Keep your mill or kiln up and running with our heavy-duty girth gears
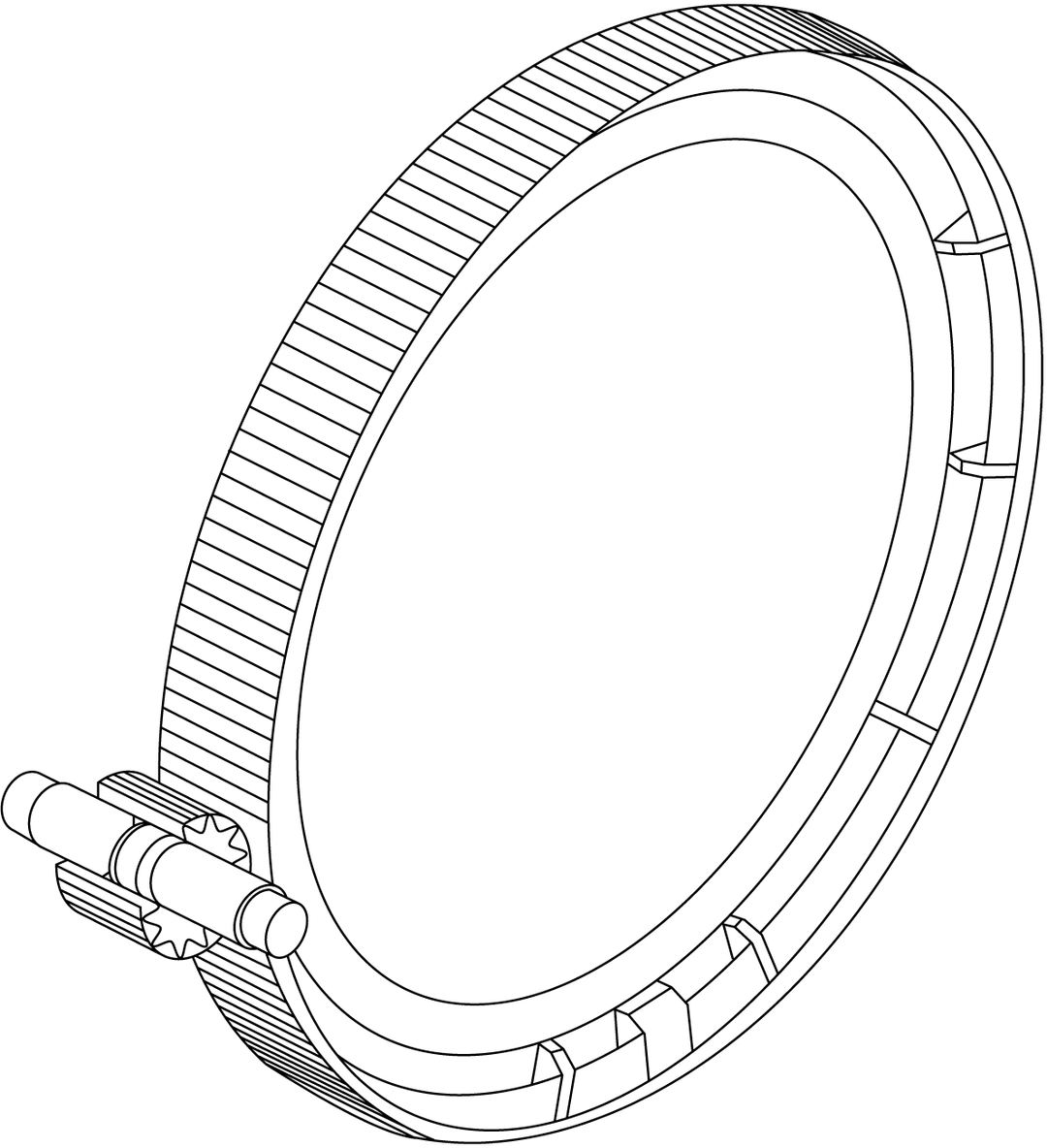
What we offer
Our girth gears let you get the best from your mill or kiln
Our comprehensive expertise in forged gear ring technology comes from our more than 50 years of experience, as well as our collaborations with leading mill suppliers and technical universities. As a member of the American Gear Manufacturers Association (AGMA), we are actively involved in defining the standards for gear-rating calculations, service factors and other design standards. We continuously invest in technology and knowledge – along with steadily strengthening our network of partners. Over 1,000 girth gears are in service around the world – delivering optimal reliability for the cement and mineral industries. Applications for our girth gears also extend into the chemical processing and ceramic industries, food processing and pulp and paper.
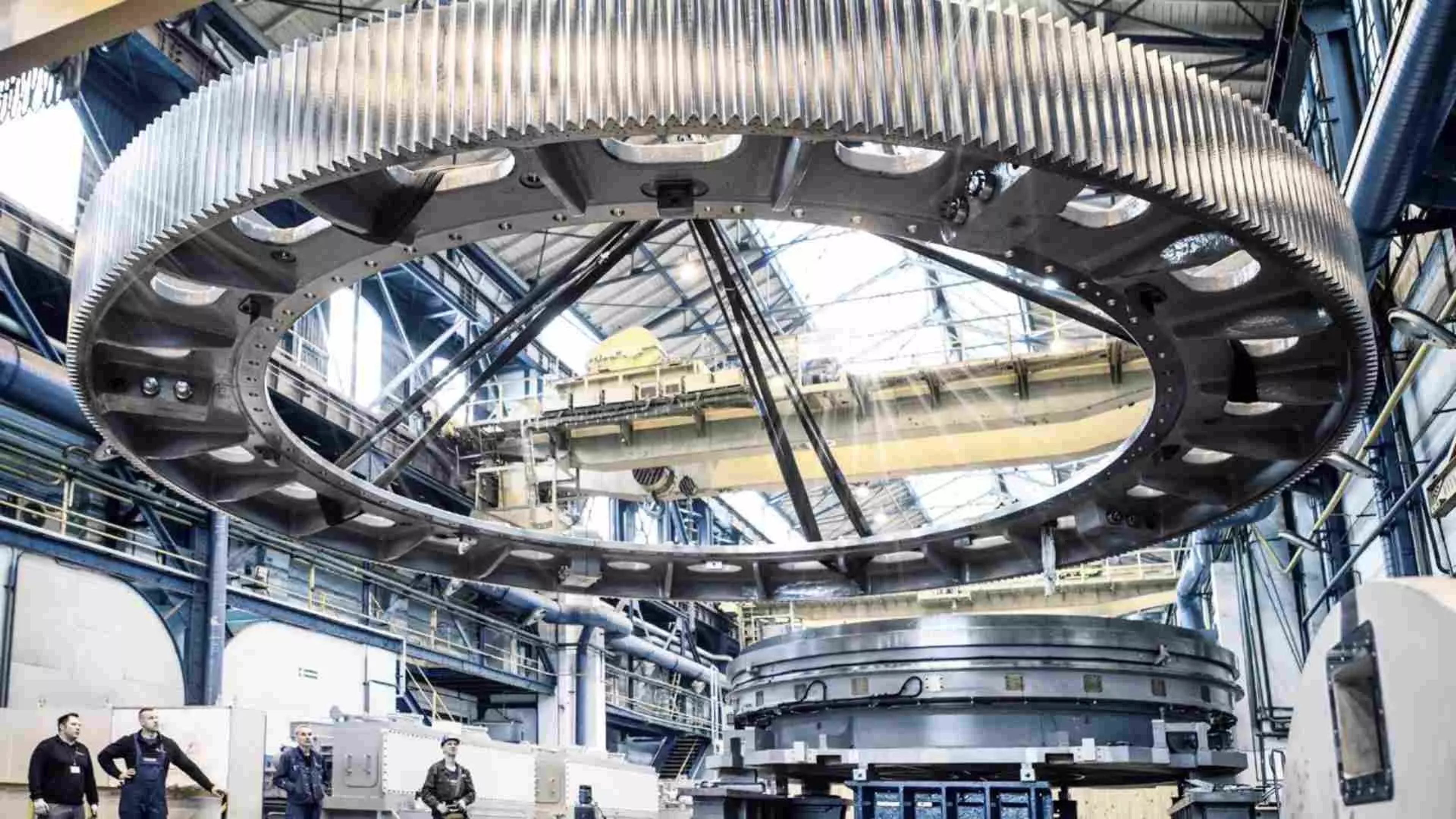
Remarkable raw materials
We build our fabricated girth gears using forged gear rim material and bodies made in an electro-welded structure. Compared to girth gears with cast base material, the manufacturing process is more sophisticated, as well as more reliable. The uniform and homogenous crystal structure of the forged rims, guarantees identical material properties throughout the entire toothing. Casting defects like hot tears, porosity or shrinkage are excluded – resulting in a stronger and more reliable girth gear.
When supplying ductile cast iron or cast-iron girth gears, we source the raw material from world-leading foundries – working closely with them to ensure the highest quality.
Manufactured for high-performance
Our cutting-edge production method ensures that our girth gears deliver optimal power and stable operation for your mill or kiln, along with high wear resistance and long operating time. There are five steps to our manufacturing process for fabricated girth gears, including strict quality checks after the final welding and tooth cutting:
To start, high-grade material is rolled and forged to the required ring dimension. Web, rips and junction plates are welded to the forged rim material according to specific qualified processes. Components undergo strict non-destructive tests, followed by post-weld heat treatment. Rough and finish cuttings trim the girth gear to its final dimension. Finally, the tooth geometry, run outs, hardness and many other properties are measured and documented as part of the closing inspection.
Made for your requirements today and tomorrow
Working to your precise needs, our highly-experienced engineers use the latest finite elements modelling software to design and engineer girth gears that fit your specifications. Our modern production sites and continuous advancements ensure that our girth gears meet your needs now – and into the future.
Smart manufacturing creates durable, fit-for-purpose girth gears
Long-lasting, heavy-duty girth gears
Expert customisations
No risk of inclusions and other irregularities
The strength of our heavy-duty girth gears comes from the strength of our source materials and manufacturing process. We use fabricated steel, forged rings, rolled plates and ductile (nodular) cast iron to ensure the smooth operations for your mill or kiln. The continuous investment in our modern machine shops guarantees state-of-the-art girth gear production, in a wide-range of sizing: External gears: Maximum diameter: 11,200 mm; Face width: 1,250 mm; Maximum module: 45 by hobbing Internal gears: Maximum diameter: 6,500 mm; Face width: 400 mm; Maximum module: 25.4 The precision and quality of the girth gear manufacturing process ensures accurate alignment – resulting in heavy-duty gears that keep your comminution equipment running smoothly now and in the future.