article
Future-Proofing Cement Operations: Ramco Cement’s Seamless Automation Upgrade with ECS/ControlCenter™ 9
In today’s fast-evolving industrial landscape, legacy systems can become a bottleneck to efficiency and reliability. This was the case for Ramco Cement’s grinding unit at Mathodu, where aging automation technology posed increasing risks to productivity and operational continuity.
The Challenge: Upgrading an Outdated Control System
Ramco Cement was relying on their old control system that had served well over the years—but time had taken its toll. With parts becoming obsolete and support limited, the risk of unplanned downtime and operational disruption had grown too large to ignore.
The company needed a modern control system that could be deployed swiftly and with minimal interruption to operations. Key requirements included improved process visibility, enhanced fault diagnostics, and comprehensive reporting—all without extending the scheduled shutdown window.
The Solution: FLSmidth Cement’s ECS/ControlCenter 9
Following a detailed evaluation process, Ramco Cement chose FLSmidth Cement’s ECS/ControlCenter 9, a state-of-the-art automation platform designed specifically for the cement industry and backed by four decades of domain expertise.
ECS/ControlCenter v9 offered a familiar yet modern user experience through its HMI/SCADA interface, powered by ACESYS v8 Cement Library standards. The system was tailored to mimic the layout and workflows of the legacy setup—ensuring minimal learning curve for operators and enabling a seamless transition.
One standout feature was real-time process simulation, which allowed operators to undergo hands-on training before the actual switchover—reducing risk and building confidence.
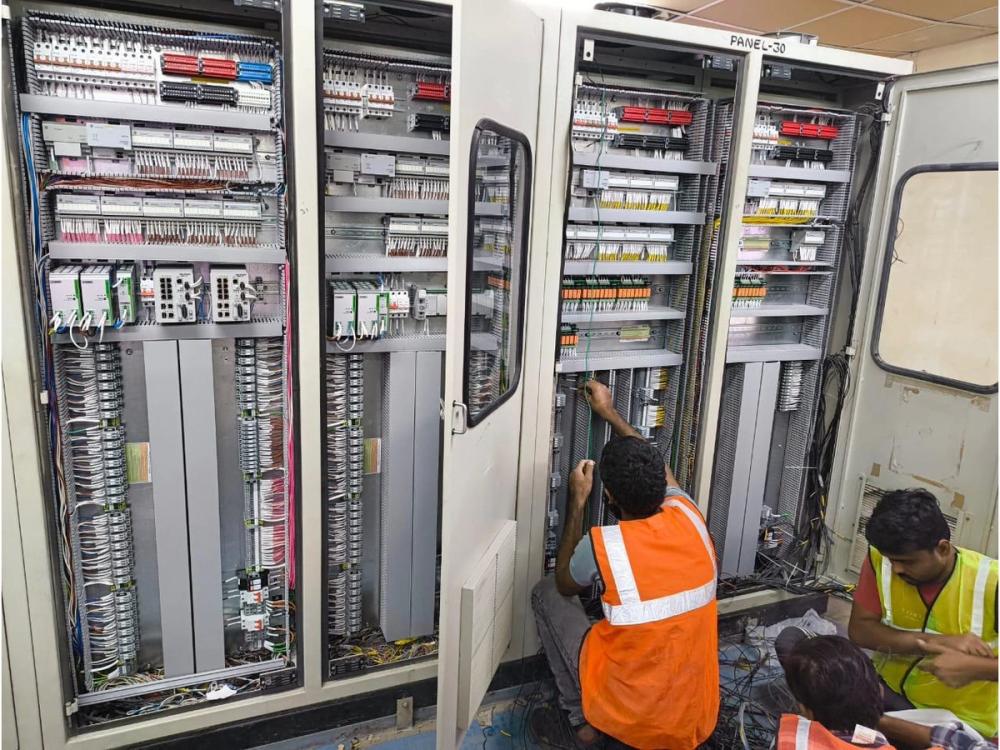
The Execution: Collaborative, Streamlined, and Risk-Free
The transition was executed in close collaboration between FLSmidth Cement and Ramco Cement. Using standardized engineering tools, the team developed consistent, high-quality PLC code, fully compatible with Rockwell PLC Hardware.
Old obsolete I/O panels were replaced entirely with modern Rockwell hardware, and ECS dual redundant servers were introduced to ensure robust, fail-safe operations and continuous data integrity.
Operator training, simulation-based commissioning, and rigorous testing enabled a smooth go-live—all within the planned shutdown period.
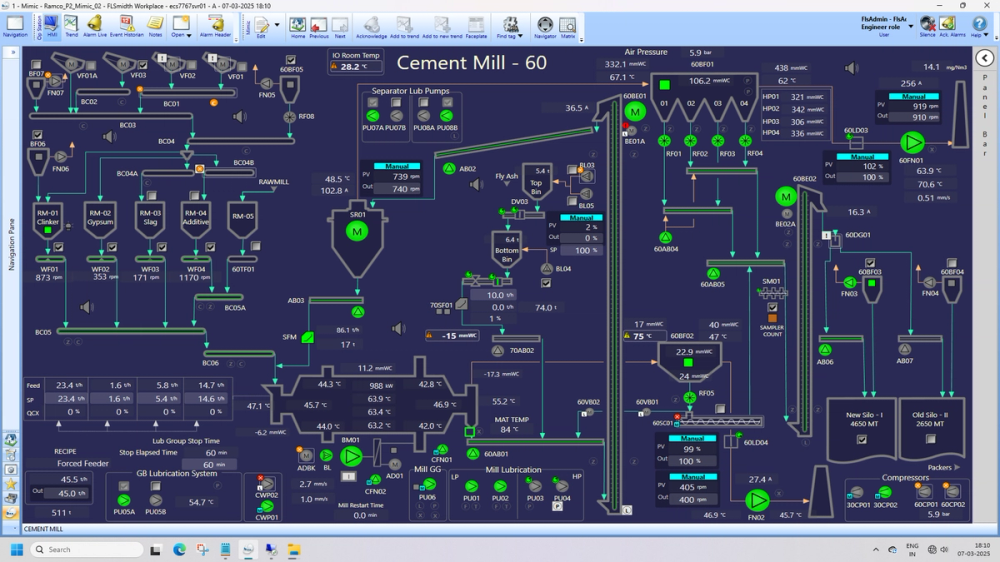
Ramco Cement
The Outcome: No Downtime, More Uptime
The results were immediate and impactful. The upgrade was completed on schedule with zero unplanned downtime. Ramco Cement now benefits from:
- Greater operational reliability
- Enhanced process control and visibility
- Reduced risk of system failure
- A scalable platform ready for future expansion
Why FLSmidth Cement?
From concept to commissioning, FLSmidth Cement provided complete project ownership—combining deep cement industry knowledge with robust engineering execution. Their commitment to tailored solutions, global service support, and proven track record made them the ideal automation partner.
With this strategic upgrade, Ramco Cement has future-proofed its grinding operations, setting a new benchmark for automation in the cement sector.