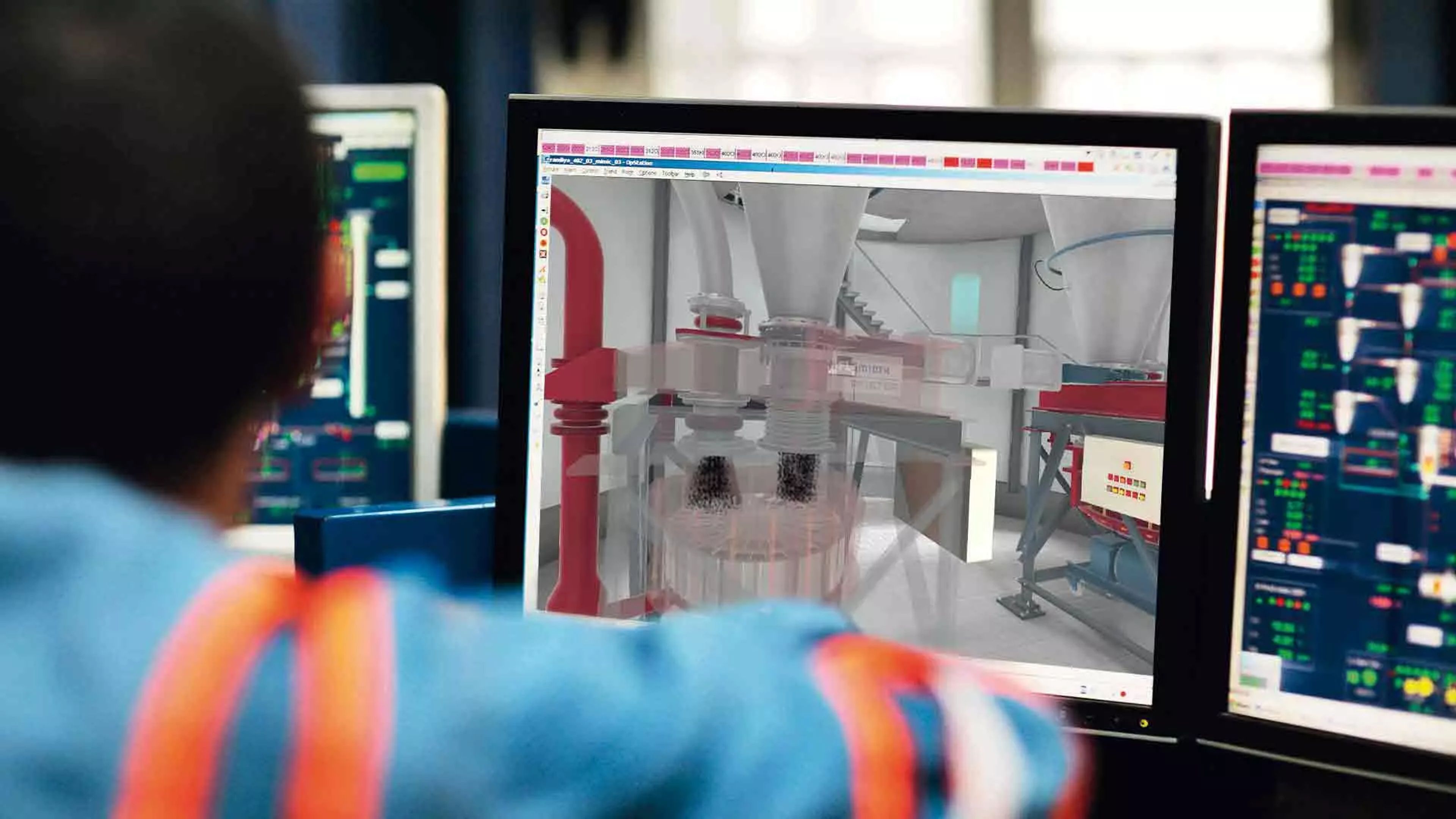
Prevent damage to your dosing system and save costs
What we offer
PFISTER® Feeding and Dosing Technology support specialists
Reduce the risk of unplanned downtime with our support services. From spare part management to system calibration and everything in between, our experts are at your disposal for proactive maintenance planning and responsive troubleshooting and support. Together, we can increase the life of your machine and reduced service and operation costs.
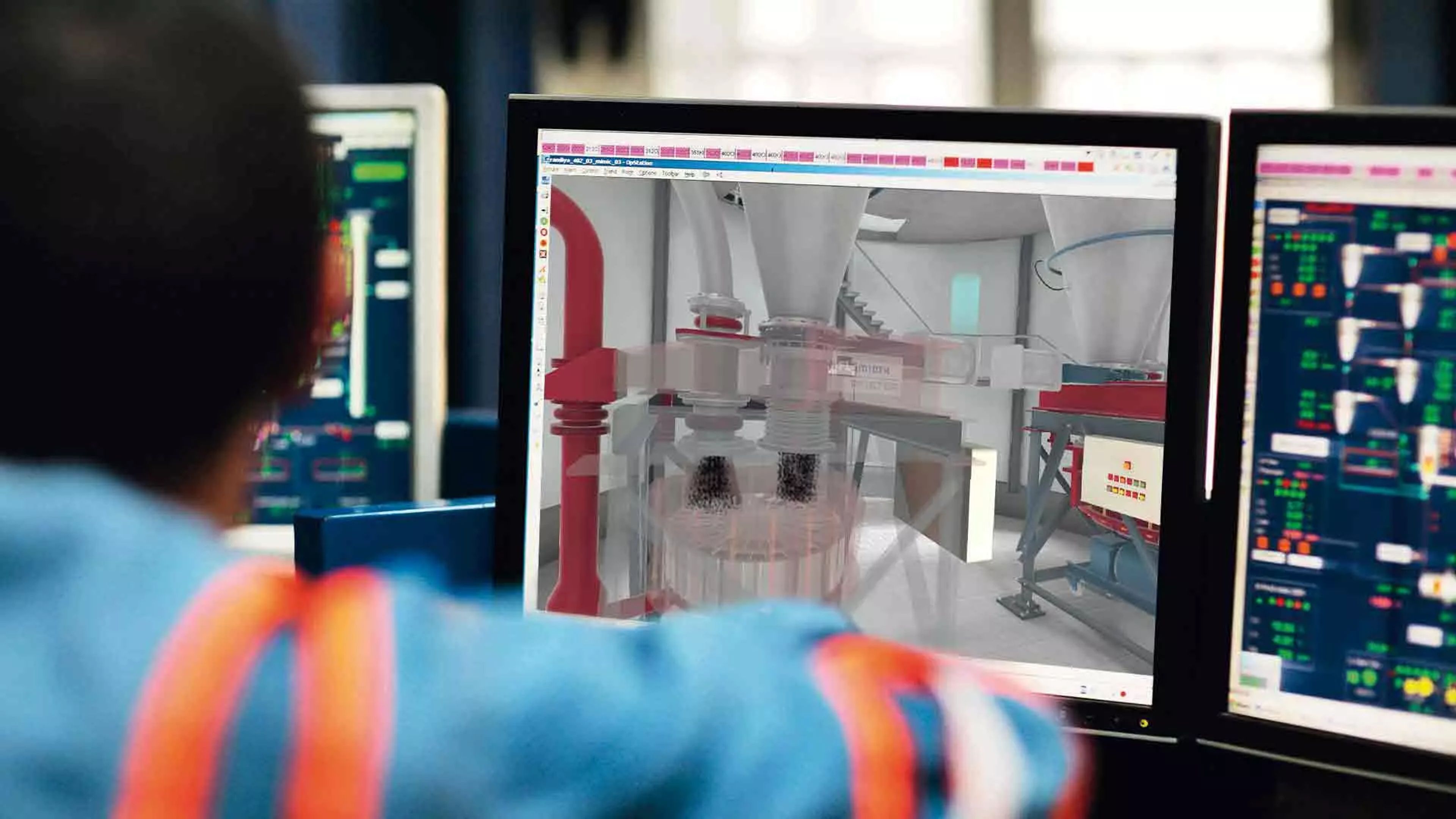
Spare part management to system calibration and everything in between
Our feeding and dosing equipment services include remote service agreements, annual service visits, feeder condition reports, software update, exchange of wear spare parts, calibration of the system, spare part recommendation and software/data back-up.
Prompt, timely support
Our Remote Service Agreement ensures you have expertise on hand when you need it. Our support specialists can be with you by phone, video call, email, or however suits you best.
Expertise at your fingertips
With 140 years’ service in the cement industry, our history speaks for itself. Today, we have a global network of feeding and dosing specialists, ready to help you wherever you are.
Reduced downtime
Responsive and timely support helps minimise downtime and reduce the cost of downtime, so that you can get back to productivity as quickly as possible.
Lower maintenance costs
Proactive and responsive maintenance help to reduce the impact of part failure or address it before it can affect production. As a result, you’ll experience lower maintenance costs.
Remote support – whenever, wherever
Advances in digital technologies enable us to help close this skills gap by providing expert support whenever and wherever you need it. Our support specialists can access your feeder – via existing hardware for newer machines, or with a simple upgrade for older models – to evaluate and diagnose issues. We then use the feeder’s unique data to identify the likely source of the problem and our expertise as OEM and experienced support specialists and field engineers to guide you towards the solution.
Remote support avoids the need to wait for an onsite visit. The service agreement also provides you with the reassurance that should something go wrong, you won’t be left to deal with it alone. Our experts are available 24/7, wherever you are in the world.
Remote support agreements are priced per feeder, with discounts available on an annual subscription for multiple feeders. We support Pfister DRW, TRW, FRW, SCF and SLF models. If your Pfister feeder does not have the necessary hardware, we can upgrade your feeder with a remote upgrade package for your CSC or FDC controllers.
Annual service visits
In addition to the remote support contract, we also offer an optional annual shutdown visit. This agreement ensures a Pfister service engineer will be with you in person during your shutdown. Prior to the site visit, we will conduct a remote evaluation of the condition of your feeders so that we can make the most of the service visit. Then, during your shutdown, we’ll perform a full inspection and evaluation of your critical components and system integrity and advise of any maintenance needs. While onsite, we can also provide refresher training for your team to optimise operations and maintenance.
Onsite support during a shutdown is a great opportunity to get expert oversight of your equipment, ensuring its ongoing reliability and performance for the year ahead.
Feeder condition reports
Our remote service agreement is a responsive service offer, available to you whenever your Pfister feeding and dosing systems experience an issue. But if you would like a more proactive picture of the overall condition of your equipment, we can provide quarterly reports detailing feeder performance and highlighting any areas of concern that could develop into future outages. This will help with maintenance planning and may even help prevent downtime by enabling you to act before a problem occurs.
Feeder condition reports are an additional service not included with the remote support package. With the connection in place for remote support, the data is available to our experts for analysis and no additional hardware is required.
24-hour hotline
We offer a 24-hour hotline and online troubleshooting, providing worldwide support when you need it. We have local service units in India, China, Asia, North and South America, Europe and the Middle East.
Tel +49 821 7949 241
Email: service@flsmidthpfister.com
Spare and wear parts
In a rough industrial environment, it’s impossible to completely prevent wear. This is particularly true for the wear parts of your dosing system, such as the rotor wheels and sealing plates.
To ensure that you are not waiting around for a crucial spare part, we keep a large number of spare parts in stock. Our skilled spares specialists can also help you optimise your spare-parts management.
Email : spares@flsmidthpfister.com
Flexible service contracts and training
We offer flexible service contracts, which can be tailored to meet your exact requirements. And, to ensure the best possible knowledge sharing, we can offer specialist training at FLSmidth Pfister’s training centre or at your production site.
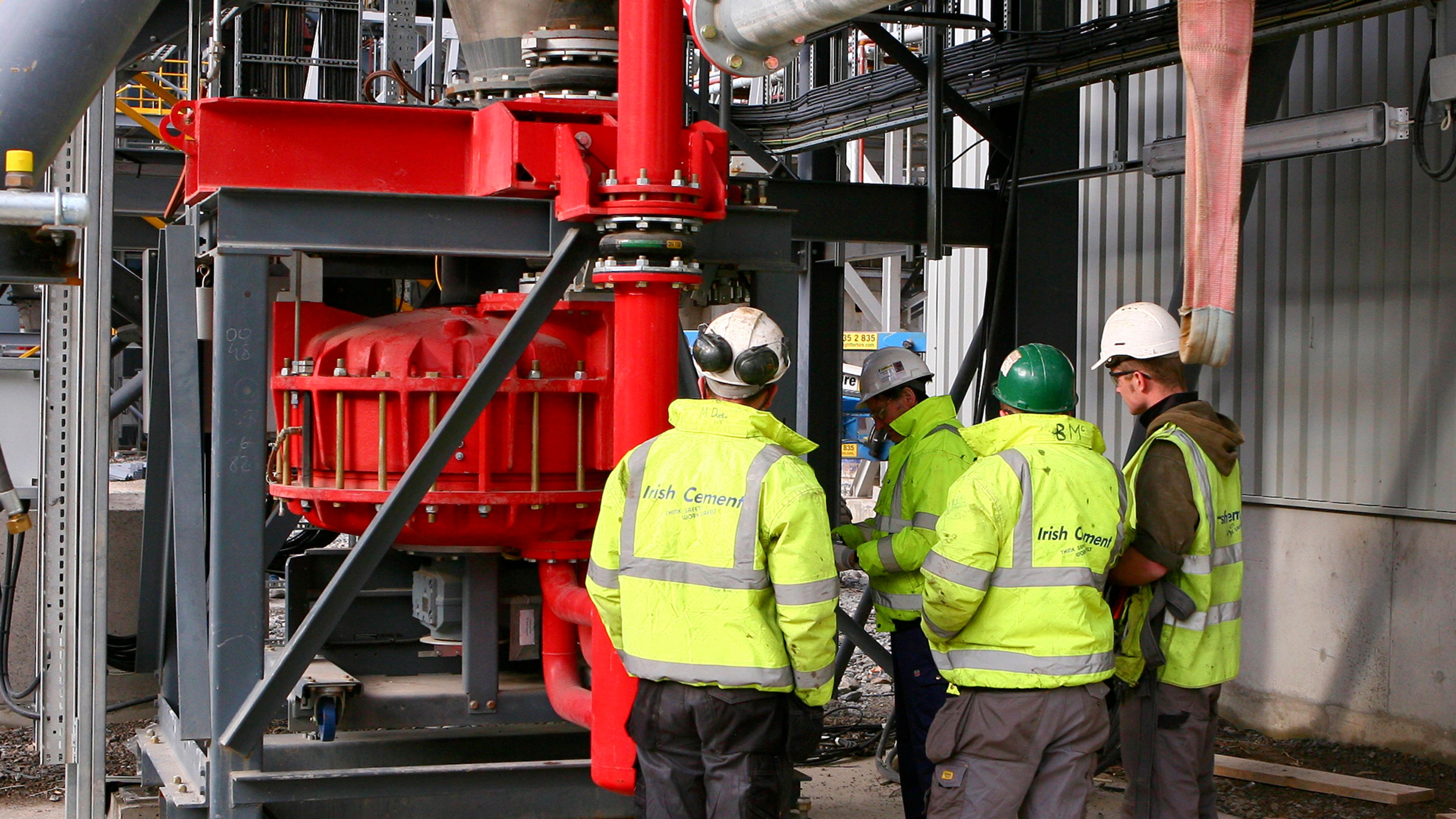
downloads
Brochures
FEEDflex - upgrade for Pfister DRW - customer testimonial
11.11.2024 |
217.85 KB |
English