article
Remote commissioning finally enables ECS/ControlCenter™ implementation at Messebo Cement after a seven-year delay
In 2018, we delivered a modern ECS/ControlCenter™ automation solution to upgrade a manually operated system at Messebo Cement in Ethiopia. However, civil unrest delayed system commissioning, putting the project on hold until the plant contacted us again in 2024.
We have enjoyed a strong, long-term relationship with Messebo Cement since we supplied equipment for the plant’s first production line around 2000. Located in Ethiopia’s northern Tigray state, the plant now supplies various Portland-type cements and a low-heat high-sulfate-resistant (LHHS) cement, operating two production lines at a combined capacity of 7000 tpd.
Messebo Cement approached us to upgrade Line 1 with an automated control system in 2016/17. The original system engineering for the upgrade was completed in 2017 and included a switch from discrete digital and analogue boards and mimic panels to a modern ECS/ControlCenter process controls system. The system was delivered to the plant in 2018.
Not long after, long-running local tensions bubbled over into armed civil unrest, preventing system commissioning. It would remain safely and properly stored at the plant until June 2024, when Messebo Cement got back in touch and asked us to restart the project.
Remote capabilities enable project restart
Ongoing travel restrictions and security concerns still prevented onsite commissioning. However, our remote commissioning capabilities and experience had developed significantly since 2018, and we decided to proceed on that basis, supported by Messebo Cement’s extremely competent local technicians. Well-preserved project documentation on our servers, a coordinated Division of Responsibility (DOR) list, and an onsite precheck of the parts system further enabled this approach.
During commissioning, we relied on our remote access tools and Microsoft Teams to help the onsite team set up the system. This included visual validation using live remote access and video connection to assist with configuration and verification steps. “Thanks to excellent cooperation and dedication from the onsite and remote teams, commissioning was executed smoothly,” said Bjarne Andreasen, who managed the project for FLSmidth Cement.
The cement plant’s digital heart
Our ECS/ControlCenter automation platform is the digital heart of the cement plant: an advanced, reliable, adaptable, secure software package that provides the foundation to control everything from machinery to full processes. It enhances productivity by ensuring equipment runs consistently under optimal conditions. By reducing operator error, it also minimises unplanned downtime. This keeps throughput high while boosting efficiency and output.
Meanwhile, our proactive service module and advanced cybersecurity protect the control system from unexpected stoppages. Ultimately, it ensures the plant operates at its best, guaranteeing the lowest cost per tonne of production.
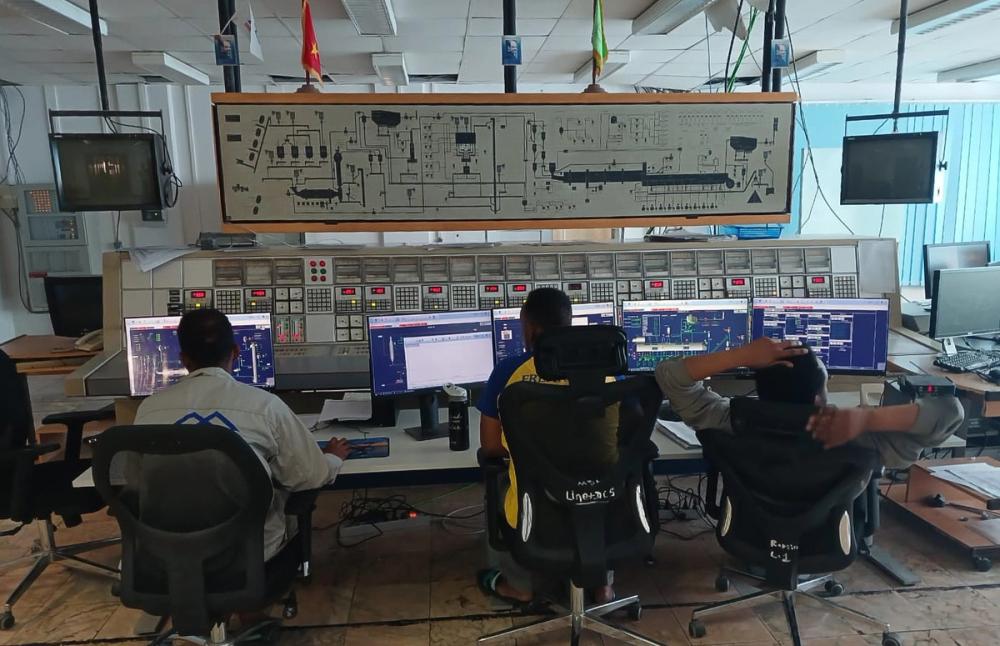
Setting the standard for remote commissioning
Opting for remote commissioning, we navigated various logistical and safety concerns, setting a benchmark for remote commissioning in challenging environments. Remote commissioning also avoided the cost and delay of travelling to hard-to-reach locations, allowing Messebo Cement to finally enjoy the benefits of a modern control system seven years after it was first delivered.
“We are grateful to FLSmidth Cement for working with us to commission the system remotely and are very satisfied with the results,” said Messebo Cement’s CEO, Mr. Kibkibre.
FLSmidth Cement and Messebo Cement are now looking to expand this new way of working to other areas, including optimising plant processes and quality with a PlantLine™ Service Agreement.
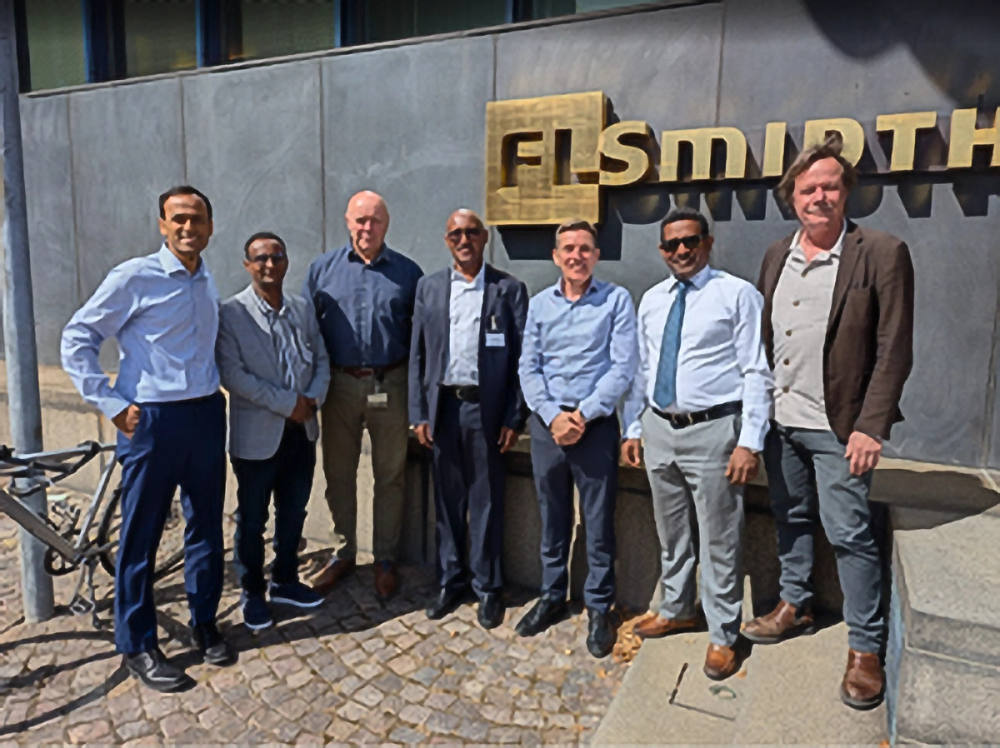