Long-lasting wear solution tailored to the demands of our OK™ mills
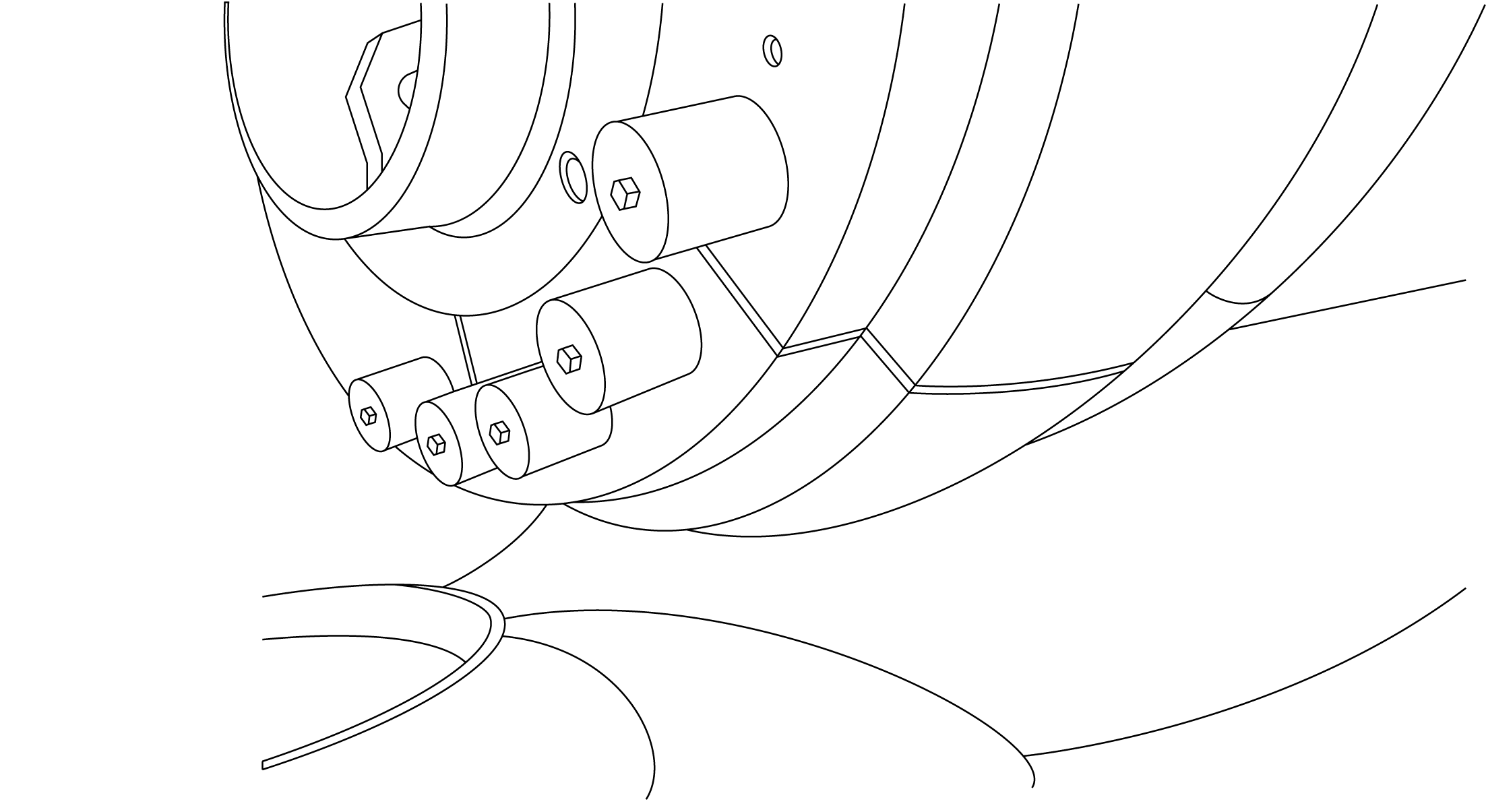ProCeramic_Wear_Segments.png?w=1080&q=80&auto=format)
What we offer
A best-in-class mill deserves a tailored wear solution
The common maintenance practice for worn VRM roller and table wear liners is to reweld or hard face the worn surface. This means regular stops to mill operation. But because the wear rate in a VRM varies, depending on feed materials and product fineness, the number of times maintenance is required over a given time period is variable. With up to 3 times the wear life of traditional high-chrome liners, OK™ Pro+ ceramic wear segments reduce the number of maintenance stops, offering a long-lasting wear solution for our OK™ raw, cement and slag mills. And because they are designed by us for our mills, they’re guaranteed to ensure mill performance stays at the high level you expect it. They also bring sustainability advantages compared to third-party wear liners, which may not fit as well or be made from inferior materials. By ensuring mill performance remains at optimum levels, grinding efficiency is maintained and energy consumption is optimised. There is also less consumption of wear parts (because the OK™ Pro+ liners last longer) and they can be recyclable at end-of-life, minimising waste.
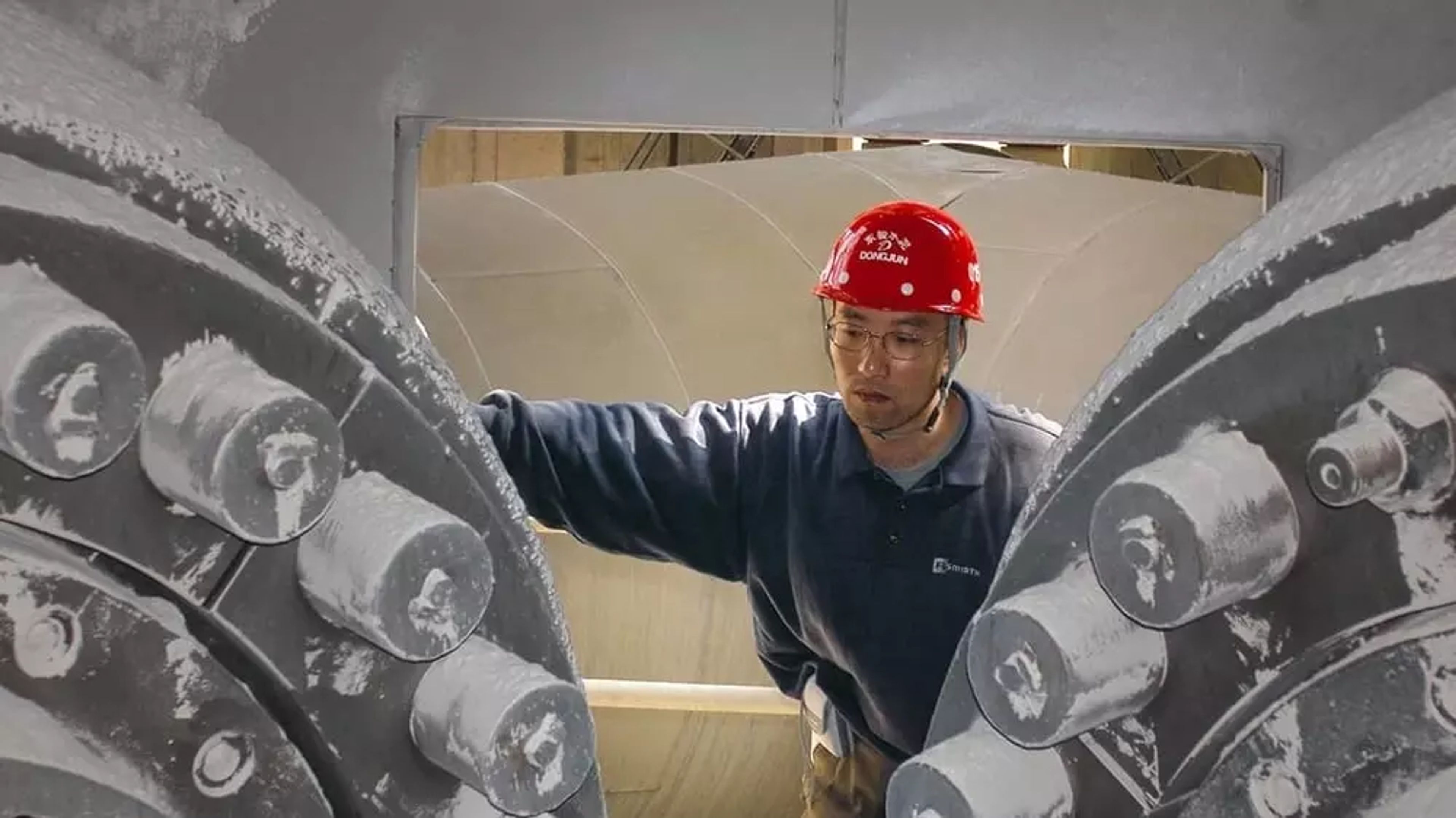
A wear solution that helps get the most out of your mill
Improve mill productivity with fewer maintenance stops
Guarantee mill performance with an expert OEM-made solution
Reduce wear liner consumption with highest-quality materials
Low-waste option as recyclable at end of life
Related Offerings