First In – First Out. Let’s keep your materials moving
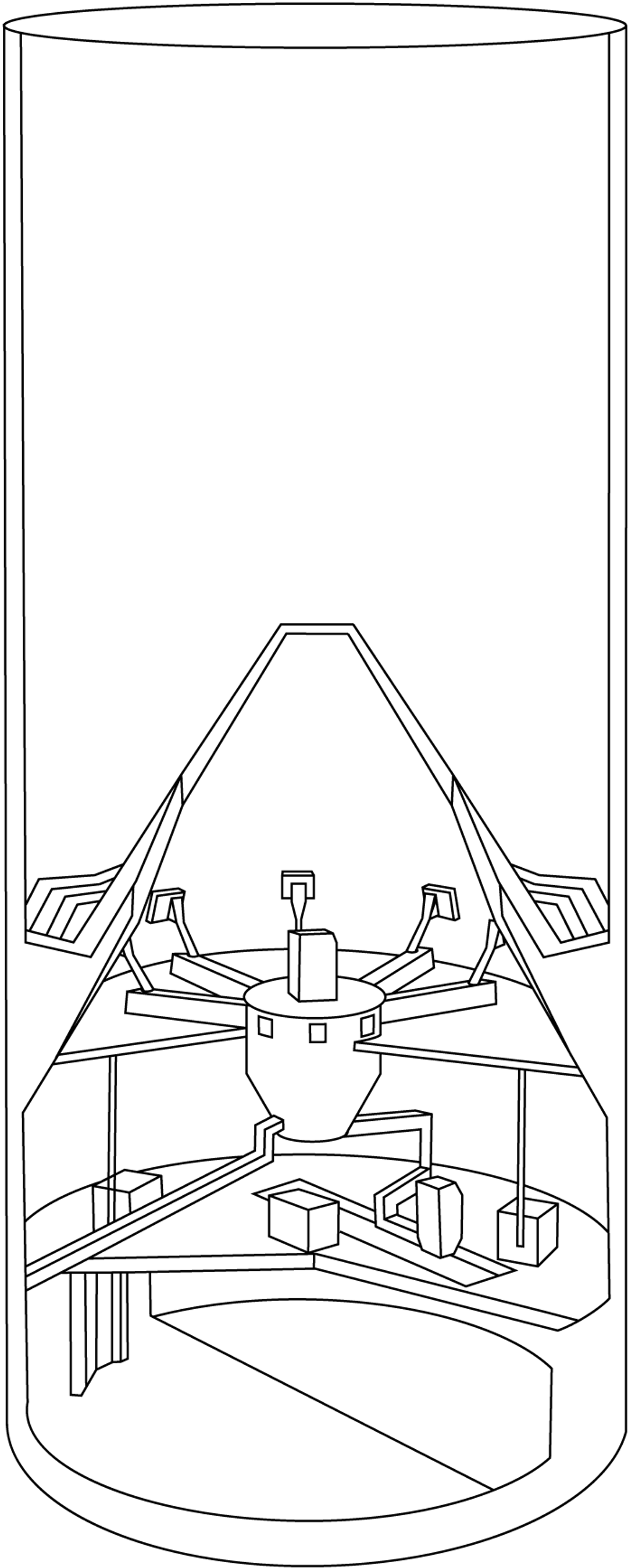
What we offer
Energy-efficient blending, storage and reclaim
You have a lot of choices for your blending silos and storage . Each has different strengths and characteristics, allowing you to choose the best fit for your application. And you can be sure that whatever you choose will be low-dust, high-efficiency and long-life.

Storage solutions to keep your process moving
Whatever material you’re storing and however it fits in to your process, efficient and complete reclaim is always a priority. It impacts productivity and profitability – not to mention safety. Problems retrieving material from storage can be a major bottleneck to your operation. This is why we have prioritized First In – First Out in all our silo designs. By keeping material moving using controlled flow technology, your materials are held safe in storage and easily reclaimed. With First In – First Out built in as standard, you can choose from our range of silo technologies in accordance with your needs.
Pneumatic blending silos for virtually any application
Pneumatic blending technology maximises the benefits of fluidisation and gravity to achieve complete blending with low power consumption. Our range of pneumatic blending silos caters for high capacity, low pressure and low dust applications in bulk materials industries.
Complete reclaim. Smart design. Low maintenance
Safe, efficient discharge
Whichever silo you choose, easy discharge remains a priority. And it’s our priority too, which is why we’ve worked hard to perfect our aeration and reclaim technology. First In – First Out is our philosophy. When product gets stuck in the silo, you have to get it out – and ultimately that can mean sending in personnel to clean up. A risky procedure best avoided at all costs. By ensuring that product is continually in motion, bridging, lumping and compaction are prevented. The silo technology and related controls do all the work for you, so your personnel aren’t in danger – and you get your materials out safely.
Flexible storage options for a range of materials
Whether you are searching for a blending silo that can deliver a more stable kiln feed, seeking a more effective means of storing and reclaiming cement, or looking to minimize the storage footprint for your range of finished products, we have the silo for you. Talk to our experts about your precise needs.
Complete reclaim
We engineer all our storage silos to maximize the benefits of fluidization while minimizing power consumption. Our Ful-Floor™ reclaim systems for dome silos use our industry-proven Airslide® fabric anchored to nearly 100% of the floor area. Embedded aeration troughs and piping eliminate restrictions that can inhibit material flow. The result? Complete reclaim of your stored material with minimal floor slope, low average power and low maintenance.
Low maintenance
Our blending and storage silos are designed with very minimal moving parts so maintenance requirements are low.
Low energy costs
Fluidizing air keeps your material moving, but we all know that the use of compressed air can be a major expense. To keep costs low, we use minimal fluidizing air and only aerate one or two sections at a time. This also brings down your maintenance requirements.
Easier raw meal cement processing with the Controlled Flow silo
Increasing productivity and efficiency to meet your demands
Your productivity relies on a process that handles product flow capably, reliably and efficiently. The Controlled Flow silo provides optimal flow, homogenising efficiency and significant power reduction at low investment cost. It operates continuously and is built to blend, homogenise and store cement raw meal.
Dependable kiln feed systems
Our kiln feed systems have proven short- and long-term accuracy and deliver outstanding reliability in hundreds of installations. We offer two solutions for kiln feed systems: FLS Low (loss of weight) This arrangement uses signals from the load cells to start and stop the process, maintaining pre-set material level limits. The kiln free flow rate is controlled by measuring the extraction rate of kiln feed by units determined by loss in tank weight per time unit while no raw meal is entering the silo. The position of the flow gate is then adjusted to maintain the pre-set rate while the kiln is filling. Pfister® FRW The special design of this rotor weigh feeder is ideal for continuous dosing powdered bulk materials with high dosing uniformity and precision. The integration of weighing and dosing makes the Pfister® FRW easy to operate and extremely reliable, with negligible wear. High feed ranges and feed rates up to 1000 t/h can be achieved. Programmable controls let you determine your flow rate distribution, as well as enabling you to fix the feed sequence, valve operation and aeration of the segments. The program starts and stops based on feed tank level. The Controlled Flow silo’s control panel is programmable through the kiln feed system and vice versa.
Additional design features
A single rotary blower aerates the kiln feed tank and operates at up to 0.8 bar of pressure. For storage silos, the optimised low-height tank operates at up to 0.4 bar of pressure. The bottom of the feed tank has one or more electrically or pneumatically-regulated gates that control flow – allowing you to regulate the flowrate. The rotary blowers have noise-reduced blow off pipes that release fluidization air out at the correct pressure level. The standard features of the silo top include manholes, sounding pipes, over- and under-pressure valves (also known as the pressure equivalizing valve), a level switch and level indicator, along with a de-dusting system.