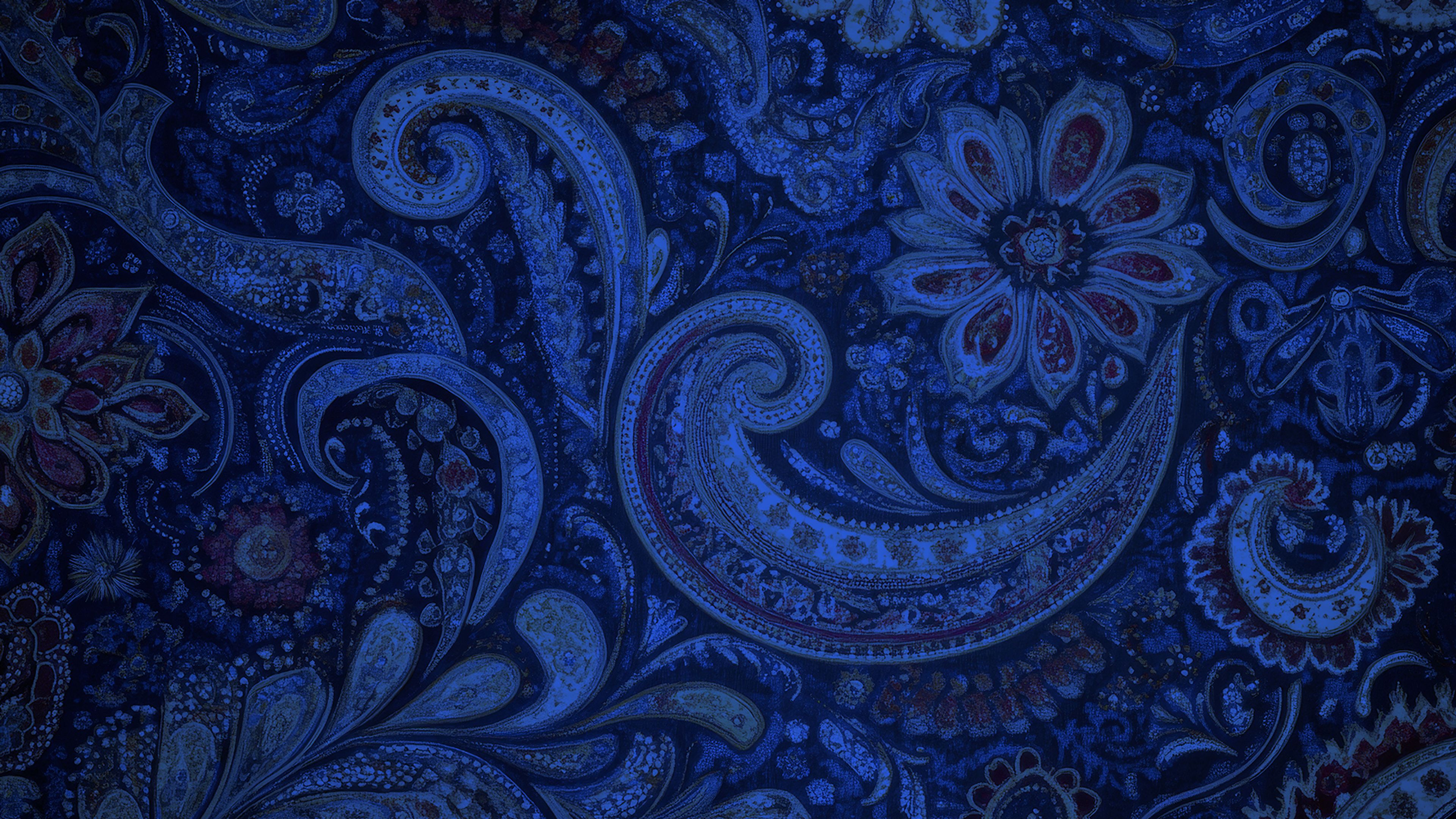
NCB
02
2024
New Delhi, India
Cementing the Net Zero Future
FLSmidth Cement NCB में भारत में
0
0
0
0
Paper #1 by Lars Kuur
Delivering SCMs with large-scale potential in the context of the Indian market
This paper reviews global trends and regional specifics to inform these decisions, focusing on the potential of Supplementary Cementitious Materials (SCMs) like calcined clay to reduce CO2 emissions. Using a Technology-Organization-Environment (TOE) framework model, the paper analyzes the factors influencing SCM adoption in the Indian cement industry, considering technological readiness, organizational challenges, and environmental pressures. It also explores the norms and acceptance in the market and operational implications of SCM integration such as material handling, supply chain logistics, and the risk of stranded assets. The importance of market dynamics and regulatory frameworks in driving SCM adoption is emphasized, particularly in India’s high-demand, resource-constrained environment in which a relatively high substitution rate is already found. The paper advocates for a strategic approach that balances immediate operational needs with long-term sustainability goals. It highlights calcined clay’s potential as a transformative SCM for the Indian market, offering economic and environmental benefits, such as reduced CO2 emissions and lower energy consumption. Additionally, the paper underscores the necessity for adoption of recent technological innovations and policy support to maximize the impact of SCMs, ensuring that the industry is well-positioned to meet both current and future challenges. A perspective is built against carbonation as a next-generation carbon capture and SCM enhancement technology and the potential of grinding to enhance SCM performance. By providing a comprehensive analysis, this paper equips the industry with knowledge and strategies needed to navigate the challenges and opportunities of the green transition, for a step towards the sustainable future for the Indian cement industry.
About the Author
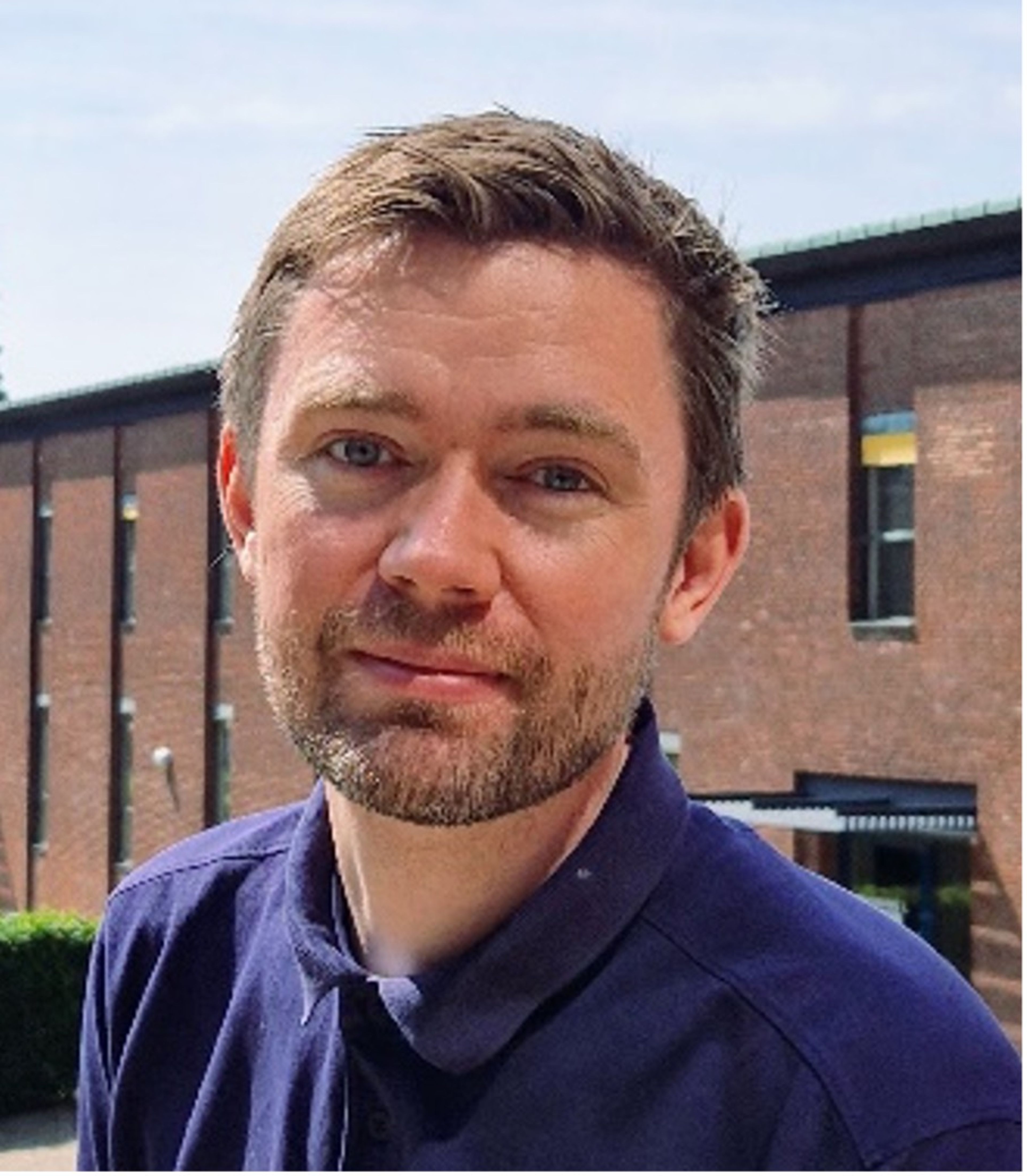
About the Author
Lars Kuur
Program Manager, Clinker Substitution
Starting as a mechanical field installation engineer with FLSmidth in 2011, Lars has helped realize projects worldwide on a gradually larger scale and more senior roles until finishing the traveling life as Site Manager on full-scope lines. With a distinctly hands-on approach and an insistence on understanding the technical details, he transitioned into the role of Capital Sales Manager, bridging needs and solutions for customers' large CAPEX projects. Finding interest in the Calcined Clay and general Clinker Substitution space, he is today rooted in FLSmidth green innovation in an overarching role of connecting the commercial needs of the customers and the FLSmidth R&D efforts in the role as Program Manager – Clinker Substitution. With his background as an MSc in Thermal Energy and Process Engineering, he has profound respect for the technical complexity and difficulties the plant operators face when journeying towards the green transition while ensuring their profitability and stability.
Interested in a conversation?
Meet me at NCB.
Paper #2 by Robert Krist
How feeding and dosing technologies contribute to reducing carbon
Energy efficiency, clinker reduction and fossil fuel replacement are the three central pillars of existing methods to reduce the cement industry’s carbon footprint. Though feeding and dosing equipment is a relatively small part of a cement plant’s operating budget, it can have a big impact on the process – and in particular on these three areas. This article will explore how feeding and dosing equipment contributes to a lower carbon cement process, with examples from real-world applications. Cement manufacturers worldwide are looking for opportunities to reduce CO2 emissions and achieve their sustainability targets. While carbon capture will undoubtedly feature in the industry’s future, it’s important for cement producers to take measures now to bring emissions down and progress towards carbon neutral cement production. Energy efficiency, clinker reduction and fossil fuel replacement are the three central pillars of existing methods to reduce the industry’s carbon footprint. FLSmidth Cement’s Pfister® brand is contributing to all three through energy efficient dosing and feeding equipment, helping to increase alternative fuels utilisation, reduce fossil fuels use, and create low-carbon cement mixes.
About the Author
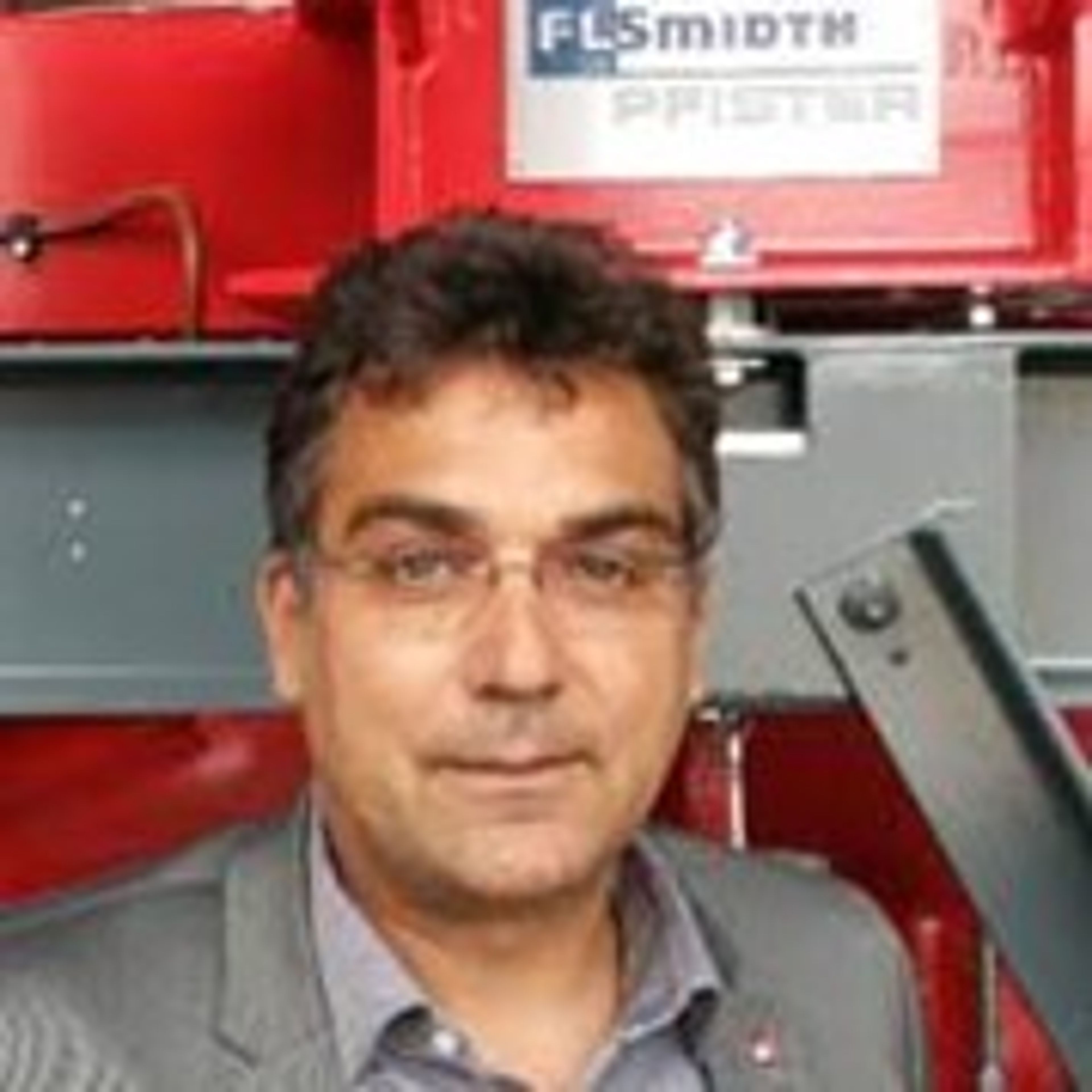
About the Author
Robert Krist
Head of Sales Feeding & Dosing, FLSmidth Pfister GmbH, Germany
With nearly 30 years of experience with dosing and feeding solutions in the cement industry – 25 of those with FLSmidth Cement, Robert Krist is one of the driving forces behind our efforts to enable our clients to start reducing carbon emission in cement operations by today. The use of new and existing alternative raw materials – to reduce the clinker factor as well as alternative fuels are key focus areas on our journey towards a CO2 neutral cement production.
Interested in a conversation?
Meet me at NCB.
Paper #3 by Kiranmai Sanagavarapu
Technology and Solutions for Enhanced Thermal Substitution Rates
Alternative fuels are a relatively straightforward and readily available means of reducing a cement plant’s carbon footprint. The technology is proven and well used worldwide, and with the right controls in place the switch from fossil fuels to waste-derived fuels does not impact the quality of the end product. In some countries, cement plants are achieving near 100% substitution in the calciner and high levels of substitution in the kiln. However, this trend is not universal and in India, the targeted thermal substitution rate (TSR) is relatively low at 25%. Still, this target is proving difficult for some cement plants to meet. In this paper, we will look at the obstacles to alternative fuel use and the technology that is available to overcome them.
About the Author
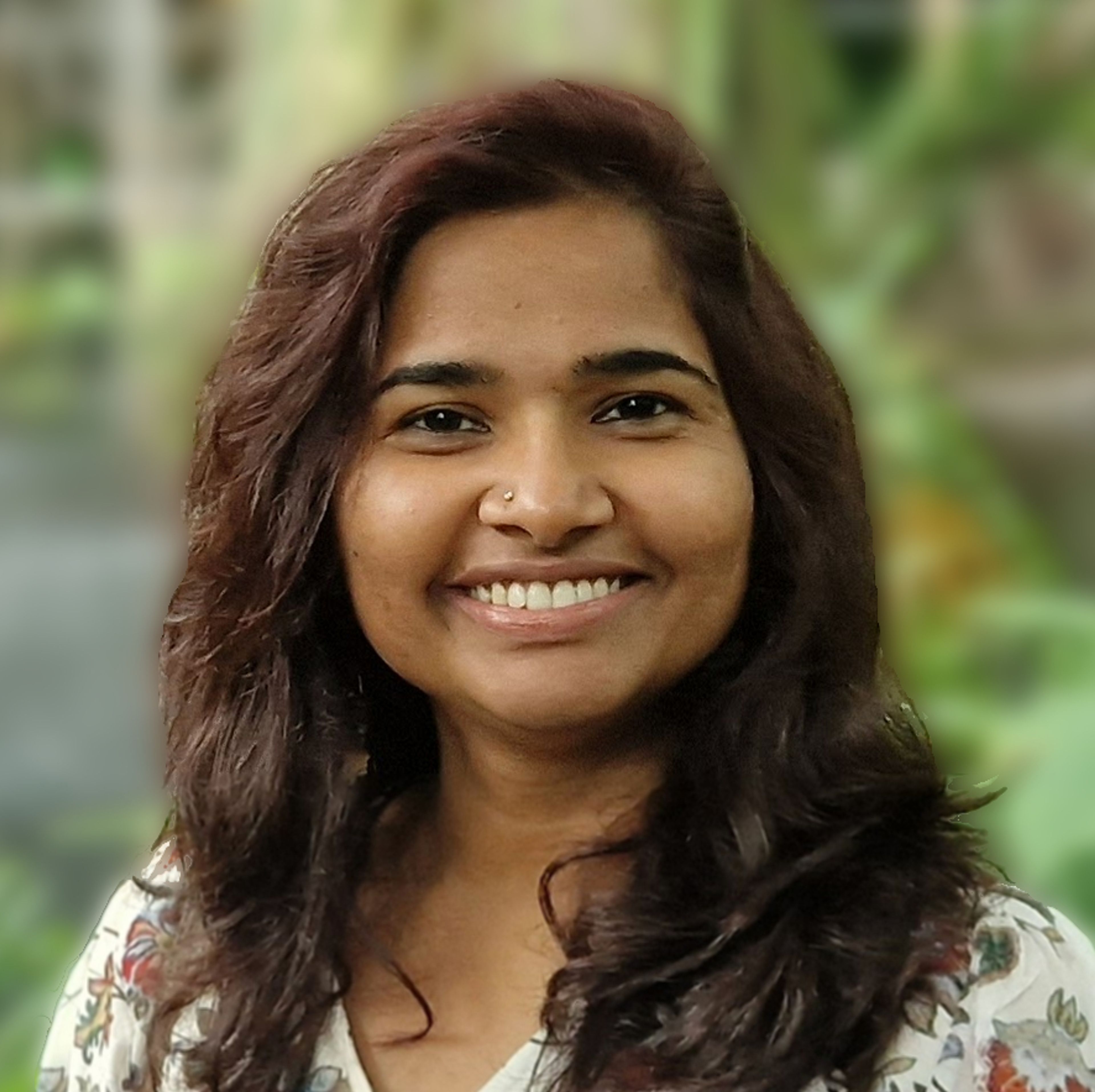
About the Author
Kiranmai Sanagavarapu
Program Manager, Clinker Decarbonisation
Kiranmai began her journey at FLSmidth as a Sales Engineer, specializing in upgrade projects, and has since held key roles such as Proposal Engineer, Process Design Engineer for the Cement Industry, and Global Product Manager for Grinding products. Her current role involves overseeing critical projects related to Clinker Decarbonization, showcasing her commitment to sustainability within the industry. With a background in process engineering, Kiranmai has been instrumental in sizing equipment, materials evaluation, and optimizing existing cement plant operations. Her expertise extends beyond technical aspects, as she has served as a technical advisor for Project, Aftermarket, Product and Service Sales, Erection and Commissioning, Proposal, Plant layout, and Product groups.
Interested in a conversation?
Meet me at NCB.
Paper #4 by Rizwan Sabjan
The digital cement plant
The cement industry lags behind many in exploiting the benefits offered by advanced digital and automation solutions. These include faster, more accurate decision-making based on real-time data, optimised process and quality control – which leads to higher productivity, reduced operating costs, enhanced maintenance and quality, and improved safety – and lower environmental impacts, including support for net-zero goals. This paper addresses some issues involved in cement plant digitalisation, particularly cyber security, a growing concern as cyber attackers increasingly target industrial operational technology (OT) and information technology (IT) networks. Securing OT systems poses several challenges. The industry must be aware of these risks and take proactive measures to ensure the security of their systems, such as cybersecurity assessments and lifecycle planning for critical digital and automation solutions. The paper then provides an overview of some digital technologies enabling the digital cement plant. The digital foundation is the plant control system, which provides the basis for implementing other advanced digital and automation systems. More advanced digital solutions build on the functionality of the plant control system and include advanced process control systems, data analytics and visualisation via plant data management solutions, and online condition monitoring and remote services via secure data transfer systems. Laboratory automation and optimisation are also briefly discussed, including the difference between process and quality data and the issues this raises when selecting a laboratory information management system (LIMS). Like the plant control software in the broader plant, LIMS provides a basis for advanced cement laboratory automation solutions, such as automated sampling and transportation, automated sample preparation and analysis, and chemical quality control. It is also noted that cement plants do not follow a uniform approach to digitalisation. It is advised to work with an expert and experienced automation solutions provider to develop a digitalisation strategy tailored to the needs and current capabilities of the specific cement plant.
About the Author
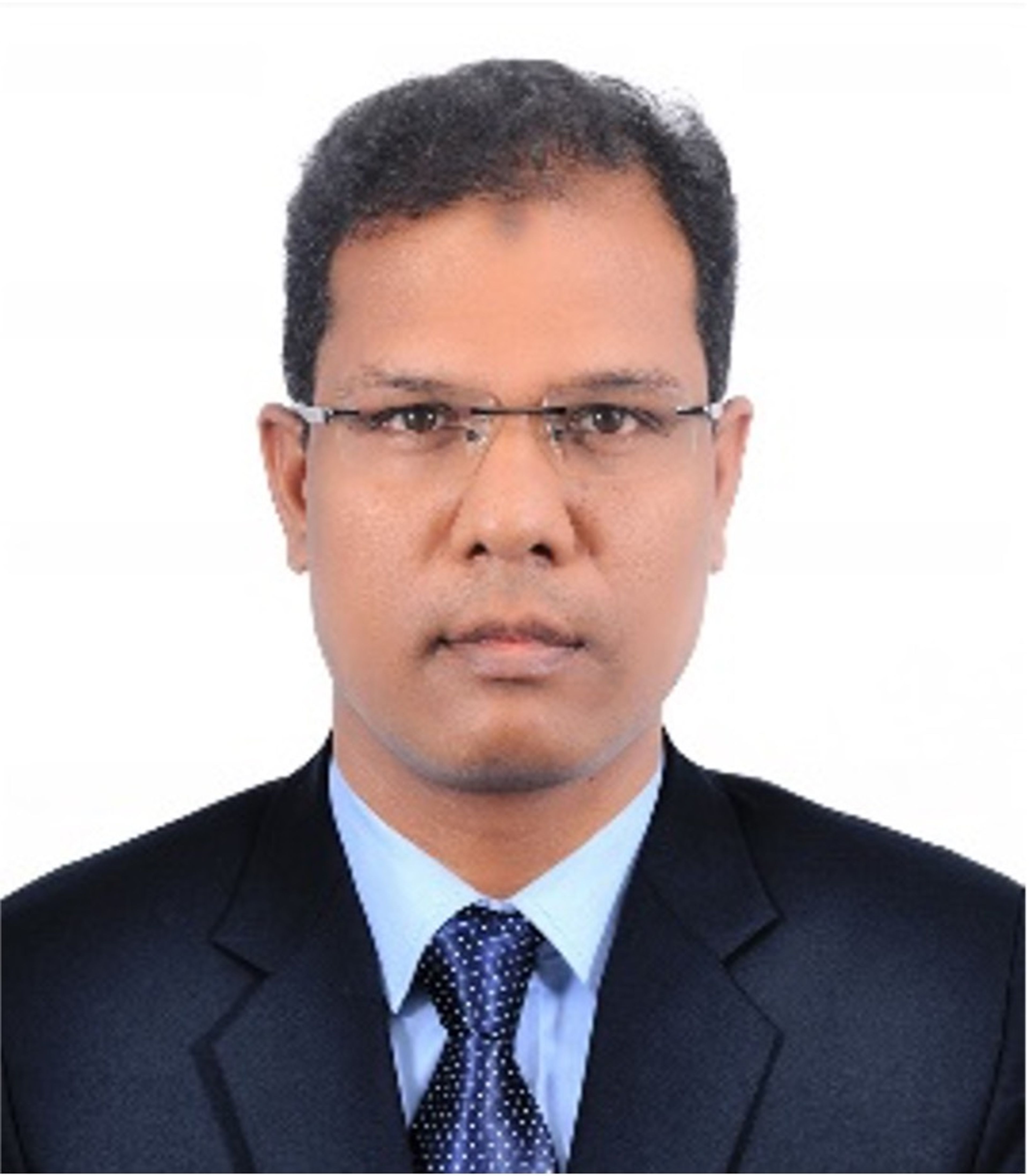
About the Author
Rizwan Sabjan
Head of Sales & Proposals, India
With over 26 years of extensive experience in industrial automation, I am a dedicated and passionate leader committed to integrating automation technology with process domains to create value for my customers. I have hands-on experience in delivering automation solutions across diverse industries, including machinery, chemicals, power generation, food, cement, and mining. My areas of interest and enthusiasm encompass driving digital transformation, the Internet of Things, condition monitoring, artificial intelligence, and uncovering new opportunities through customer engagement.
Interested in a conversation?
Meet me at NCB.
Our team at NCB
Looking to connect before the conference? Click on a profile to schedule a meeting with one of our experts.
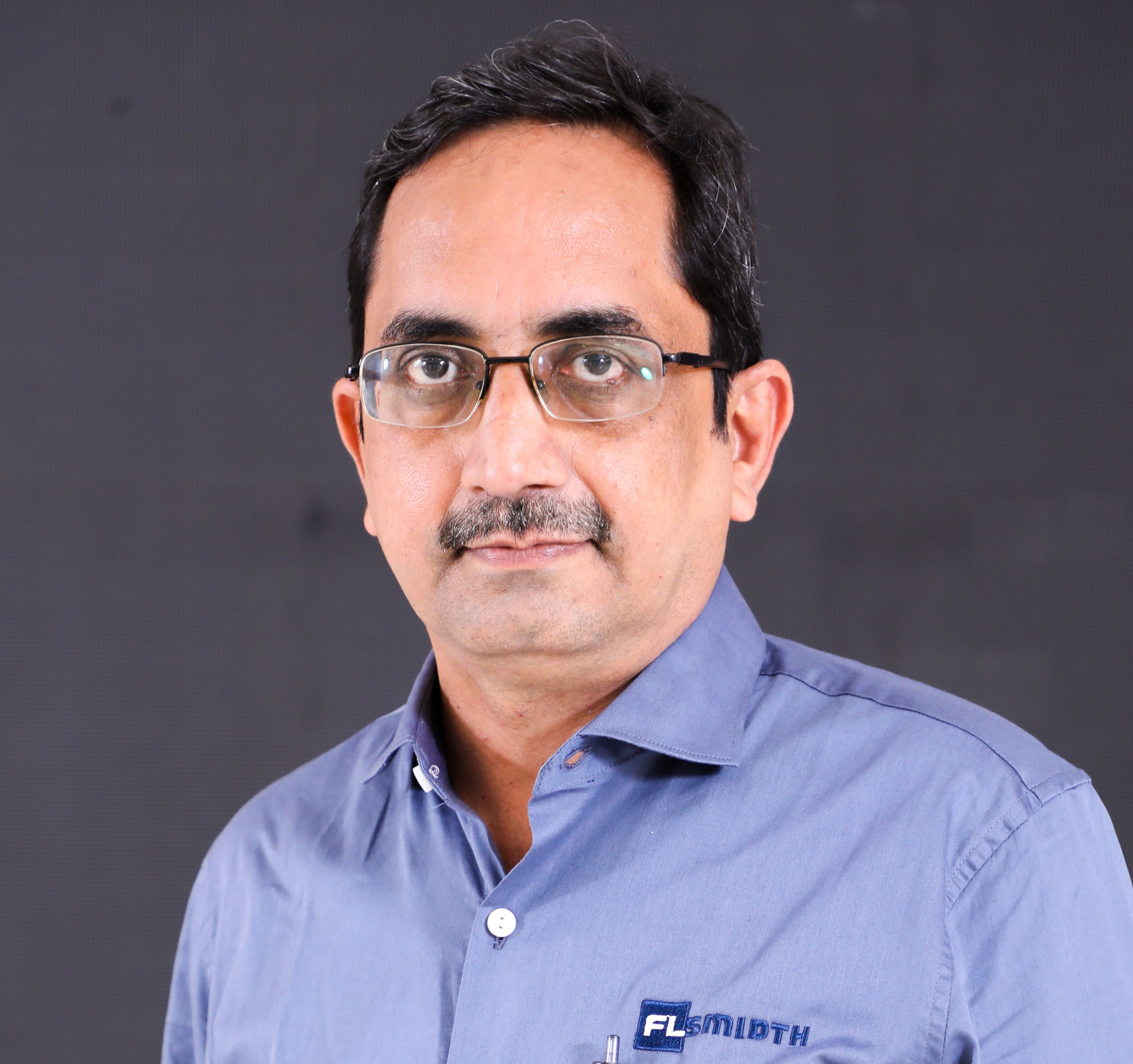
Ramakrishna Nuti
Global Sales Manager, Automation Technologies
Interested in a conversation?
Meet me at NCB.
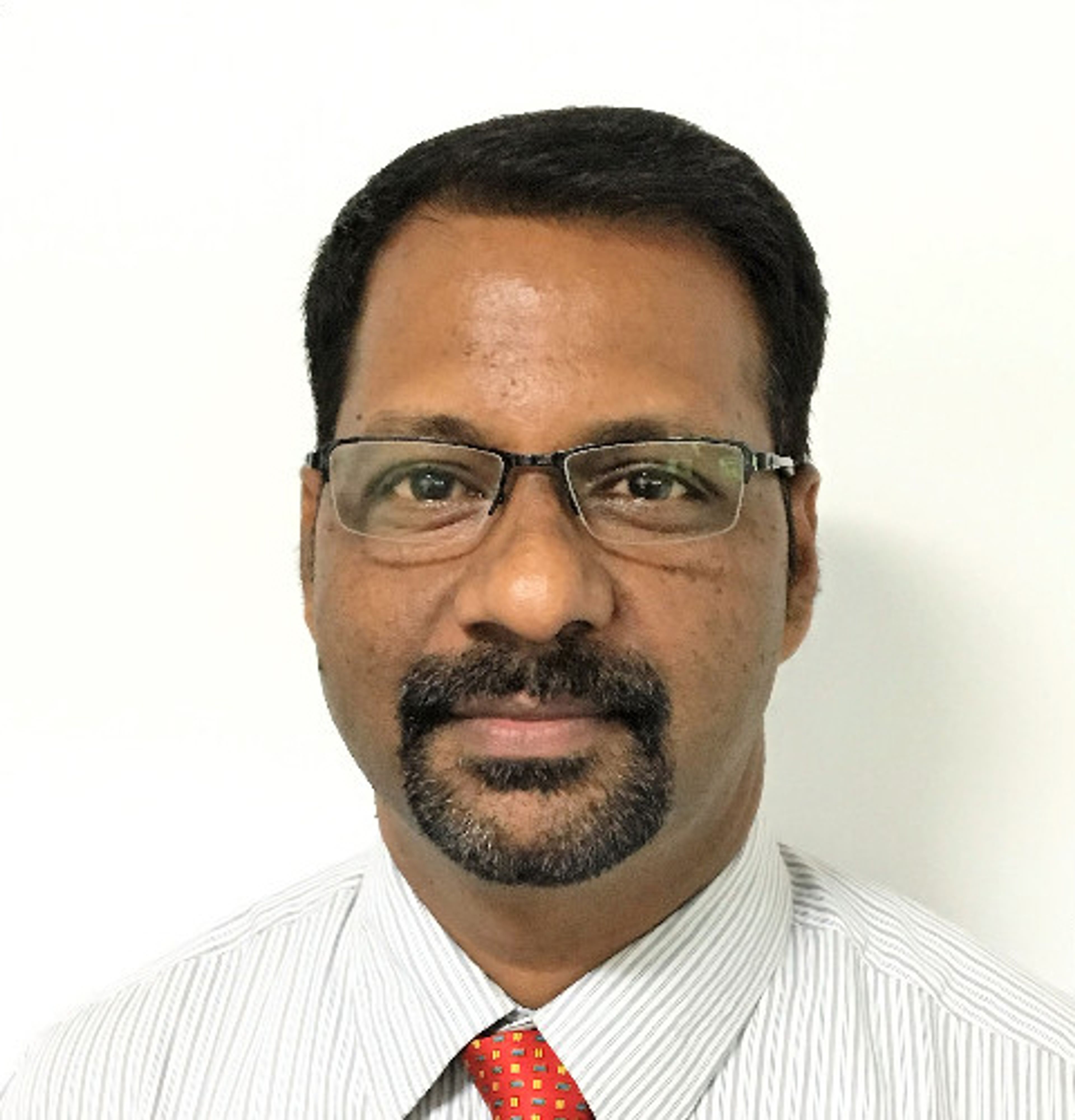
Raveendran Chalil
Head of Service Execution, India
Interested in a conversation?
Meet me at NCB.

Manoj Taneja
Head of Cement, India
Interested in a conversation?
Meet me at NCB.
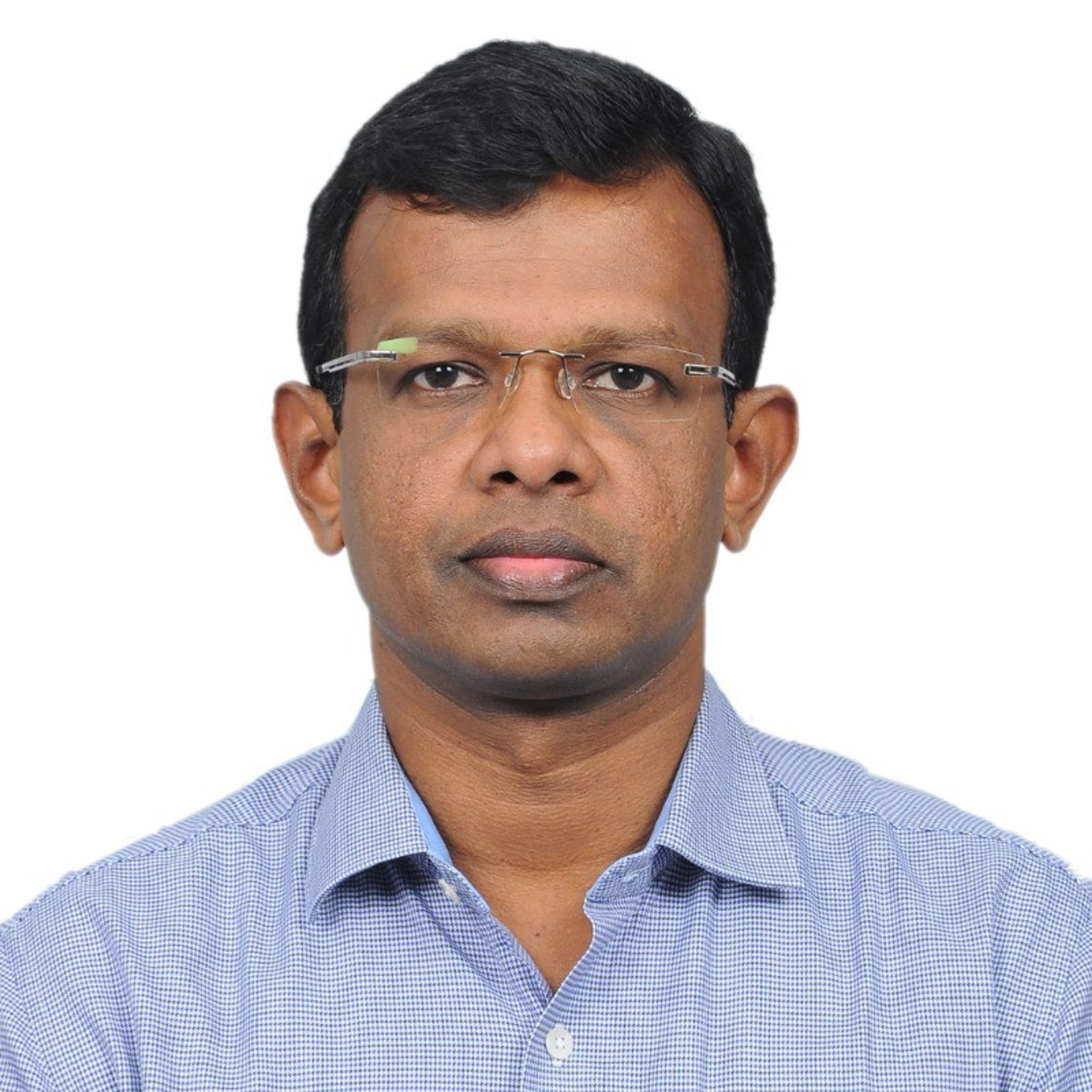
Altrin Prabahar
Head of Sales, Storage, and dispatch, India
Interested in a conversation?
Meet me at NCB.
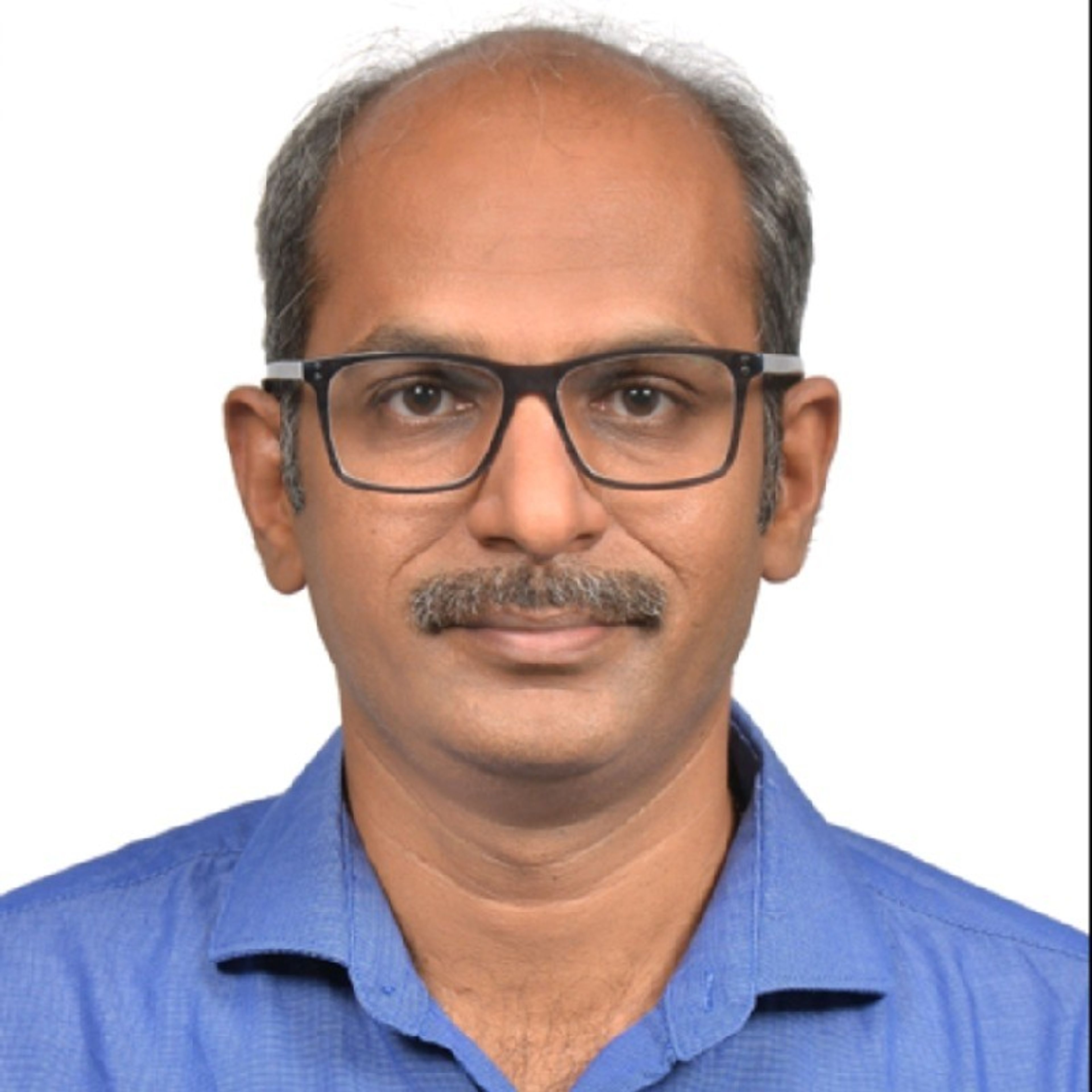
John Soosaialphonse
Head of Green Technology R&D
Interested in a conversation?
Meet me at NCB.

Amin Shaikh
Product & Retrofit Sales, India
Interested in a conversation?
Meet me at NCB.
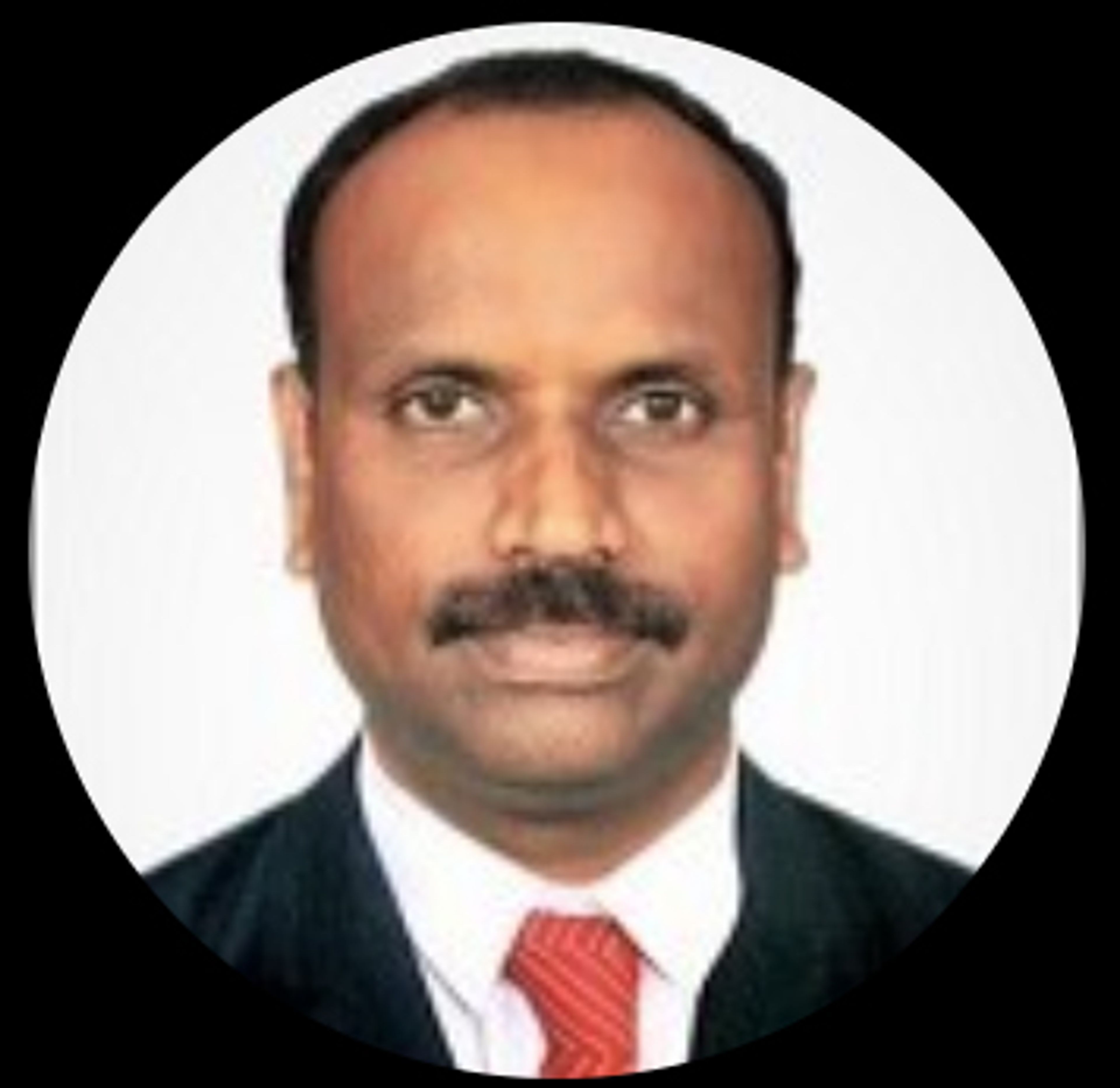
Prakash Durairaj
Facility Management & Indirect Procurement Manager
Interested in a conversation?
Meet me at NCB.
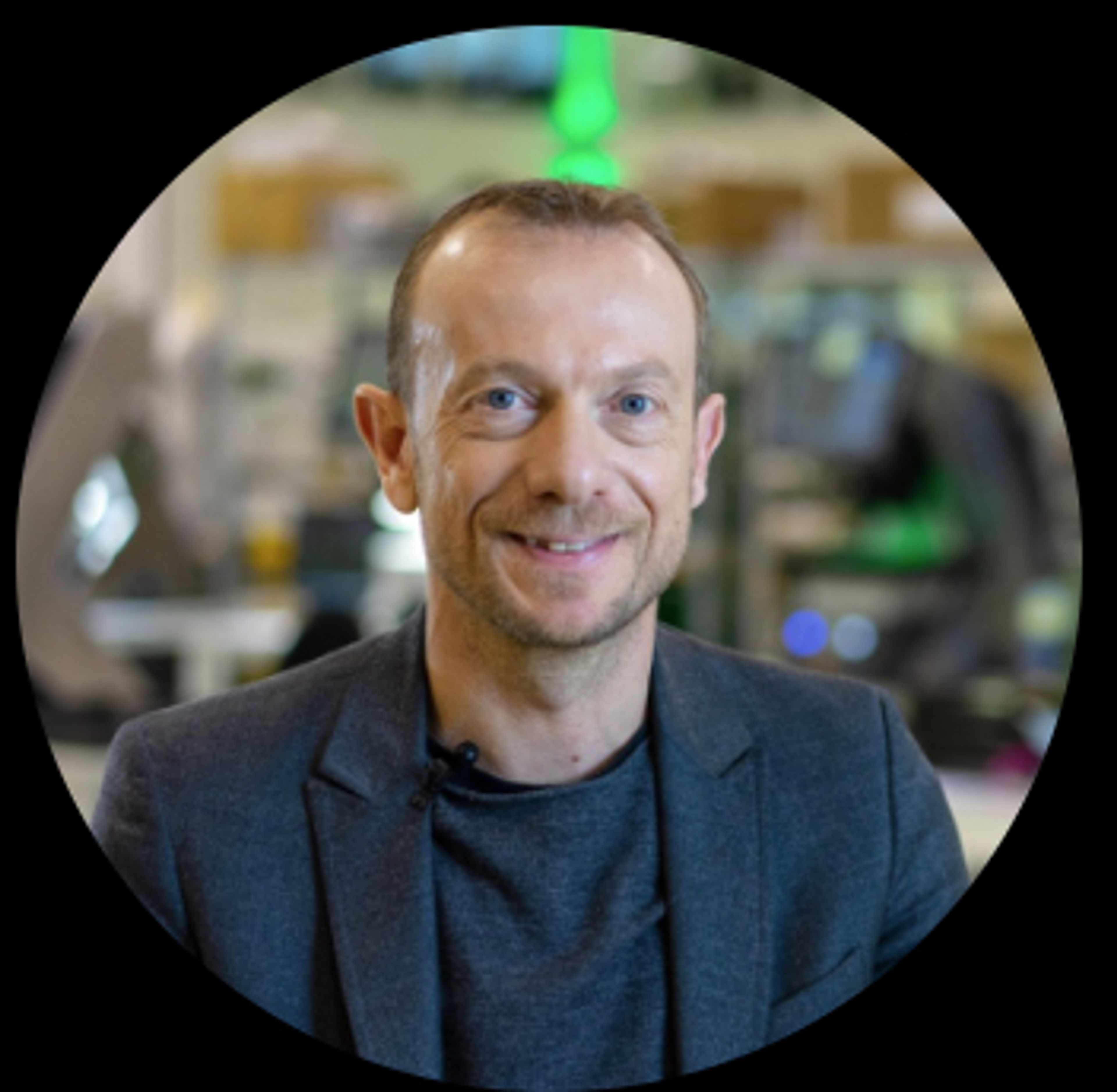
Marco Martinini
Head of Storage & Dispatch Product Line
Interested in a conversation?
Meet me at NCB.
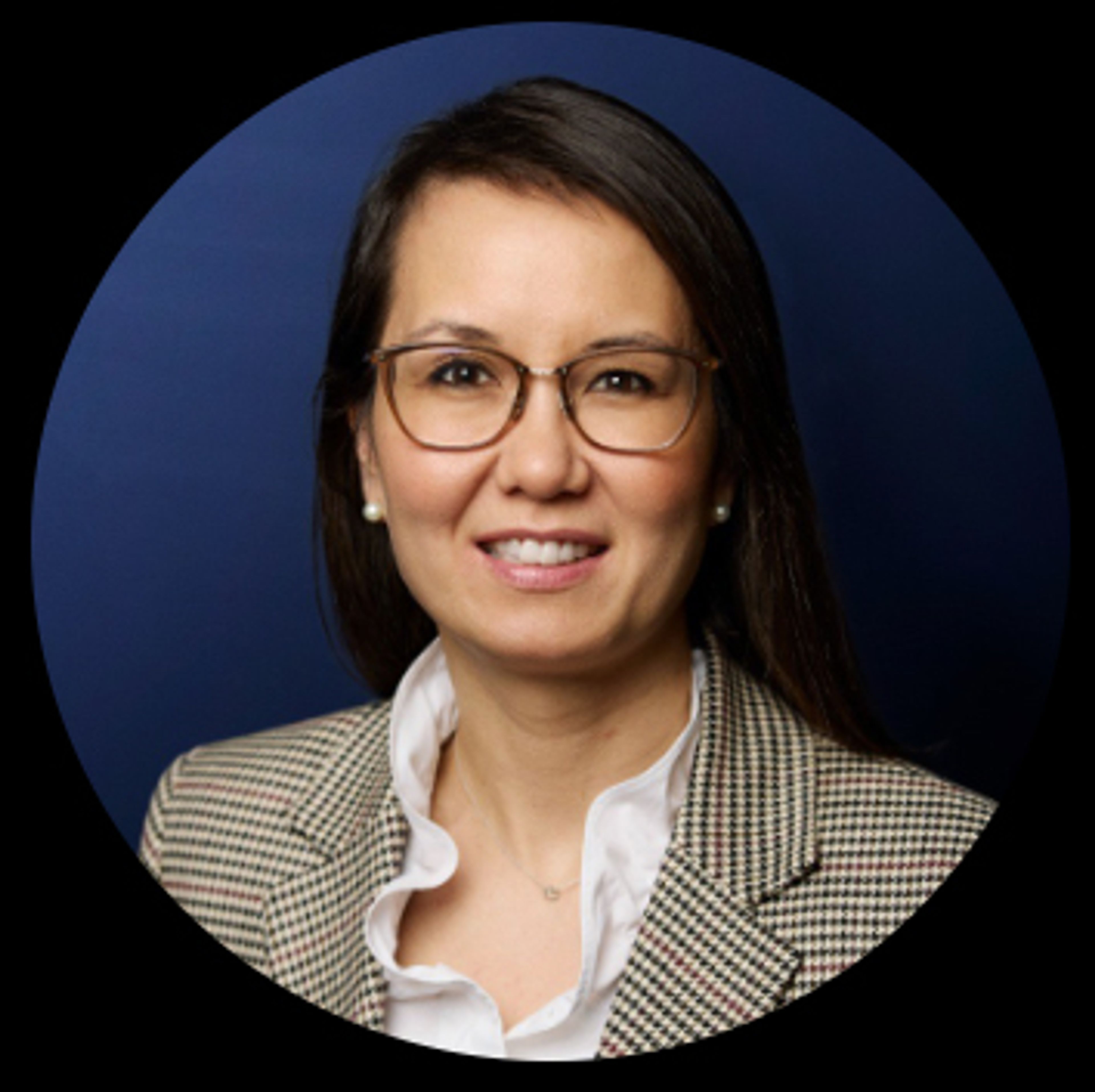
Majken Boennelykke
Head of Transformation and Business Development
Interested in a conversation?
Meet me at NCB.
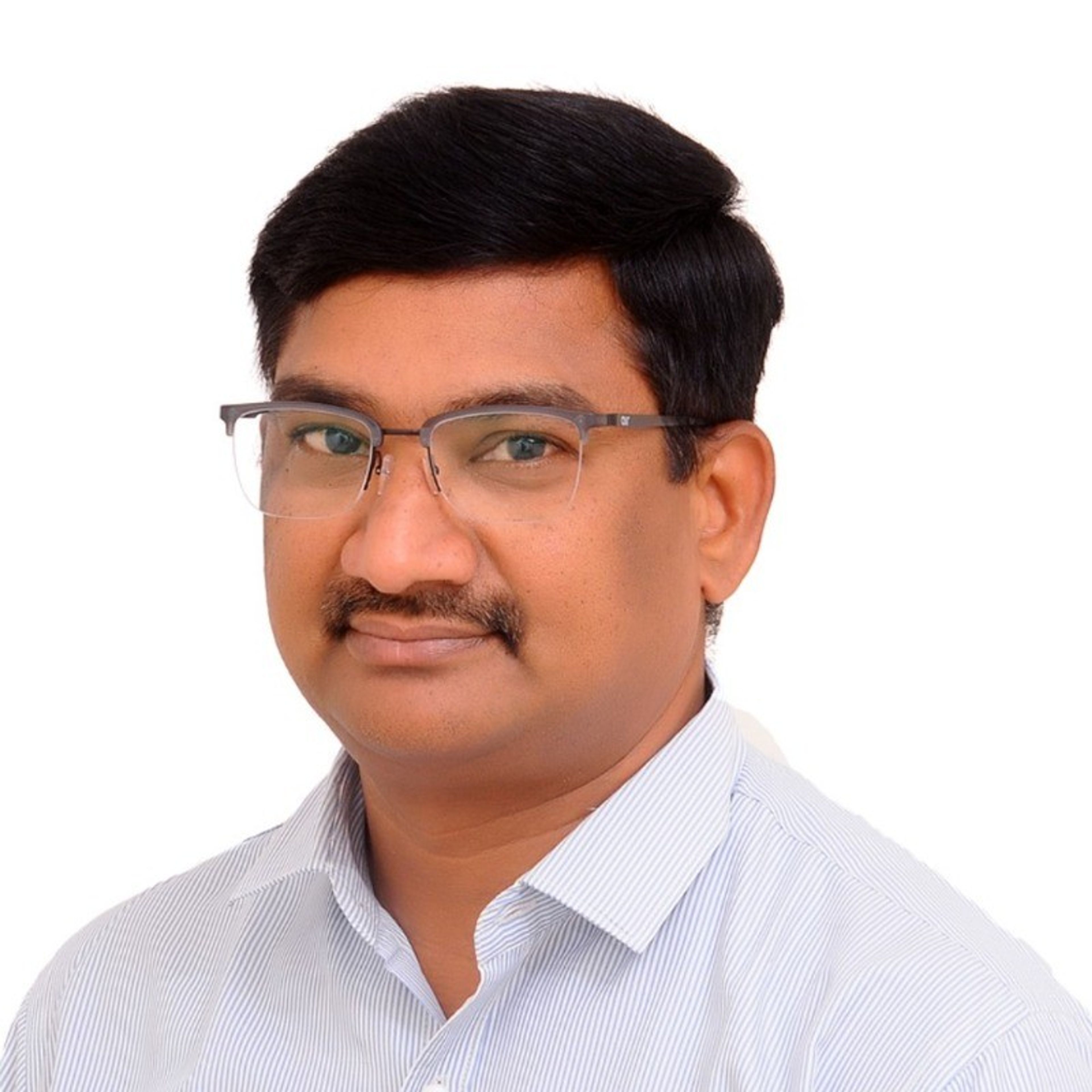
TS Srinivas
Head of Product Engineering
Interested in a conversation?
Meet me at NCB.
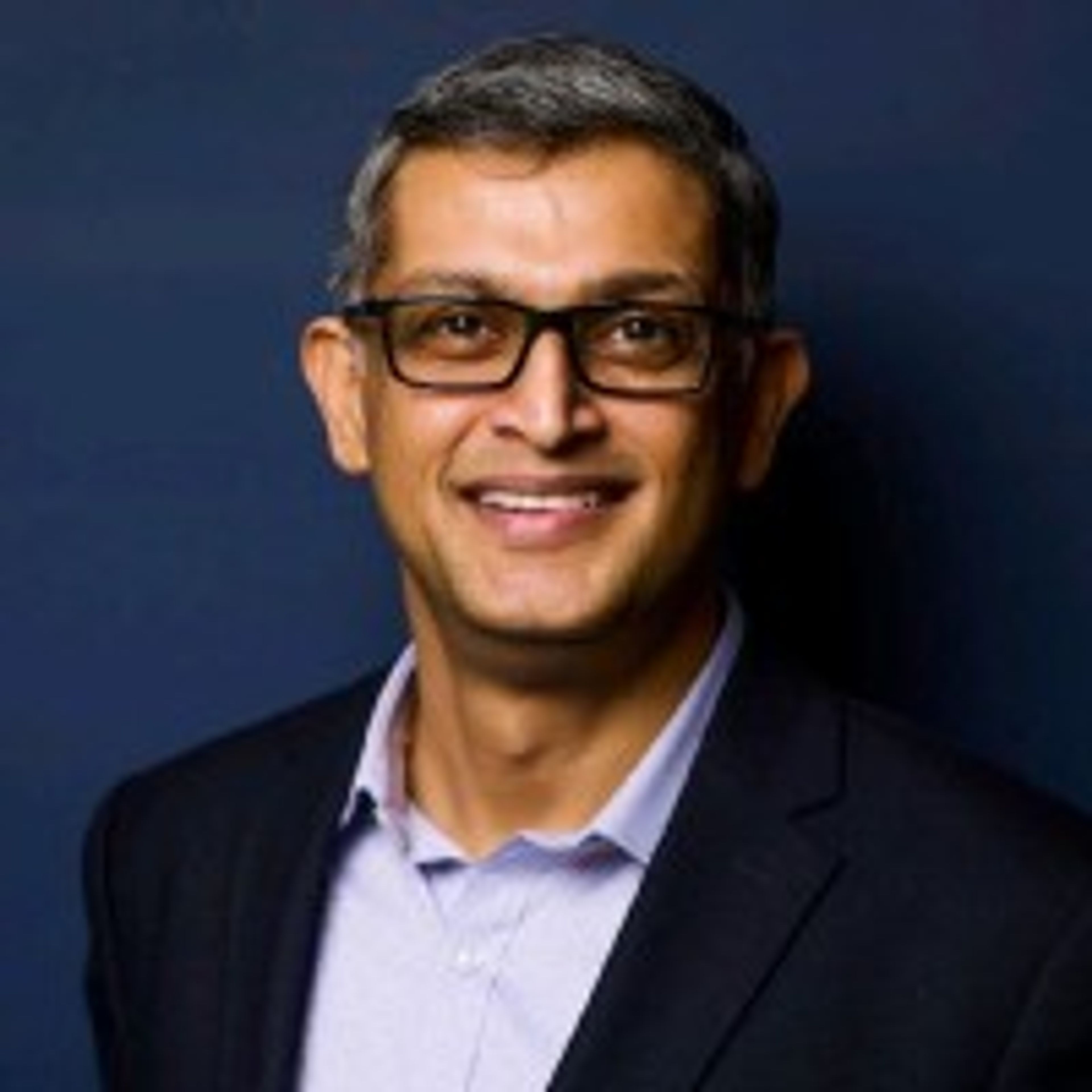
George Xavier
Vice President and Head of People and Sustainability
Interested in a conversation?
Meet me at NCB.
About the NCB Conference
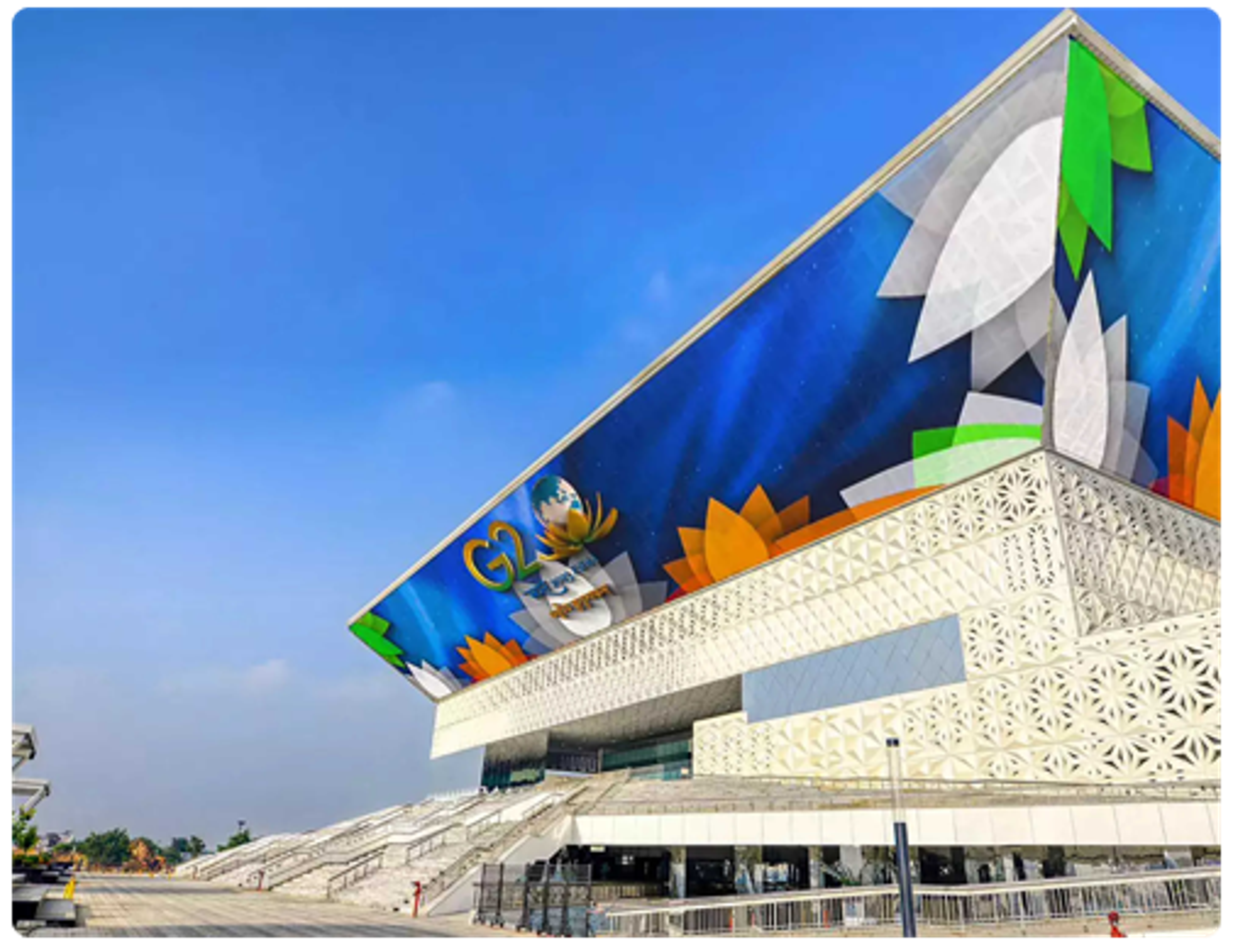
About the NCB Conference
National Council for Cement and Building Materials (NCB), an apex Research and Innovation organization, under the administrative control of Department for Promotion of Industry & Internal Trade (DPIIT), Ministry of Commerce & Industry and dedicated to research, technology development & transfer, education & industrial services for cement, allied building materials & construction industries, is organizing the 18th NCB International Conference & Exhibition on Cement, Concrete and Building Materials from 27 – 29 November 2024 at Yashobhoomi, IICC Dwarka, New Delhi, India, as a follow-up of the Seventeen NCB International Conferences/Seminars organized earlier. The theme of this year's conference is "Cementing the Net Zero Future".
Want to learn more about the conference?
Visit the officia website.