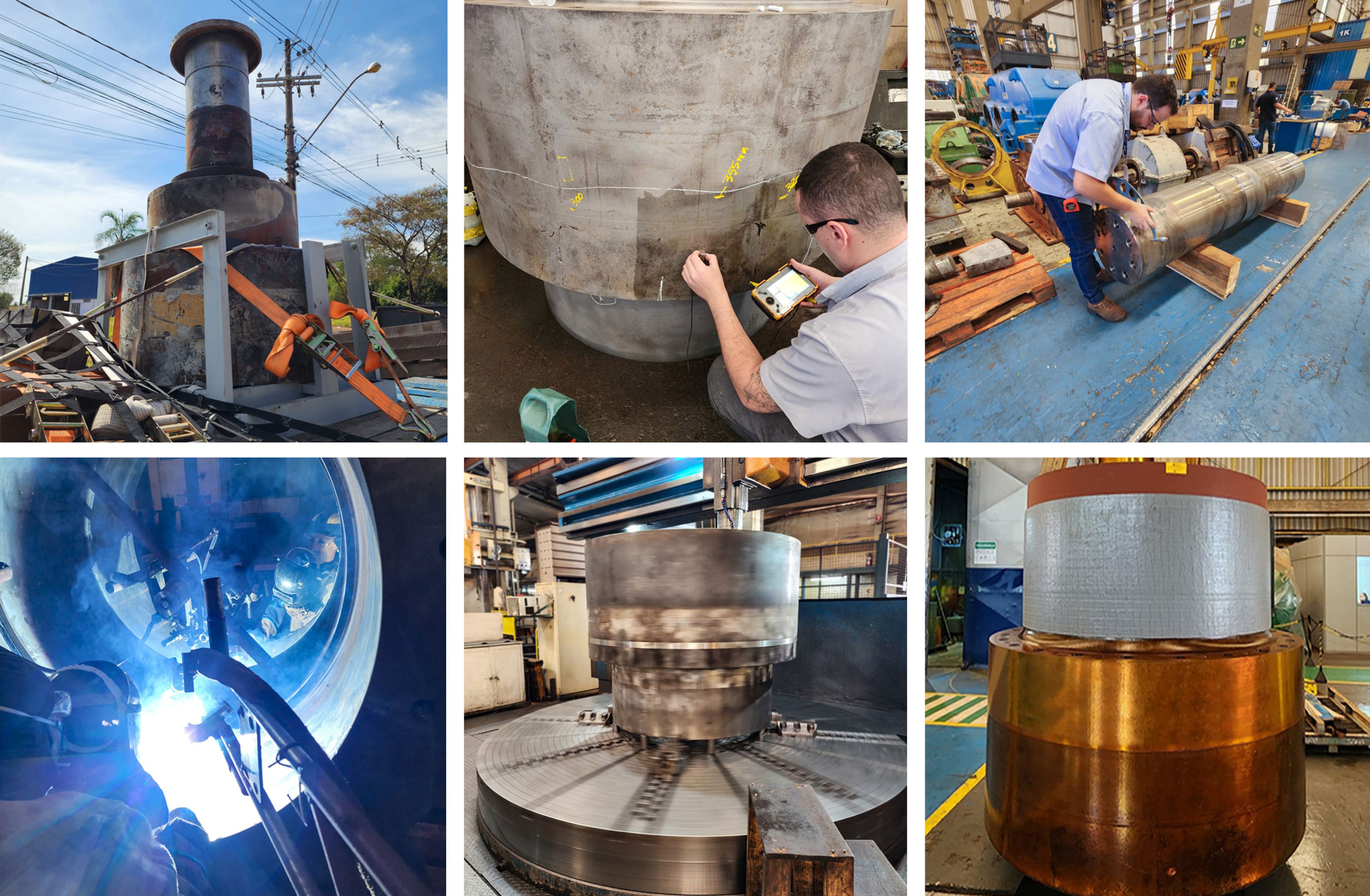