article
Quick win in the quest to reduce CO2
Clinker is the most expensive and carbon-intensive ingredient in cement. Optimizing cement’s clinker factor has therefore become a key target for cement companies looking to reduce their carbon emissions – as well as support their bottom line. At Holcim Germany’s cement plant in Höver, a modern automated sample preparation system is providing the foundation for an efficient and consistent process that delivers optimal product quality with lower environmental footprint.
Every tonne of cement produced with a higher-than-specified clinker factor is money out of the window. On the flipside, every tonne of cement produced that doesn’t meet the target clinker factor is also costly. In the past, cement producers would err on the side of caution and include more clinker than was needed to meet specification.
But with the urgency to limit the impact of climate change, it has become more important than ever to make sure clinker use is optimized.
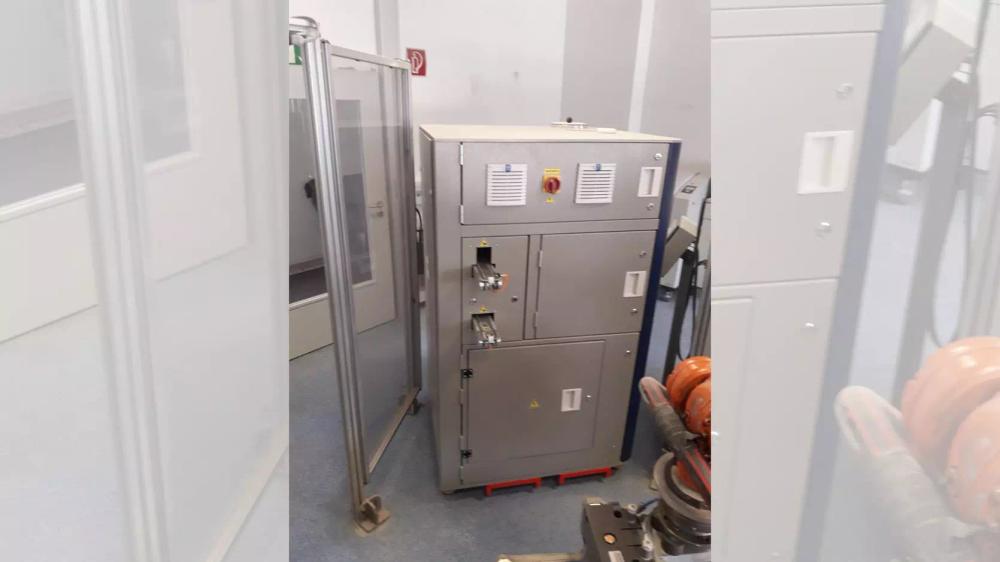
QCX/RoboLab® systems: industry’s best cement laboratory automation
"There is no doubt that optimizing your clinker factor is a quick win and an efficient way to improving the environmental footprint of cement production," says Dr Benecke, Production Manager at Höver plant, which is part of LafargeHolcim, one of the most carbon-aware cement companies in the world.
Take this example: a plant produces CEM I cement with a specified clinker factor of 95% to 100%. The closer the plant can get to a clinker factor of 95%, the lower its OPEX and environmental footprint will be.
In fact, a 3000 tpd cement plant that brings the clinker factor of its cement just one percentage point closer to the lower end of the specified range would reduce its emissions of CO2 by 23 tonnes per day – the equivalent emissions of a Volkswagen Passat driving around the world 4.6 times.
At Höver cement plant, optimizing the clinker factor has become a daily journey towards a more sustainable production. Helping the plant on its way is a new FLSmidth Cement QCX Centaurus combined mill and press. Responsible for automatically preparing samples for analysis, the Centaurus may not be the most glamourous or cleverest piece of equipment in a cement plant. It is more of a workhorse than an Arabian thoroughbred. But that does not make it any less vital.
The QCX Centaurus is able to prepare about 60 additional individual samples per day than the previous system used at cement plant Höver. And the more samples prepared and analysed, the better picture the plant has of the cement that is being produced, and the better able they are to ensure a consistent quality.
“With today’s modern equipment for sampling, preparation and analysing, we are able to continuously adjust the compositions of our cement and constantly stay on target for the type of cement we are producing,” Dr Benecke continues.
The added sampling capacity provides other benefits too.
“Increasing sample throughputs with the QCX Centaurus has ensured better control of the kiln process and minimized the safety buffer in process control, so that we experience a higher efficiency - in the range of about 2% – leading to lower emissions and fuel savings. Consistent samples are also an unavoidable pre-requisite for quality control, when alternative fuels are used,” explained Dr Benecke.
FLSmidth Cement QCX Centaurus provides consistent sample quality by reducing cross-contamination to a minimum. It is user-friendly with a modular and accessible design that allows for easy maintenance in the often space-constrained laboratory environment. Furthermore, its flexibility enabled a seamless integration and interaction with the existing lab infrastructure.
“The Centaurus is well-known for its quality, capacity, ease of use and reliability in sample preparation,” said Michal Krsek, Product Manager at FLSmidth Cement. “These qualities helps bring new levels of consistency and quality to cement operations with benefits that go beyond the bottom line to help address the most pressing challenge facing the industry: sustainability.”