article
The impossible upgrade made possible
Yanbu Cement and FLSmidth Cement have proven that two production lines running on PLCs from different vendors and older I/O’s can be upgraded and controlled from one common control platform. This increases productivity and knowledge sharing between operators.
From the control room at the Yanbu Cement Company in Saudi Arabia, the operators now oversee and control production lines 4 and 5 from the same application. As trivial as this may sound, it is the effect of an upgrade process that other suppliers had deemed impossible.
Yanbu Cement Company was experiencing an increasing amount of downtime, especially on line 4 which was running on old ABB Bailey infi90 components and an ABB 800XA control system. This system was about 25 years old. In addition to the downtime resulting in a loss of production, spare parts were becoming increasingly expensive and time-consuming for the company to procure.
Upgrading the entire production line was considered, but as line 4 itself has about 25,000 I/O’s, this would require scheduling a longer downtime resulting in a loss of production and revenue, as well as a large capital expense.
“We are always on the look-out for productivity gains. Upgrading the automation system was part of an optimisation of our plant that began as a retrofit of our burner system. Together with FLSmidth Cement, we analysed the potential for productivity and quality enhancement across our plant. It turned out that upgrading the control layers would prolong the life of the I/O devices securing the best return on investment,” says Amr Nader, COO - Chief Strategy, Operations & Industrial Excellence officer.
Amr Nader, COO, Chief Strategy, Operations & Industrial Excellence Officer, Yanbu Cement Company
Productivity benefits of common control
The operators at Yanbu also had a strong wish to be able to control both line 4 and 5 from the same central control system. This would save the operators time and increase productivity of the two lines. However, as line 5 was running on Siemens’ SIMATIC PCS7 control system based on S7 400 PLCs, the operators had been told that this was not an option. But a visit from FLSmidth Cement’s sales team made them think differently.
“Combining legacy ABB and Siemens systems into a common platform is far from a plug-and-play solution. But as cement production is our core business, our approach is to look at the possible productivity level of the plant and then work our way down through the technical requirements in order to make it happen. This way, the technology supports reaching the targets instead of limiting them. And even though it was not a simple solution, this approach led us to find a solution that lets us control the two lines at Yanbu from one central control system,” says Rizwan Sabjan, Deputy General Manager-Global Sales Support, Group Digital, FLSmidth Cement.
Amr Nadar also stresses the benefit of choosing a supplier with cement as its core business.
Amr Nader, COO, Chief Strategy, Operations & Industrial Excellence Officer, Yanbu Cement Company
New programming based on cement library
The common control platform is now ECS/ControlCenter V8 from FLSmidth Cement.
ECS/ControlCenter already works well with Siemens PLCs, but to connect the old Bailey controllers required the team to think outside the box.
Rather than ditching the old controllers, they added a few Symphony Plus Bailey-compatible controllers to replace the oldest of the existing ones. On top of that, they added an extra layer of new Siemens S7-400 PLC s and panels, servers and engineering and operator stations. New ethernet switches, fibre-optic cables and media converters make it possible to get data from the existing I/O’s into the Siemens controller used in the ECS/ControlCenter V8 platform.
“For this to work, we had to redo the entire PLC programming and process interlocking for both lines. The programming is based on FLSmidth Cement's comprehensive cement library called ACESYS (Adaptable Control Engineering System), and the operators and engineers shared knowledge with us while the system was being built. As the solution for line 4 had never been tried before, we ran a thorough preliminary test at site, and then we ran a complete factory acceptance test at FLSmidth Cement using the systems-integrated device simulation function,” Rizwan Sabjan explains.
Yanbu Cement has one central control room for both lines, using ECS/ControlCenter™ V8 as the common control platform.
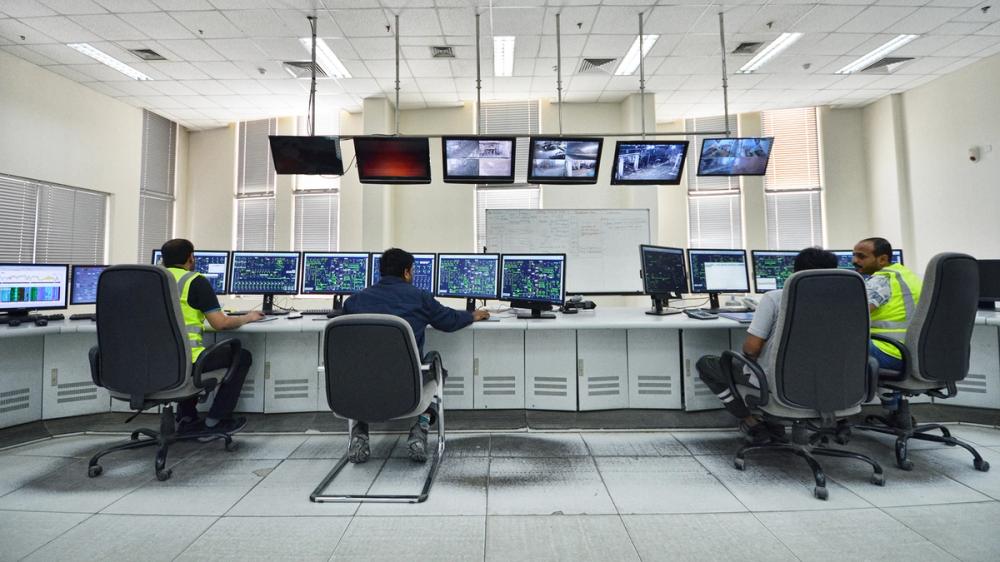
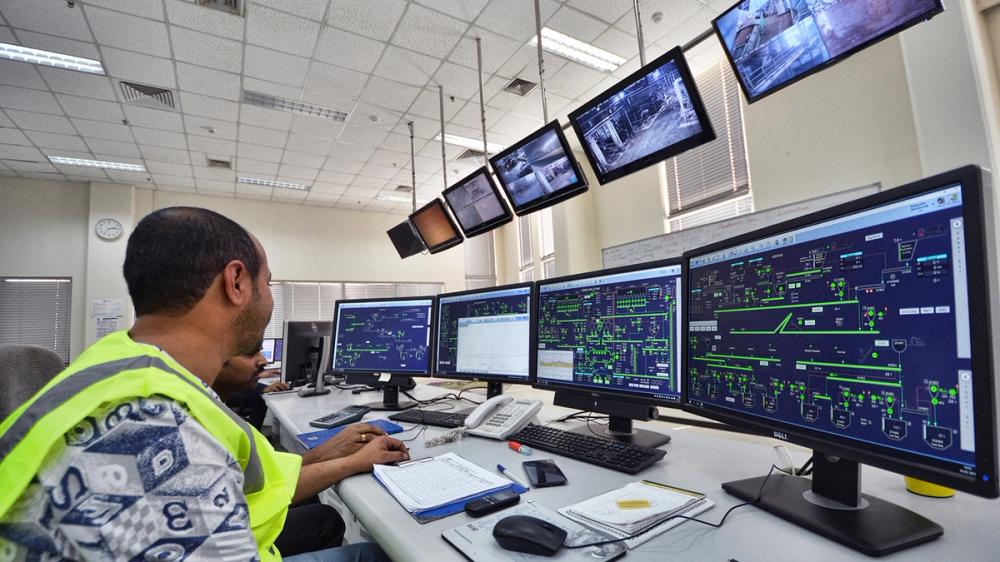
Operators share more knowledge
FLSmidth Cement’s ECS/ControlCenter V8 was already capable of integrating with the existing Siemens controllers of line 5, yet updating the programming using the ACESYS library now means that the operators have full access to the features in ECS/ControlCenter V8 to optimise the operations.
“FLSmidth Cement makes efficient and clear process displays that help the operator to keep the process running smoothly. The feel of the V8 layout is engineered to be superior to the existing PCS7 and 800XA, using the human-optimised equipment symbols based on the ACESYS v8 standard. This makes it easy to operate,” says Mohammad Aly, Optimization Manager and Project Head of the upgrade from Yanbu Cement Company.
Yet another benefit is that fewer operators are needed to operate the system, and that knowledge is easily shared:
“As simple as it may sound, sharing data and knowledge across a plant is the best way to optimise production, and this has become a lot easier. When our team finds ways to optimise production on one line, this knowledge can immediately be implemented on the other line as well,” Aly says.
Due to the thorough tests and great co-ordination between the project teams from FLSmidth Cement and Yanbu, the implementation was delivered within the scheduled shutdown period without any extension and with no effect on the planned production. Following the upgrade, downtime on line 4 has been reduced even though the old I/O´s are still in place.
About Yanbu Cement
Yanbu Cement Company, a Saudi joint stock company, is one of the major cement manufacturers in the Kingdom of Saudi Arabia and the largest cement company in the Western Region. They have a total installed capacity above 7.0 million tonnes of clinker and cement dispatch capacity above 10 million tonnes per year. Yanbu Cement is ranked as one of the top 50 companies in KSA with a paid-up capital of SR 1.575 billion.
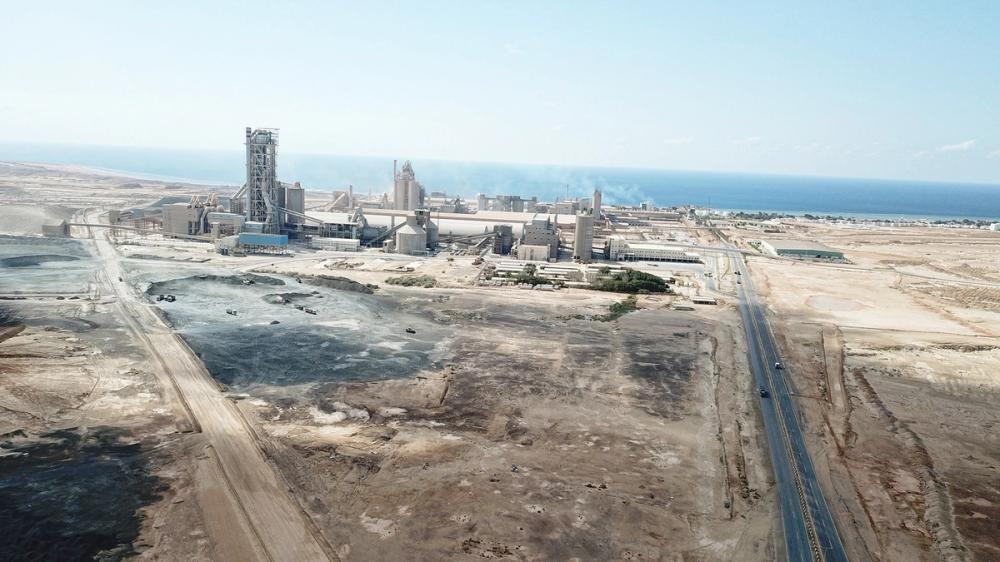
About ACESYS Cement Library
ACESYS v8 (Programming Standard) is a Cement Library created by FLSmidth Cement with the following unique features:
- Same look and feel irrespective of any PLC hardware (Rockwell, Siemens and Schneider).
- Structured PLC programming with standard object making maintenance engineer job easy to pick and use.
- In-built device simulation blocks helping conduct FAT (Factory Acceptance Test) 100%, so complete process interlockings are tested prior to system installation at site with no surprises during commissioning.
- Root cause analysis at face-plate level which helps the operator to conclude the reason for tripping and reduce the downtime of the plant.
Related Offerings