Our vertical roller mill offers optimum raw, cement and slag grinding
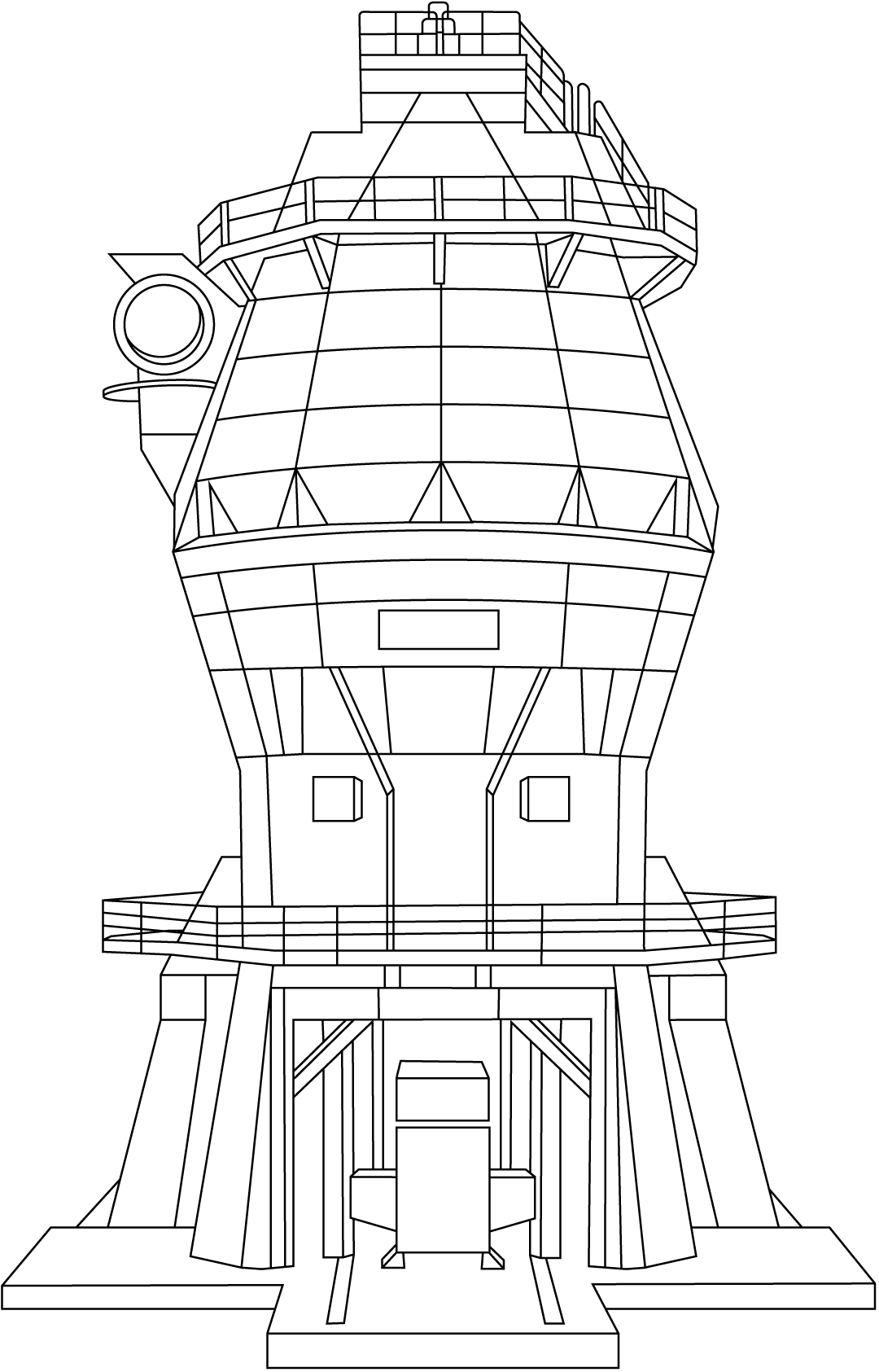_Raw_and_Cement_Mill.png?w=1080&q=80&auto=format)
What we offer
Vertical roller mill with peak raw, cement and slag grinding performance
Our cost-saving Vertical Roller Mill (VRM) exhibits a modern design approach. We continuously improve our solution with the latest updates to enhance grinding performance and overall productivity. The success of the OK™ Mill highlights the reliability of its technology and a contribution to the cement industry amidst rapidly emerging trends of greater variation in feed materials and larger production capacity. Our OK Mill grinding solution skilfully comminutes raw material, cement and slag. You can easily adjust it to grind any feed material and produce multiple cement types in the same mill. Due to its highly effective drying performance, the OK Mill is the natural choice for grinding blended cements with one or more wet components. A design for optimal efficiency ensures your operating costs are minimised while profitability is maximised.
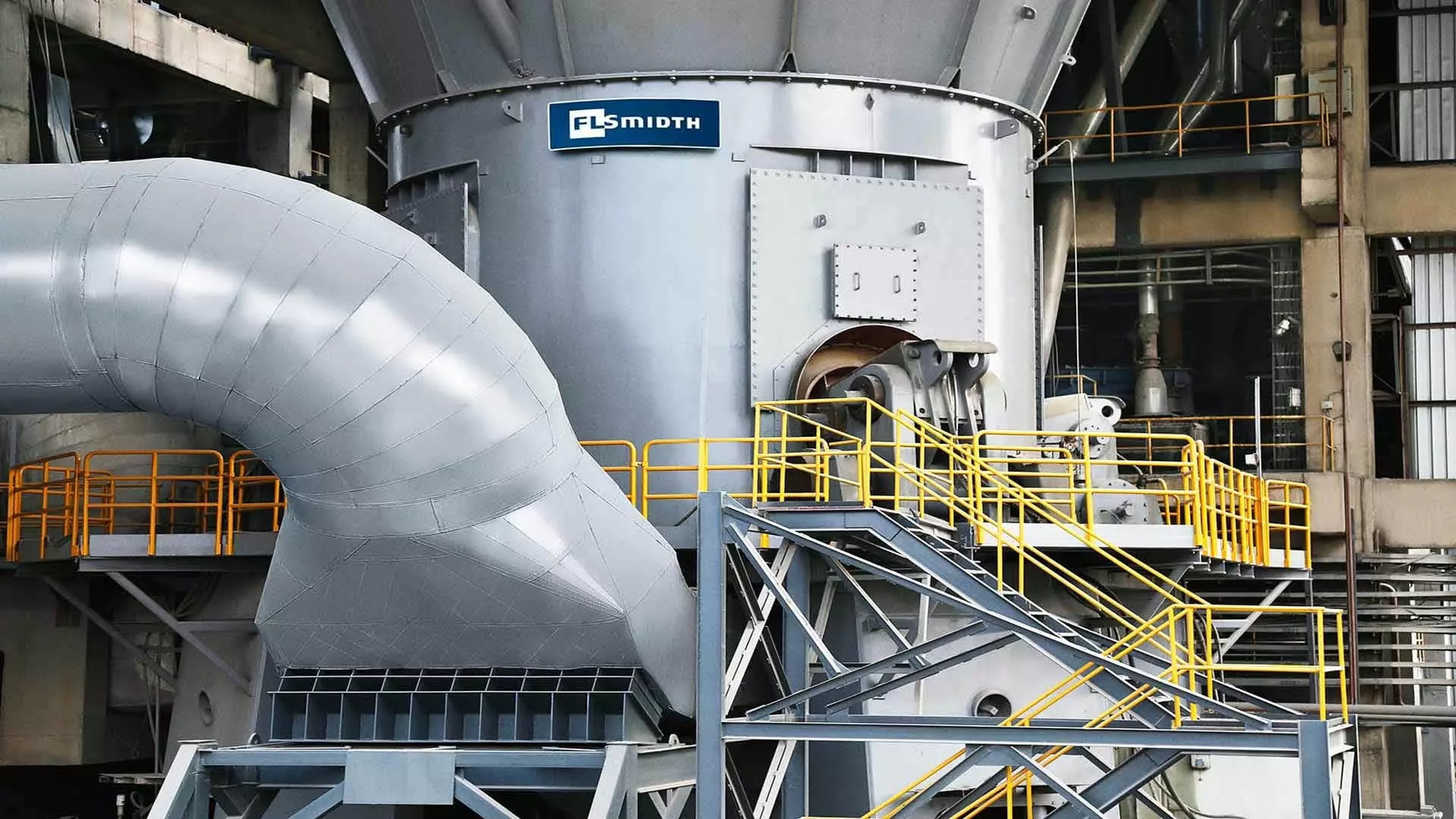
Impressive energy savings in operations
Our OK Mill with its patented roller and table design delivers the best power efficiency of any cement vertical roller mill. It uses five to ten percent less power than other vertical roller mills. In addition to efficiency, the unique design also makes the vertical roller mill more stable in operation than other vertical roller mills, offering higher availability and the capability to grind the finest products and highest Blaine cement.
Intelligent design simplifies operations and maintenance
With a modular design, the OK Mill offers the best possibility for low long-term total cost of ownership (TCO) and minimal spare parts net working capital. Parts commonality leads to greater flexibility in sharing spare parts across vertical roller mills, regardless of size and application. It also simplifies spare parts inventory, saving you costs and improving parts delivery times.
The segmented wear parts can be maintained inside the mill or if needed, the rollers can be removed from the mill using the swing out feature for external maintenance. The roller wear parts are made of the toughest material that is suitable for repeated hard-facing.
Compact layout makes installation hassle free
The OK Mill combines the drying, grinding, material conveying and separation processes into one compact unit, requiring fewer machines in the mill circuit and therefore, simplifying plant layout. Concrete mill stands replace the traditional steel structures, reducing installation time and costs. Using concrete also means lower mill vibration at the foundation.
The high-performing vertical roller mill generates minimal noise during operation due to the lower level of mill vibration. This makes installation without a building feasible. This substantially reduces civil construction costs and improves the working environment for your plant employees.
Reliable vertical roller mill for easy grinding of raw, cement and slag
The OK™ Mill was originally designed for cement grinding. In 2017 we released the OK™ vertical roller mill for raw materials grinding. The OK™ Mill’s modular design comes with unique flexibility, showcasing parts commonality, where spare parts can be shared between vertical roller mills regardless of size and application. Equipment longevity is assured with durable wear protection on all internal surfaces. The main difference between cement and raw OK™ Mills lies in the roller grinding profiles, with the raw mill rollers bearing a spherical shape that is more suitable for grinding cement raw materials.
downloads
Brochures
First-time service agreements for OK® Mill and key OK Mill components
17.05.2024 |
1.01 MB |
English