article
Industry 4.0 – Are we there yet?
The world is currently experiencing the fourth industrial revolution – or Industry 4.0. This is an era of digital transformation characterised by the introduction of AI and machine learning, connectivity (the Internet of Things or IoT), and big data – all of which are powered by cloud computing. To put it another way, there is much more computing power and much more storage. And, combined together, this is giving us data analytics at a whole new level. These are exciting times and we see examples in nearly all facets of our lives.
First published in World Cement magazine, April 2025
The pioneering cement producers who have integrated Industry 4.0 report remarkable benefits. Plants utilising smart sensors, IoT devices, and real-time data analytics have experienced up to a 20% increase in overall production efficiency, 15% reduction in energy consumption and a 10% decrease in raw material wastage [1]. The tangible benefits of AI-driven tools are many:
- Lower environmental impact – Greater efficiency reduces fuel and power use per tonne of cement while optimising clinker quality, enabling a reduced clinker factor.
- Enhanced quality – Real-time process adjustments optimise blending, fuel/raw material feeds, and pyro stability for more consistent output.
- Carbon capture readiness – Stabilised flue gas composition increases CO₂ concentration which simplifies carbon capture implementation – and makes it much more cost effective.
- Increased uptime – Continuous monitoring and stability reduce the frequency of issues and prevents minor issues from escalating into major failures.
It is hard to imagine any other investment having a more attractive ROI. You would assume virtually all plants would be embracing Industry 4.0 immediately and many are for applications regarding condition monitoring and proactive maintenance. But, from the perspective of process optimization, our industry is not quite there. That is the inspiration for this paper. This isn’t intended to be an in-depth technical piece, nor is this for the purpose to promote a specific offering. Rather, the objective is to explore why the cement industry seems to be struggling to implement the latest digital technologies at speed and what we can possibly do about it.
From Industry 3.0 to Industry 4.0 - the digital transformation of cement production
The latest estimates suggest that just 30% of cement plants worldwide have begun implementing Industry 4.0 technologies in various stages of the process [2]. That may sound somewhat respectable, 30% of plants. But that figure gives us no indication of how far the plants have actually progressed with implementation or even if the plant intends to rollout Industry 4.0 across the entire flow sheet rather than just isolated applications. So, what is going on here? Well, in short, it is not easy to move to 4.0 unless the plant has fully implemented 3.0 in a way that provides a solid foundation.
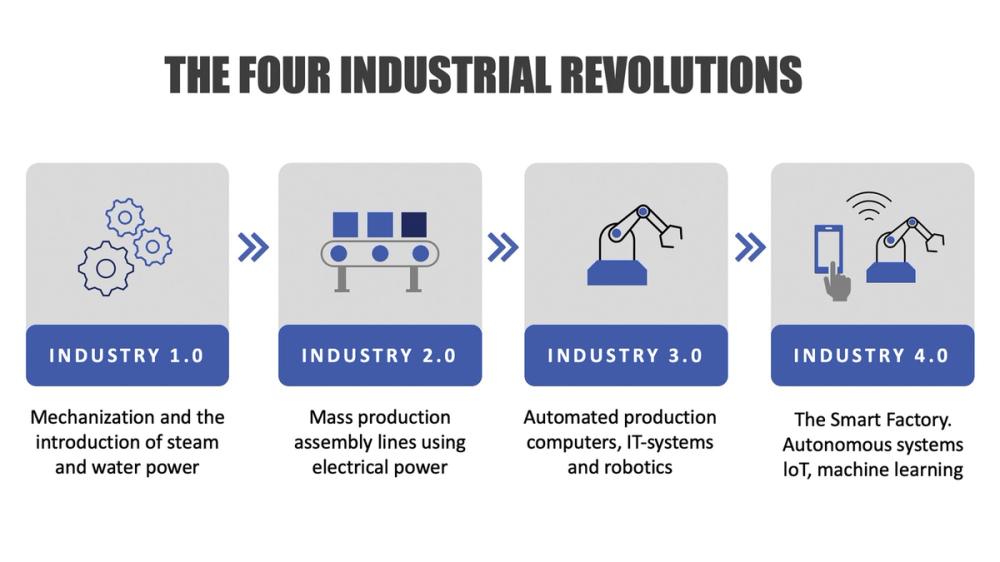
Let’s take a step back. Industry 3.0, also known as the digital revolution, initialised the automation and digitisation of manufacturing systems through solutions such as programmable logic controllers (PLCs). Process control focused on the automation of linear tasks, reducing manual intervention and increasing the precision and speed of processes, resulting in a marked improvement in process efficiency and an easier path to a high-quality end product.
The scope of the solutions was either specific applications such as the pyro process or perhaps even multiple applications at a site. But, with few exceptions, the solutions always stayed within the gates of the plant. Understandably, our industry was focused on squeezing out as much value as possible, as soon as possible and was largely successful. But, at the same time, much less effort was given to lay the groundwork necessary to support easy adoption of 4.0.
What are the barriers of implementing Industry 4.0 at scale?
Given the capabilities of the latest APC solutions, why is it that so many plants are lagging on the adoption of smart technologies?
- Lack of awareness – Some in leadership may not appreciate how important it is or have the full perspective of their plant’s situations.
- Change management – Embracing advanced process control software is a culture change for some operators. Without reinforcement such as periodic refresher training, there can be a risk of reverting to former practices.
- Trust – Between cybersecurity concerns and the range of new solutions on the market, there’s a lack of trust around which solution can deliver without risk.
- Immature technology – Though there is a lot of potential out there, real impact will only be achieved when APC solutions are mature enough and designed to be rapidly deployed from site to site, a capability many start-ups miss experience to deliver.
- Cost – The lack of technical maturity also makes it harder to calculate an accurate ROI as few benchmarks or past examples are available to support estimates for the actual opportunity costs and future benefits.
- Data isn’t usable at scale – There’s a lack of structured, high-resolution data –often missing crucial metadata (such as calibration details and process changes) – which is essential for training robust algorithm.
How do we progress to Industry 4.0 readiness?
First, plants as well as suppliers must deliberately put Industry 4.0 at the forefront of their automation strategies and make sure the proper foundation is in place. For example, at FLSmidth Cement, our R&D Roadmaps for each product are designed to capture the benefits of evolving AI solutions or other technologies. This includes the need to support the creation of usable data sets, mobility, and cloud computing so that AI solutions can be most effective.
Data that is usable at scale
Data quality and accessibility is the most prevalent and challenging obstacle that we see plants battle. Industry 4.0 solutions – especially AI-driven ones – require more than just sporadic historical records. A robust metadata foundation is essential, including calibration dates, process changes, and measurement precision. For some applications, having a time series of one year at a 10 second resolution is necessary. Without this level of detail, even well-collected data can be difficult for AI to interpret, limiting its ability to predict process behaviour and optimise operations.
To fully unlock AI’s potential, companies must strengthen their data foundations today. Start by auditing current automation systems (OT architecture) to identify gaps in data collection and metadata. Ensure sensors are calibrated for and control systems ready for continuous, high-resolution data capture. Standardised, centralised data storage simplifies AI analysis. (Good news if you have installed an FLSmidth ECS/ ControlCenter process control solution in the last 10 years: you already have one year of one-second-resolution data – a hidden advantage.)
Next, structure metadata management by documenting process changes, calibrations, and measurement precision. Break down departmental silos and integrate data across systems. Partner with experienced providers to build a scalable, future-proof architecture.
Sample data is an area of special concern as many plants still operate manual labs, but that data and the surrounding meta data is essential. The lack of such will severly strain your efforts for clinker substitution. A sampling and lab audit will reveal a clear view of data quality, accessibility, and consistency, and help identify gaps that could undermine AI-driven optimisation. By tackling these areas early, plants can establish a strong foundation for a smooth and effective digital transformation. This will enable full scale implementation of data driven AI Process optimization solution as they mature over the coming years.
Break free from vendor lock-in
In Industry 3.0, proprietary automation solutions were standard, and while not ideal, they were manageable. However, this lack of flexibility is causing frustration in today's digital landscape. Many plants now find themselves locked into vendor-specific systems that hinder integration, delay digital transformation, and drive-up costs. Companies struggle to adapt to new innovations and align with long-term operational goals without the freedom to evolve their technology stack.
It doesn't have to be this way. Supplier-agnostic pathways are available to offer an alternative to vendor lock-in. One such pathway is the Open Process Automation Standard (O-PAS) from The Open Group. O-PAS provides comprehensive guidance for developing Industry 4.0 automation systems that are independent of proprietary technologies. It enables seamless integration across diverse systems, giving companies the freedom to create cost-effective, scalable, and interoperable digital transformation roadmaps. Open standards have accelerated innovation outside of cement; we must also fully embrace this practice as an industry.
Industry 4.0 automation systems that are independent of proprietary technologies. It enables seamless integration across diverse systems, giving companies the freedom to create cost-effective, scalable, and interoperable digital transformation roadmaps. Open standards have accelerated innovation outside of cement; we must also fully embrace this practice as an industry.
Cybersecurity
Many industrial automation systems are typically older, unpatched – and thus more vulnerable to – cyberattacks, which was perhaps OK when they worked in isolation. However, advancing digitalisation and connectivity are exposing these systems to greater risks. Industry 4.0 is built on cloud computing. Typically, many AI providers structure and execute their solutions in the cloud. They run their algorithms and then send the outcome (set points and predictions) back to the plant. The IT and OT systems from Industry 3.0 were simply not designed for this as there was much less need for data exchange, which kept the risk of cyberattacks much lower.
Certainly, plants can open up the flow of data, but this is an extra step that tends to act as a speed bump. Although some have matured the ability to send data to the cloud, very few have the systems to take data back at the required speed and scale. Partnering with an experienced supplier who can design a secure architecture and implement best practices is key. We are confident of this need as we have been getting frequent requests for assistance from our customers. In fact, there were so many enquiries that we were inspired to launch a specific service package for cybersecurity assessments.
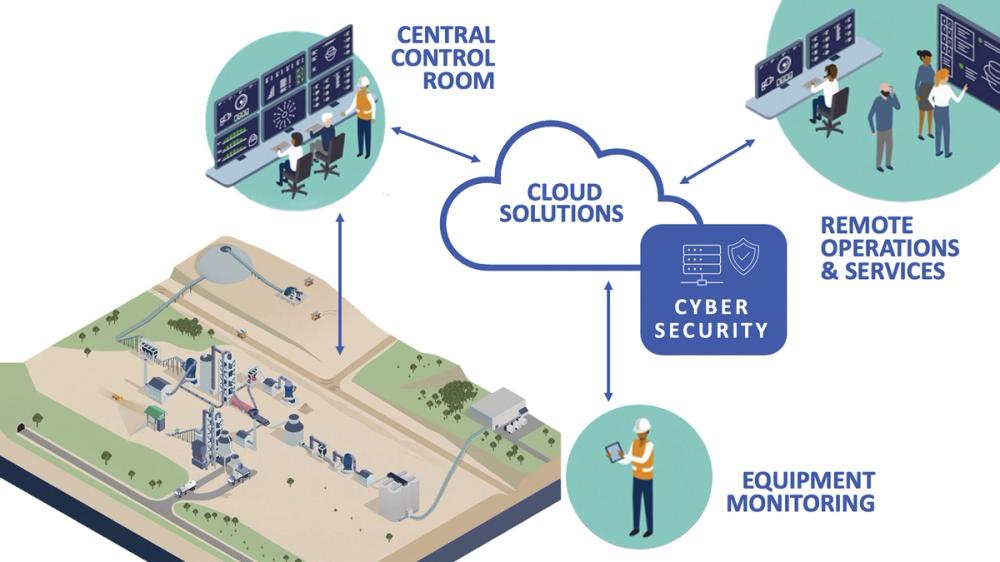
Organisational readiness; review KPIs
To fully harness the potential of next-generation Optimization solutions, all KPIs must be aligned so that the Optimization systems and algorithms are configured to give plants what they really want. However, in working with plants, we often uncover competing priorities which can make everything more complicated and impede the best overall outcome. What is the right trade between maximising alternative fuels in order to save money, versus getting better clinker quality such that more substitutions can be used to reduce CO2, versus getting a stable and ideal flue gas to enable carbon capture? It is unlikely that you can get them all perfectly achieved at the same time, but which should be prioritised over the others? And who decides?
For a given project, we usually have a primary contact at our customer. Sometimes that person will guide us to design a system that will achieve their own KPIs without full consideration for the greater good of the entire plant. It is not intentional or self-serving. Rather, I believe it is just organizational growing pains because Industry 4.0 and plant-wide optimization thinking is not yet fully part of our cultures. Consequently, at times, we have found ourselves playing the role of a detective to get the clarity and alignment needed so that we can deliver the best overall solution.
Move to business models that fit the speed of innovation
In Industry 3.0, the normal Go-to Market strategy consisted of selling software with a perpetual license. This model was widely accepted as a best practice by everyone involved. Our customers owned the software outright, and we, in turn, received full payment upfront. Our competitors did similar. However, updates were not automatic and plants often found themselves running with somewhat outdated versions.
To stay competitive, cement producers no longer have the luxury of waiting for a major upgrade to adopt new features - things are moving too fast. Consequently, we have transitioned to offering our software as a subscription-based service as opposed to a one-time purchase. In other words, rather than owning software, a plant receives an optimising service that includes software and proactive monitoring of performance. This concept has been well-received by plants, however many have had the extra administrative hurdle of adapting their approach to budgets and purchasing KPIs. Furthermore, in the same spirit of delivering continuous performance, we have seen an uptick in enthusiasm for our PlantLine™ Service Agreements which include secure, trouble-free support with 24/7 coverage and customisable modules for cybersecurity, remote technologies, lifecycle management and proactive maintenance.
Conclusion
Plants that fully adopt Industry 4.0 will have a powerful competitive advantage, accelerating efforts regarding productivity, decarbonisation, quality cost savings. Much of the technology is already available. And, with the right strategy in place the obstacles can certainly be overcome. Start by assessing your plant’s digital maturity today, in particular, your OT systems. Conduct a data, cybersecurity, and Sampling and Lab audit, then work with industry experts to implement the next generation of advanced process control. The sooner you take action, the faster you’ll unlock efficiency gains and sustainability improvements. The future of cement production is digital – don’t get left behind.
[1]https://www.worldcement.com/indian-subcontinent/18032024/pioneering-the-global-cement-industry/